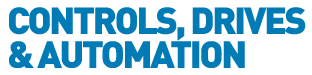
![]() |
Charlotte Stonestreet
Managing Editor |
Home> | AUTOMATION | >Systems | >INTEGRATING ELECTRIC AND PNEUMATIC CONTROLS |
INTEGRATING ELECTRIC AND PNEUMATIC CONTROLS
25 October 2012
Until recently, electrical control engineers have been forced to regard electrical and pneumatic subsystems as separate entities. Jacqui Hanbury, Product Manager at Festo, believes that the end of this segregation is now clearly within sight
However, this is now changing fast. Witness the number of universities offering degree-level courses on mechatronics, and the growth in specialist companies providing multi-disciplined engineering training. The current economic climate is also having a major effect: in response to acute supply pressures, machine manufacturers are being forced to take a fresh look at how they can build systems with less people, in shorter time frames. One obvious way, which many are beginning to adopt, is to develop more flexibility within their workforce, by training their engineers to be multi-disciplined.
ELECTRICS & PNEUMATICS RARELY WORKED WELL TOGETHER
This concept has had a long gestation period. It wasn’t so many years ago that even the very structure of engineering functions within companies conspired to ensure that the disparate worlds of pneumatics and electrics would never meet. At the machine level, this meant that the technologies rarely worked well together – and even when they did, the cost of closing the gap was extremely high in terms of labour. In fact, it was often the case that the two disciplines only came together for the first time at the final system commissioning stages, which is hardly the best time to be resolving critical system integration issues. A typical sorting machine with a series of pick-and-place stations – comprising X-Y electrical axes, pneumatically-operated stop gates and vacuum pick-up devices – provides a very good example of these issues. Such a machine would traditionally be configured with a central PC/PLC, and demand significant time overheads for sub-system integration, wiring and commissioning. During final build, what starts off as a simple task can rapidly become more complicated, as the various feedback systems are incorporated.
Analogue vacuum detection, distance and pressure sensors, etc., will all require separate devices to be built into the control panel and connected; and even if Fieldbus has been employed to help save on wiring, there are still the issues of EDS/GSD type configuration files, addressing and parameterisation to be resolved for each device.
Individually this isn’t a problem, but locating the files, deciphering the documentation from lots of different suppliers and bringing it all together takes far more time than most people realise.
SAFETY REQUIRES A MULTI-DISCIPLINED APPROACH
Machine safety issues also require a multi-disciplined approach.
Consider, for example, a system where half of the pneumatic control valves need to be exhausted in a safety situation, whilst the other half need to be held ‘on’, to ensure that crucial cylinders do not drop, or that process valves do not move. Typically, this can be achieved on a pneumatic manifold quickly and easily, by zoning the pressure. However, the best practice solution would be to also ‘zone’ the electrical power supply, thereby ensuring that even if the pilot valve failed, no power would be available to drive its solenoid.
WHAT TO LOOK FOR IN AN INTEGRATED AUTOMATION PLATFORM
So, given that we are now on the threshold of having control engineers who are happy to embrace electrical and pneumatic systems, where are the multitechnology products they need to make their life easier? Well, they do exist, but it is important to note that not all such products are, or are ever likely to be, equal.
FESTO CPX – NOW WITH CODESYS CONTROLLER
Festo’s CPX multifunctional valve terminal probably comes closest to the ideal – it is still the only product on the market with a backplane bus that spans both pneumatic and electrical functions, some 8 years after it was launched. And since that time, Festo has significantly extended the CPX’s range of pneumatic and electrical technology modules, which now includes a fully synchronous 8-axis controller for electric drives and an asynchronous multi-axis fieldbus gateway. The latest addition is a CoDeSys embedded controller – essentially an industry-standard PLC with additional functionality – which provides a technically elegant means of controlling all the units in a CPX terminal, regardless of whether they are for pneumatic or electric drives, or for I/O functions. Suitable for single and multi-axis applications, the controller can operate autonomously or in conjunction with a host controller such as a master PLC, and can also be used as an intelligent slave in fieldbusbased systems, to provide localised signal pre-processing.
Fully integrated automation platforms offer a wealth of advantages to engineers who are prepared to embrace both electrical and pneumatic disciplines. Imagine being able to combine temperature and pressure measurement side-by-side, with all signals sent via a fast backplane to a fieldbus or Industrial Ethernet (IE) node, or directly to a PLC running a small part of the machine! Other significant benefits include reduced commissioning time and faster, more accurate diagnostics.
Integration in universal networks based on Ethernet opens up a number of new possibilities, especially with regard to additional IT services such as web-based monitoring and diagnostics. At last, with the advent of ‘multiskilled products’, this is a practicable proposition. Engineers are finally free to design machines without having to worry about combining disparate pneumatic and electrical functions.
Festo’s Jacqui Hanbury explains more about the CPX Integrated Automation Platform in this short video: www.bit.ly/cpxvideo
- PPS becomes Festo Official Partner
- Know your poppet from your spool: Free advice on pneumatic valve selection
- Festo celebrates centenary
- A toast to sustainability
- Award winning collaboration
- Putting disabled drivers in control
- Design cartesian robots in minutes
- First UK Cyber Factory training facility
- Productivity concepts
- Solve machine setting issues
- SWISSLOG SECURES MAJOR ORDER
- IMPROVED PERFORMANCE & RELIABILITY
- Engine Facility
- BULK AUTOMATION
- Integrated Packaging Solutions
- Rockwell Automation expands Midrange system portfolio
- Yokogawa joins Friends of the Supergrid
- Festo extends reach of VTUG and MPA-L valve terminals
- Siemens extends TIA Portal engineering framework
- Competence In Automation