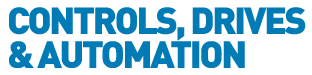
![]() |
Charlotte Stonestreet
Managing Editor |
Living up to machine modularity
05 December 2018
With the combination of a Cube67 Diagnostics Gateway and the straightforward integration of IO-Link, the Murrelektronik Cube67 paves the way toward decentralisation and digitalisation in the cloud using OPC UA
The Murrelektronik Cube67 system advances the trend toward flexibility and is designed for modularity. Already used in over 100,000 machines and plants in diverse industries and applications worldwide, the system boasts an impressive number of different products, many equipped with multifunctional ports that can be configured as inputs or outputs, enabling flexible installation concepts that are customised for number of IOs at the sensor/actuator level.
A major advantage of the Cube system is the “one cable strategy" whereby both communication and power are carried over just one system cable. This leaves cable channels and energy chains available so they can be designed smaller from the start, or even eliminated entirely. The six-pole M12 connector also eliminates the possibility of wiring errors.
Up to 32 modules can be connected to each bus node, using four lines within an installation radius of 60 m, making the Cube system perfectly suited for even extensive installations. The lines are protected by integrated electronic fuses (MICO), the proven Murrelektronik current monitoring system. This saves space in the control cabinet by removing the need for circuit breakers.
The complete portfolio of modules ranging from protection level IP20 to IP67 and even IP69K is available for installations. Meanwhile, the communication only ever runs through a single bus node, which can also be swapped out depending on the protocol in use. As a result, it is also possible to “change the protocol without changing the system.” In other words, an identical installation concept (Profibus, ProfiNet, Ethernet/IP, EtherCAT) can be designed for different protocols by simply choosing the appropriate bus node.
Machine option management
To prevent difficulties when getting different machine modules to work together, the Cube system offers machine option management (MOM). The related hardware and software planning is carried out virtually based on a standardized full configuration. The components actually present in the real machine are activated automatically, simplifying configuration of the different parts of the machine. Optional add-ons can be configured easily with the press of a button.
The idea of streamlined machine installations poses a particular challenge when it comes to integrating safety aspects. The Cube system combines Cube67 K3 modules with the MVK Metal Safety block module as an affordable way to duplicate safety outputs.
The safety outputs of the MVK Metal Safety module will securely switch off up to 12 standard outputs, controlled by a ProfiNet/PROFIsafe control system (K3 functionality). They are divided between two safety circuits, each with three ports suitable for double connections. This multiplication of the safety outputs is a simple but effective way to reduce both costs and labor. Safety sensors are integrated directly into the installation concept with this approach, and eliminating the need for a safety relay significantly reduces the wiring workload while saving considerable space in the rack cabinet.
Another core advantage of the Cube system is its impressive range of informative diagnostic capabilities, which extend from the bus node across the entire installation down to the individual modules and channels. The extensive information saves time during commissioning and is of particular advantage during troubleshooting taking into consideration the immense costs that can result from even short downtimes.
Cube offers easily identifiable diagnostics with red LEDs that show maintenance at a glance which port is affected by an error. This diagnostic functionality can be used in detail via programming on the relevant control system.
The Cube67 Diagnostics Gateway offers an efficient, time-saving, and highly integrated method of diagnosis as it allows troubleshooting without any programming at all. It precisely evaluates all signals and diagnostic messages from the entire installation, independently of the control system. The network topology and any errors that arise are clearly visualized in a user-friendly, multilingual web interface.
The data is also available over a standard OPC UA interface for further analysis in any cloud system. This all takes place entirely independently of the control system, making it an integral aspect of the installation that need not be changed even if the control system is changed.
Key Points
- Murrelektronik's Cube system has “one cable strategy" whereby both communication and power are carried over just one system cable
- Up to 32 modules can be connected to each bus node, using four lines within an installation radius of 60m
- Diagnostic capabilities extend from the bus node across the entire installation down to the individual modules and channels
- MQ 15 connectors for wide range of applications
- MIRO Safe+ Safety Relays for all Applications
- An I/O system fit for the future
- Using data to your advantage
- Food & beverage sector benefits
- Reduced power loss
- Preventing explosions
- Diagnostics via text
- Fusion fieldbus module
- Better protection for 24VDC control circuits
- No related articles listed