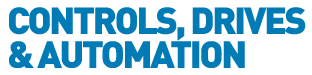
![]() |
Charlotte Stonestreet
Managing Editor |
Home> | AUTOMATION | >Monitoring | >MONITORING FOR AUTOMATION |
MONITORING FOR AUTOMATION
24 October 2012
Chris Hansford, managing director of Hansford Sensors, explains how vibration monitoring equipment protects productivity and profitability
In the past, many engineers have genuinely believed that it is cheaper to continue running worn equipment rather than invest in replacements. However, when expensive downtime costs and catastrophic failure hit the plant this theory of ‘efficiency’ is often proved dramatically wrong. This is why the use of condition monitoring has proved to be so cost-effective across industry: machines that have begun to exhibit defects are at greater risk of failure than those without defects, and are therefore more likely to generate unwelcome downtime costs; a condition monitoring system enables engineers to plan maintenance and replace defective components before problems occur.
INVESTMENT SUPPORT
With the rising costs of energy, the advance of automation technology and the steady reduction in purchasing costs has, in recent years, enabled more operators to capitalise on its benefits. As a result, more and more manufacturers are looking to condition monitoring to support their investment and the capability to monitor rotating machines with the aid of vibration monitoring remains one of the most effective preventative maintenance measures an engineer can take.
Vibration sensors offer the potential for continuous monitoring and analysis; an inexpensive option when balanced against the potential cost of downtime on an automated line.
With vibration sensors, or accelerometers, mounted in a number of key positions on mechanical equipment, and associated equipment to gather data and/or alert engineers to developing problems, machine downtime can be significantly reduced.
There are two main types of accelerometer: AC accelerometers and 4-20mA accelerometers. AC accelerometers are typically used with data collectors for monitoring the condition of more critical/complex machines, such as gearboxes and turbines, while 4- 20mA components are commonly used with PLCs to measure lower value assets, such as motors, fans and pumps.
Handheld vibration meters and data collectors are now commonplace, providing a line of defence when permanent online vibration instrumentation cannot be economically justified, or supplying a ‘second opinion’ when online systems are in place but, for example, the decision to stop the process is critical. The more critical the machinery in terms of safety and/or plant profitability, the more likely it is that a permanent online system will be employed.
MORE AND MORE MANUFACTURERS ARE LOOKING TO CONDITION MONITORING TO SUPPORT THEIR INVESTMENT
A range of sensors and monitoring techniques are now available with which to maximise machine uptime by extending operating life beyond recommended maintenance intervals and, at the opposite end of the scale, identifying rapid increases in vibration that could lead to a catastrophic failure. The efficiency of vibration sensors has driven demand in a number of ways; as well as offering enhanced efficiency and increased performance, these devices also enable operators to satisfy the ever-more robust regulations imposed regarding health and safety, which have made the use of sensors in non-safe areas a prime requisite.
RANGE OF SENSORS
A range of sensors with different capabilities are now available to suit a variety of applications. For example, Hansford Sensors has launched the HS-109 triaxial accelerometer, enabling three axes to be read simultaneously, which reduces measurement time.
Protected by a stainless steel casing, the HS-109 has an operating temperature range of -55 to 140˚C and is sealed to give an ingress protection level of IP67.
Automation has the potential to boost productivity and efficiency, not to mention product quality, but it can only do so if the plant is adequately monitored and protected. Given the current economic climate, the challenges faced by manufacturers in 2012 – especially the pressures on operating costs – look set to continue for the foreseeable future, so an effective maintenance strategy is critical.
Key Points
- Condition monitoring enables engineers to plan maintenance and replace defective components before problems occur
- There are two main types of accelerometer: AC accelerometers and 4-20mA accelerometers.
- Handheld vibration meters and data collectors provide a line of defence when permanent online vibration instrumentation cannot be economically justified