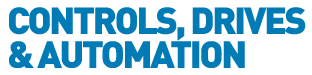
![]() |
Charlotte Stonestreet
Managing Editor |
Oil & gas sector powers ahead
12 August 2019
If not a tsunami, there was a green wave at the recent EU elections, and it is opportune to review potential developments in the oil and gas industry in the light of the environmental challenges being faced over the next two generations. Andy Pye assesses the current position
According to a new analysis by Global Witness, $4.9 trillion is the spend forecast to be spent by the oil and gas industry on exploration and extraction from new fields over the next decade. The report, Overexposed, is the first to compare the latest 1.5°C climate scenarios used by the Intergovernmental Panel on Climate Change (the Paris Agreement) with industry forecasts for production and investment. Alarmingly, it finds that any oil and gas production from fields not yet in production or development would exceed what climate scenarios indicate could be extracted and burned while still limiting warming to 1.5°C.
ExxonMobil is forecast to spend the most in new fields over the next decade, followed by Shell. Together with Chevron, Total and BP these five oil and gas majors are set to spend over $550 billion on exploring and extracting oil and gas that is not aligned with the world’s climate goals.
“There is an alarming gap between the plans of oil and gas majors and what the latest science shows is needed to avoid the most catastrophic and unpredictable climate breakdown,” said Murray Worthy, Senior Campaigner at Global Witness and author of the report. “Investors will rightly be concerned that despite industry rhetoric to the contrary, the oil and gas sector’s spending plans are so drastically incompatible with limiting climate change.”
The study finds that some climate scenarios rely on nearly as much CO2 being captured in the 21st Century as has been emitted since the Industrial Revolution. However, to date there are only two power stations in the world capturing CO2, after the commitment of $28 billion of public funds to boost development of the technology.
Malware destroys data
As the oil and gas future becomes more controversial, security issues come naturally to the fore. It is being reported that a new variant of the Shamoon malware was discovered on the network of Italian oil and gas contractor Saipem, where it destroyed files on about a tenth of the company's PCs. The vast majority of the affected systems were located in the Middle East, where Saipem does a vast majority of its business, but infections were also reported in India, Italy, and Scotland.
“The resurgence of the Shamoon wiper should remind all IT Executives and Directors of the critical importance of the basics of infosec security hygiene - such as the Australian Cyber Security Centre’s Essential 8, which starts with application whitelisting - an essential control which would have prevented this attack, automated patching, application hardening, restricting admin privileges, and multi-factor authentication," commented Andrew van der Stock, senior principal consultant at Synopsys.
"The initial entry point is of interest," adds Thomas Richards, associate principal consultant at Synopsys. "With the recent releases of breaches involving passwords, it is a possibility that an employee used the same password in multiple locations which led to the attacker’s ability to compromise Saipem. The Shamoon attack could also be predicated by a phishing campaign or other credential compromising event."
Tools to increase efficiency
All of which means that the need to reduce exploration and development costs has never been more important to the future of the oil and gas industry. This includes optimising the through-life production efficiency and the economic extension of the life of existing and ageing fields.
The abundant availability of electricity coming from renewable sources, in particular photovoltaic and wind power, is finally benefiting the environment, yet is also putting pressure on more traditional technologies. With the cost of energy and profit margins falling, they must find new ways to increase efficiency. The transition to electrification, the sustainable exploitation and profitability of shale oil fields, the maintenance of existing plants and the construction of new ones, and the growth of renewable energy present the industry with complex challenges.
Validated simulation
Within the oil and gas industry, engineering designs have traditionally been developed using empirical analysis, physical testing and experienced-based learning in the field. Simulation-based design, and particularly Computational Fluid Dynamics, is increasingly being used to explore designs and system operation digitally through detailed, accurate prediction of a wide range of physical and chemical behaviours.
Companies like TechnipFMC and OneSubsea are deploying Siemens Simcenter software in the design and operation of oil and gas products systems, including downhole tool optimization and subsea and flow assurance risk reduction.
Reda Bouamra of Schlumberger specialises in designing downhole flow control valves (FCVs). Scale deposition is a significant flow assurance challenge as it can reduce production, is costly to remediate, and can cause FCVs to jam, so the objective is to develop an FCV that was less susceptible to scale.
An integrated CFD-experimental design process has been used to design a testing programme, ensuring it was as close to real well conditions as possible. It validates CFD methods, enabling confident use of CFD to explore conditions and designs not tested. Alternative designs or scenarios can be evaluated.
PLM links complex projects
Product lifecycle management (PLM) software is another tool which enables energy producers to better manage complex projects for all involved technologies, including cloud computing, the digital twin and collaborative design, as well as the logistics, security and continuity of the operation.
“When we talk about the energy sector, we tend to think of simply generation," explains John Nixon, senior director of energy and utilities at Siemens PLM Software. “The industry is broad and includes chemical, petrochemical, oil and gas, each with its own peculiarities and critical issues. The three kinds of customers we typically collaborate with are: plant owners who produce electricity, process chemicals, refine crude oil; engineering companies that design and develop plants; and construction companies that build the structures and assemble the machinery.”
Different geographical locations also contribute to the industry’s complexity. Europe, the “mature” continent, is engaged in modernising existing facilities while the Asian giants, primarily China, will be investing massively in the next few years.
“Technology today allows us to observe everything as a whole, closely and in detail, to verify where efficiency can be improved,” says Eduard Marfa, director of Teamcenter Software Marketing for EMEA at Siemens PLM Software. “A PLM platform that connects all project information, from CAD to CAE, plant engineering to manuals and from the supplier list to the installation history, provides insight into every phase, whether that is designing, performing maintenance or retrieving information about a specific component.”
Marfa uses the concept of a digital twin, a virtual representation of a physical product or process that includes all relevant information. It is possible to perform analyses, tests and verifications, and retrieve all related data, even before a physical version is created. Replacements for failed parts can be available much sooner, by sending a part file to the site where it is manufactured using a 3D printer.
“For example, consider on-site maintenance workers,” Marfa continues. “Using a digital twin, they can look up a specific detail on a tablet and check the conditions of use (how long ago the component was installed, its useful life, its operational parameters, the manufacturer, who installed it) to decide whether to repair it, replace it, or interrupt the operation.”
Hydrate risk management
The formation of gas hydrates that block pipelines is a major concern. The threat is particularly high in offshore oil platforms, which are increasingly moving to deep water operations, as the fluid may cool to low temperatures in the flowline or in the production facilities.
Hydrates can form rapidly and can result in serious decreases in production levels, equipment damage, safety issues, and even emergency shutdown of equipment. To mitigate this risk, operators generally inject chemical inhibitors into the hydrocarbon flow to prevent their formation.
During the plant design phase, modelling and simulation software and pre-operation field test data are utilised to optimise the pipeline network design and calculate the amount of inhibitor required to prevent hydrate formation. During operations too, field operators use the simulation results to calculate the amount of inhibitor to be injected into the flow. Injection rates are regularly reviewed by field experts, but without real-time visibility into the actual state of the pipeline, operators tend to overdose the inhibitor to provide a sufficient buffer for daily operational conditions and to compensate for changes in field properties over time. This can result in excessive chemical use and increased operating expenses.
Yokogawa Electric has introduced on-demand hydrate risk management to help offshore oil platform operators maintain production levels, protect plant assets and minimise operating expenses and downtime by optimising pipeline chemical injection. The new solution integrates the Maximus and Multiflash simulation software from its subsidiary KBC, with Yokogawa’s FAST/TOOLS SCADA software. Automated chemical injection metering valve technology can also be integrated into the system.
Maximus is a purpose-built tool for compositional thermal hydraulic steady state simulations of pipeline networks, including wells, choke valves, flowlines and a wide range of processing equipment. Multiflash provides pressure-volume-temperature (PVT) modelling, used to evaluate the phase behaviour and physical and transport properties of complex mixtures and pure substances.
Withstanding extreme conditions
Unforgiving offshore conditions can be detrimental to the performance of oil facilities. Generally, large-scale machinery found on offshore rigs, such as marine riser tension systems and cranes, are specifically engineered for use in these environments, having been designed and manufactured by marine specialists. However, smaller components are often purchased from suppliers that may not specialise in marine engineering.
440 grade stainless steel is known for its resistance to damp environments. Bearings made of this material are regularly used in environments subject to washdown and exposed to water, such as food and beverage manufacturing. Despite this, 440 stainless steel actually has very poor resistance to salt water and 316 stainless steel bearings are a better option. Full ceramic bearings made from zirconia or silicon nitride can provide even higher levels of corrosion resistance and are often used fully submerged.
According to Chris Johnson of SMB Bearings, it is also worth checking that the bearings used comply with other standards, such as those relating to quality control, such as ISO 9001 and ISO14001.
Beam pumps with silent helical gears
Pentag Gears and Oilfield Equipment, a designer and sole UK manufacturer of beam pumping units in the UK, has completed the delivery of its 35th beam pump for the Wytch Farm Oil Field in Dorset.
This is the largest onshore oilfield in Western Europe, operated by Perenco and was originally founded by British Gas Corporation back in 1980. The average daily oil production of the Wytch Farm Oil Field is more than 13,000 barrels.
The Wytch Farm Oil Field comprises three separate oil reservoirs, including the Bridport and Sherwood Jurassic sandstone oil reservoirs and the Frome clay/limestone oil reservoir. Bridport lies 900m beneath the surface, the Sherwood reservoir is situated at a depth of 1,600m and the Frome reservoir, is 750m below the surface.
Pentag offers unobtrusive operation of its beam pumps with its ‘Silent Helical’ gear reducers and incorporate corrosion resistant adjustment mechanisms, suitable for all climatic conditions. They also feature a bolted construction for easy assembly and fully sealed roller or bar type bearings fitted throughout.
The beam pumps are extremely flexible and accept any type of prime mover. Their design also offers an easy and unique method of adjustment of the counterbalance weights for tuning purposes. In addition, Pentag’s beam pumps provide easy access for inspection and maintenance, as well as simple stroke adjustment.
Production Manager Andrew Larkin says: “This has been a major relationship and has involved close collaboration with engineers at Wytch Farm Oil Field. As a result, when orders for individual units have been received, we have designed, manufactured and delivered the units on time and to budget.” All units comply with API specifications.
Key Points
- Simulation-based design, particularly Computational Fluid Dynamics, is increasingly being used to explore designs and system operation
- Companies like TechnipFMC and OneSubsea are deploying Siemens Simcenter software in the design and operation of oil and gas products systems
- Product lifecycle management (PLM) software is another tool which enables energy producers to better manage complex projects
- National Engineering & Construction Recruitment Exhibition
- Collaboration key for car production
- New UK-based robotics and automation specialist
- New sensor technology
- UL develops cybersecurity standard
- UK cyber security sector worth £8.3b
- Drive for hostile environment protection
- Funding secured for Silverstone based Digital Manufacturing Centre
- New applications key to cobot market success
- Managed IoT connectivity available in AWS Marketplace
- No related articles listed