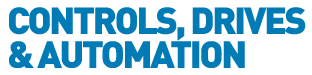
![]() |
Charlotte Stonestreet
Managing Editor |
Home> | DRIVES & MOTORS | >Variable Speed Drives | >Drive for hostile environment protection |
Drive for hostile environment protection
22 October 2016
In more demanding operating environments, it can be difficult for complex electronic assemblies to continue functioning correctly. Exposure to the elements such as moisture, salts, and corrosive chemicals such as oils or fuels take their toll, reports Andy Pye
As a result, many major industrial drives suppliers, including Rockwell Automation and Emerson Electric (Control Techniques) offer conformal coating of the electronics to give extra protection against moisture, dust and chemical ingress as well as temperature extremes. The primary purpose of a coated PCB is for the protection of the micro lead components that are vulnerable to dust and moisture build up, which can result in conductive paths.
The objective is to enhance product life, preventing or delaying electronic failure in more challenging environments; here, to address the uncoated portions of PCBs and other components, an appropriate enclosure type (IP54 or better) should be employed in addition to conformal coating.
According to Jeff Meier, low voltage drives product quality manager at Rockwell Automation, customers expect drives to operate for at least five years without failures in all locations, including harsh environments.
Typical applications for which conformal coating is beneficial include the textile, woodworking and water industries, although conformal coating is a benefit in any demanding industrial environment. Their use is becoming increasingly common in consumer and domestic applications that can be susceptible to environmentally-induced field failure, including portable devices comprising fine pitch, densely populated assemblies, such as mobile phones, through to washing machines.
Conformal coating is a thin polymeric film which ‘conforms’ to the contours of a printed circuit board to protect the board's components. Typically applied at 25-250μm, it is applied to electronic circuitry to act as protection against moisture, dust, chemicals, and temperature extremes that, if uncoated (non-protected), could result in damage or failure of the electronics to function. When electronics must withstand harsh environments and added protection is necessary, transparent conformal coating is preferred to potting.
Conformal chemistries
There are many chemistries of conformal coatings available, including acrylic, epoxy, polyurethane, silicones and polypar-xylylene (XY). A few hybrids consisting of blends of more than one type are also available.
As an example, a US-based specialist in the supply of complete electrical packages for oil rig cranes is using Control Techniques AC and DC drives as part of a landmark $500,000+ order involving the upgrade of 10 LeTourneau cranes. Although they were originally fitted with large motor-generator sets, these do not offer variable speed, meaning there is total reliance on the skill of the boom operator to lower heavy loads.
JC’s Marine Oilfield Services specialises in a variety of motor control solutions that are customised to match the needs of oil rig cranes, as well as drilling barges, supply vessels and land rigs. The company proposed the use of a Unidrive SP AC variable speed drive for the boom, and two Control Techniques Mentor MP series DC regenerative drives for the swing and hoist. Conformal coating on the PCBs, which helps impart protection in marine environments, while the large working temperature range is also advantageous.
“By changing to a Control Techniques variable speed drive for the boom we can ensure complete control over the speed and rate at which the boom moves, so that loads up to 50 tons are ‘feathered’ rather than ‘banged’ to the ground,” said John Costanza, President.
Control Techniques started by conformally coating a selection of its drive electronics, but now offers the process as standard. It operates a dedicated conformal coating line and a UV-curable coating chemistry from HumiSeal. UV curing ovens tend to be very compact and occupy far less factory floor space than the kind of equipment and machinery required to cure other types of coating material in a volume production environment. The UV40 process offers an genuine alternative to older solvent based products with none of the problems normally associated with UV curing materials: the rapid cure speed, level of processing ease and thermal cycling resistance have been previously unavailable with UV curable materials.
Key Points
- Conformal coating of the electronics gives extra protection against moisture, dust and chemical ingress as well as temperature extremes
- A thin polymeric film which ‘conforms’ to the contours of a printed circuit board to protect components, it is typically applied at 25-250μm
- There are many chemistries of conformal coatings available; acrylic, epoxy, polyurethane, silicones and polypar-xylylene (XY), and hybrids
- Soft Robotics becomes Oxipital AI
- UK tech that ‘teleports’ humans into robots in finals of global robotics competition
- Call to action to upskill on offshore wind robotics
- OPENSAFETY STANDARD UNDERPINS NESTLÉ PACKAGING AUTOMATION
- Professor Robert Richardson elected new Chair of ESPRC UK-Robotics & Autonomous Systems Network
- Researchers identify over 43,000 unprotected SCADA devices
- £213m upgrade for UK’s research infrastructure
- Software-defined OT-ready digital platform
- Made Smarter launches Guiding Principles for digitilisation
- Amazon invests €400m+ in cutting-edge robotics
- PUMPED UP PERFORMANCE
- SOFT STARTER OR VARIABLE SPEED DRIVE?
- Jeans With Less Energy
- Enhanced to Withstand Tough Environments
- Savings From Improved Torque Ratio & Efficiency
- Modular VSD
- ENERGY SAVING: AN OLD MESSAGE WITH NEW PROMISE
- Updated installation guide for power drive systems
- UK drives manufacturer seals global automation deal
- WEG motors & drives power high-efficiency air blowers