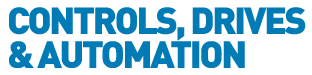
![]() |
Charlotte Stonestreet
Managing Editor |
Pneumatic robotics meets artificial intelligence
05 November 2020
WITH AN eye firmly on the cobotics sector, Festo's BionicSoftHand and BionicSoftArm 'future concepts' are pneumatically operated, enabling safe interaction directly with people
UNLIKE THE human hand, the BionicSoftHand has no bones. Its fingers consist of flexible bellows structures with air chambers. The bellows are enclosed in the fingers by a special 3D textile coat knitted from both, elastic and high-strength threads. With the help of the textile, it is possible to determine exactly where the structure expands and generates power, and where it is prevented from expanding. This makes it light, flexible, adaptable and sensitive, yet capable of exerting strong forces.
Artificial Intelligence
The learning methods of machines are comparable to those of humans: either in a positive or a negative way – they require a feedback following their actions in order to classify and learn from them. BionicSoftHand uses the method of reinforcement learning. This means that instead of imitating a specific action, the hand is merely given a goal. It uses the trial and error method, to achieve its goal. Based on received feedback, it gradually optimises its actions until the task is finally solved successfully.
Specifically, the BionicSoftHand should rotate a 12-sided “cube” so that a previously defined side points upwards at the end. The necessary movement strategy is taught in a virtual environment with the aid of a digital twin, which is created with the help of data from a depth-sensing camera via computer vision and the algorithms of artificial intelligence.
Proportional piezo valves
In order to keep the effort of tubing the BionicSoftHand as low as possible, the developers have specially designed a small, digitally controlled valve terminal, which is mounted directly on the hand. This means that the tubes for controlling the gripper fingers do not have to be pulled through the entire robot arm. Thus, the BionicSoftHand can be quickly and easily connected and operated with only one tube each for supply air and exhaust air. With the proportional piezo valves used, the movements of the fingers can be precisely controlled.
The 24 valve nozzles are connected via an airflow plate to the ten air connections of the gripper fingers and the two swivel modules. At the same time, the pressure sensors required for precise control are located on the plate. In order to be able to realise the filigree design with the complex air ducts in such a tight space, the plate is produced with 3D printing.
Shared working space
The strict separation between the manual work of the factory worker and the automated actions of the robot is being increasingly set aside; work ranges are overlapping and merging into a collaborative working space. In this way, human and machine are able to simultaneously work together on the same workpiece or component in the future – without having to be separated for safety reasons.
The BionicSoftArm is a compact further development of Festo’s BionicMotionRobot, whose range of applications has been significantly expanded. This is made possible by its modular design: It can be combined with up to seven pneumatic bellows segments and rotary drives. This guarantees maximum flexibility in terms of reach and mobility, thus enables it to work around obstacles even in the tightest of spaces if necessary. At the same time, it is completely flexible and can work safely with people. Direct human-robot collaboration is possible with the BionicSoftArm, as well as its use in classic SCARA applications, such as pick-and-place tasks.
The modular robot arm can be used for a wide variety of applications, depending on the design and mounted gripper. Thanks to its flexible kinematics, the BionicSoftArm can interact directly and safely with humans. At the same time, the kinematics make it easier for it to adapt to different tasks at various locations in production environments: the elimination of costly safety devices such as cages and light barriers shortens conversion times and thus enables flexible use – completely in accordance with adaptive and economical production.
www.festo.com
Key Points
- Re-breather function
- Accelerating technological developments
- Know your poppet from your spool: Free advice on pneumatic valve selection
- Automated biomass cultivation
- Focus on smarter automation
- INTEGRATING ELECTRIC AND PNEUMATIC CONTROLS
- Swimming robot inspired by nature
- Pneumatic safety course
- Future perfect form
- Digital twins boost machine development
- No related articles listed