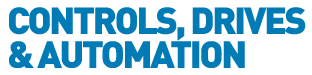
![]() |
Charlotte Stonestreet
Managing Editor |
Home> | POWER TRANSMISSION | >LinearĀ | >How to design an optimal linear motion solution |
Editor's Pick
How to design an optimal linear motion solution
12 October 2023
JOSH ROBERTS explores the range of linear motion technologies available today and guides us through the design considerations that will result in the best selection for your application.

LINEAR MOTION on machines traditionally uses pneumatic or electric drives, but recent technological advances mean there are more options available today than designers may realise. For example, point-to-point electric drives are becoming more cost-effective and can replace some movements traditionally undertaken by pneumatic cylinders. Equally, the latest pneumatic technology offers features traditionally associated with electric drives. With new servo and digital pneumatic technologies added to the mix, picking the solution that will offer the best performance, cost and energy efficiency for your application can be challenging for designers and machine-builders.
Design considerations
With so many linear motion technologies to choose from, it makes practical sense to begin with the application parameters and then decide which product option will deliver the best solution. Key design considerations include the payload (what mass is to be moved) and the force that will be required. For example, does the application require a defined pressing force, and does it vary based on the product? Designers should also define what repeatability is needed and whether multiple positions are involved, plus the motion control requirements for speed, synchronisation, or interpolated motion.
Then there are the physical and practical aspects to consider. What physical footprint is involved: is this a desktop machine or end of arm tooling on a 6-axis robot? What energy source will be used? If this is pneumatic, the supply pressure and phasing (single or three-phase) should be determined. Cost considerations also come into play: does the customer value TCO over capital expenditure, are there any energy efficiency and carbon footprint targets? Finally, is the expertise in place to service and maintain the desired technology?
Linear motion technologies
Let us turn now to the linear motion technologies available and examine their characteristics.
Pneumatics is a robust, simple to use technology with a high force density. Pneumatic devices offer best in class force output for the defined footprint and weight, together with high repeatability end-to-end positioning. Speed and position are defined with flow control and sensors. Force control is linked directly to the applied pressure. Pneumatics can be energy efficient when using best practice design and operation.
Servo pneumatics offer all the benefits of pneumatics, plus positioning capabilities. Servo pneumatic devices have a linear displacement encoder attached to the cylinder in question. The positioning commands and the encoder feedback create a closed loop control and the output is fed via a proportional directional control valve back to the actuator. The controller positions the cylinder with motion control to defined speeds and accelerations. This technology is specifically useful for applications not suitable (due to size, weight, energy source or environment) for electric drives.
Digital pneumatics offer precise control with energy and diagnostics benefits. For example, the Festo Motion Terminal (VTEM) combines fast switching and virtually silent piezo control valves with integrated sensors for closed loop control. The full flexibility of this smart terminal is accessed using the wide range of downloadable Apps (i.e. proportional control, soft-stop, pre-set travel time, leakage etc). Each valve position houses four piezo valves with boosters in a bridge format. The valve has both pressure and flow sensors for closed loop feedback of the pneumatic output at each port. This configuration enables a multitude of different functions, which are engaged by the motion apps. The function of a single valve can be changed – for example, from a directional control valve to a proportional valve – in real time.
End-to-end electric actuators are available in an array of mechanical axes designs (gantry or cantilever design with either a ball screw or tooth belt). The integrated motor is a stepper with an encoder and controller offering connections for both power supply and communications (digital IO or IO-Link). Simple to commission, these devices can be taught the desired end position and perform point to point positioning under a defined motion profile (set over the push buttons or IO link). Mid-positions are also possible with IO-Link control.
Electric drives combine advanced motion control with high dynamic motion. Common servo controllers range from 24 V DC power supply to 3 phase 480 V power supply. Based on the motor type selected for the application (stepper, BLDC, servo), designers can deploy an array of different feedback encoder types. Position, speed, and force can be controlled from the PLC via the servo controller. Multiple drives can be combined via motion controllers for complex handling solutions. Enhanced motion control can also be achieved, including synchronisation, flying saw and interpolated motion. Functions such as DC link can be enabled for improved energy efficiency.
A summary of the benefits and applications of each linear motion technology is given in Figure 1.
Figure 1: Summary of the benefits and applications of different linear motion technologies
TCO and sustainability
Total cost of ownership is becoming increasingly important and making the correct sustainable choice of linear motion technology can be time-consuming and complex. Festo offers a software tool to simplify the decision-making process. Aptly named ‘CO2 & TCO Guide’, this tool helps designers to compare electric and pneumatic drives from Festo’s product portfolio and provides a clear comparison of the energy consumption, CO2 emissions, initial purchasing costs (based on your company’s conditions) and the total cost of ownership. Users simply enter the key application criteria, and the tool provides a graphical, illustrated cost calculation over periods of up to 10 years.
More resources
Keeping pace with advances in linear motion technology will help designers to make the right choices for their application, based on the relevant criteria. Festo supports all five of the linear motion technologies discussed in this article, which means we can give technology neutral advice and offer online selection tools that support our customers in identifying the best solution for their application.
Further support, including a more in-depth explanation of the linear motion technologies available and how to relate them to a real machine design, is available in the 'on-demand' webinar at the website below.
Josh Roberts is product manager at Festo GB
www.festo.co.uk/optimaldriveswebinar
Key Points
- When designing, begin with the application parameters and then decide which product option will deliver the best solution
- Pneumatic devices offer best in class force output for footprint and weight, with high repeatability end-to-end positioning
- With total cost of ownership becoming increasingly important, Festo offers a software tool to simplify decision making
- Full Servo Motion Advantages At A Fraction Of The Cost
- First UK Cyber Factory training facility
- Industry 4.0: Revolution or evolution?
- Easy swap from one PLC manufacturer to another
- Development at pace!
- Festo celebrates centenary
- Multi-protcol keeps things simple
- Electrical positioning systems made easy
- INTEGRATING ELECTRIC AND PNEUMATIC CONTROLS
- Festo and QM Systems collaborate on automated mass testing system
- Roba-linearstop Gets Dynamic Brake Approval
- YOUR CARRIAGE AWAITS
- FT Series - Linear Actuators
- Record contract
- Moore International key distributor for Schneeberger
- Art comes alive with linear rail
- Linear positioner for fluid mechanics
- High force operation
- Limitless size & variation
- For processing & packaging