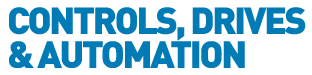
![]() |
Charlotte Stonestreet
Managing Editor |
Smarter workers
25 February 2016
The full potential of Industry 4.0 will only ever be realised if factory-floor staff believe in the concept and are trained to deliver it, asserts Neil Lewin, consultant - training and development at Festo
Industry 4.0 has gone from buzz phrase to widespread understanding and acceptance in an astonishingly short space of time. First promoted by the German federal government and used in 2011 at the Hannover Fair to describe the conceptual workings of forward-thinking German companies, the term is now commonly used to outline the many strands of increased digitisation that will lead to smarter factories and streamlined production. Indeed, many advocates suggest that Industry 4.0 is so important that it will usher in the ‘fourth industrial revolution’.
It is certainly a topic that is exciting manufacturing companies across the globe. Production environments with components that can communicate with each-other and control and regulate themselves bring the potential of much higher levels of customisation. While the most cutting-edge car plants can already build a multitude of models and options on the same line, Industry 4.0 will bring the same flexible possibilities to mass produced consumer items such as footwear and domestic appliances. And with mass customisation comes increased efficiencies and bigger returns.
But the value of Industry 4.0 will only be realised if it is fully embraced by workers on the shopfloor. The human operator is and will remain the key element of modern production, but can expect to be assigned more and more new tasks. Employees on production lines will be required to perform complex decision making, enact swift troubleshooting, and oversee effective preventative maintenance strategies. If Industry 4.0 is to deliver smarter factories, there will be a requirement for an army of knowledgeable staff.
German industrial control and automation company Festo has been quick to identify the training opportunities that this will bring. The role of the employee within the modern production environment will be transferred from that of machinery operator to fast-thinking problem-solver, requiring new levels of training and knowledge. The topic of education will become a key success factor in smarter industrial environments. For a workforce to fully embrace Industry 4.0, and to perform new and different tasks such as working alongside collaborative robots, they have to understand what it means and know how to make the best use of it.
The role of people in the success of the digitalisation of manufacturing is absolutely critical. Industry 4.0 creates an opportunity for traditional, higher labour cost areas to remain globally competitive and able to meet the ‘customisation’ demand. That is an exciting possibility for countries like Germany and the UK which may struggle to compete with emerging nations on cost alone.
Change management
However, in tandem with technical competency, Industry 4.0 will also require a strong focus on change management. One of the biggest obstacles to its adoption will be employee reaction and acceptance. If workers are concerned that Industry 4.0 will eliminate their jobs, they are bound to be resistant to it. Huge efforts need to be made to ensure that staff understand that Industry 4.0 is more of an opportunity than a threat.
That means managers also need to sharpen their skills. Accepting change isn’t easy for all employees, so leadership skills in change management will be critical. The effective handling of change management will ultimately differentiate between the winners and the losers in the Industry 4.0 revolution.
Festo’s development in course material around Industry 4.0 has also been underpinned by investment in ‘equipment’, with a ‘cyber physical factory’ that has been developed by its Didactic division. An early example is embedded in the company’s new production facility in Stuttgart where it is being used for the qualification of underlying principles across areas such as assembly lines, fabrication, production planning and quality control, and lean methodologies.
The cyber physical factory is effectively a research and learning centre, pulling together mechatronics and network formation. It’s a place where the development of networks can be carried out, focussing on areas such as network communication, energy management, condition monitoring and process optimisation. It can be used to test and develop cooperation between intelligent components, together with their interconnections, under real conditions. It’s where Industry 4.0 starts to come to life. Several UK institutes and academic establishments who want to be in the vanguard of technology are actively considering the use of the Cyber Physical factory.
It’s clear, then, that Industry 4.0 isn’t restricted to the adoption of new technologies. It will also require a fundamental change in the way that managers and shop-floor employees carry out their roles within production environments. And Festo is at the forefront of putting the necessary skills and competencies in place.
Key Points
- Industry 4.0 needs to be fully embraced by workers on the shopfloor who will required to perform complex decision making
- There will be opportunity for traditional, higher labour cost areas to remain globally competitive and able to meet the ‘customisation’ demand
- Industry 4.0 requires a strong focus on change management; staff must understand that Industry 4.0 is more of an opportunity than a threa
- Improving predictive maintenance with artificial intelligence
- Festo debuts first pneumatic cobot
- Tips for I4.0 implementation
- Handling solutions in 20 minutes
- How to design an optimal linear motion solution
- Pneumatic safety course
- Multi-protcol keeps things simple
- Simplicity & efficiency with selection & assembly
- E-vehicle revolution powers on
- Accelerating technological developments
- No related articles listed