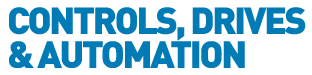
![]() |
Charlotte Stonestreet
Managing Editor |
Home> | POWER TRANSMISSION | >Gears | >Precision racks have twice the holes |
Precision racks have twice the holes
25 June 2024
DID YOU know that gear racks were originally used to place objects at different heights? For example, they were used in kitchens to perfectly position pots over fireplaces. As industrialisation progressed, the gear rack became far more important as a machine element and found its way into mechanical engineering.

Today, rack and pinion drives convert the rotary movements of gear units or motors into linear movements, or vice versa. The drive itself consists of a gear rack and its counterpart, the pinion. When the pinion is turned, the gear rack moves along its longitudinal axis, resulting in linear motion.
The challenge: improving positioning performance
Gear racks must not move out of place when forces are applied by the pinions. The holding force of the screw fastenings counteracts this. In addition, gear racks are usually mounted with dowel pins at both ends of the racks and this process requires considerable effort. To ensure that the position is exactly right, the bores for the dowel pins must be made and then reworked with a reamer directly on the machine in the bolted-on state. This is extremely demanding, time-consuming work, and creates swarf.
The solution: double bores
Stober's new precision gear racks with twice the bore holes eliminate the need for time-consuming doweling. The contact pressure on the machine body is doubled: Instead of every 125mm as is standard, gear racks are fastened again after just 62.5mm Although time-consuming doweling is not required, it remains an option thanks to the existing holes.
Stober's precision gear racks are available in various lengths and modules, for the highest demands on smooth operation and positioning accuracy:
- Module: 2 – 6
- Max. feed force: 12.6 – 83.1kN
- Helical, hardened and ground
- Gearing quality 6 in accordance with DIN 3962-1
- Length: 500mm, 1000mm.
Consistent system concept
According to Stober, its innovative concept for rack and pinion drives, combined with planetary or helical bevel gear units and directly mounted servo motors, offers a perfectly coordinated system that can be flexibly adapted to a wide range of requirements in terms of load capacity and precision. It is ideal for applications in machine tools or automation and robotics and will provide extra safety against possible shifting.
- New Winding Technology
- Shhh...planetary gears at work
- Best supplier award for Stober
- Unwind, wind and rewind with precision
- Motor removal on the vertical axis
- Connect motors & drive controllers up to 100m
- Right-angle servo gearbox
- Online drive solution configurator
- Advanced drive module plays it safe
- Enhanced predictive maintenance