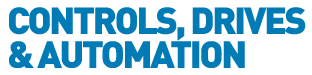
![]() |
Charlotte Stonestreet
Managing Editor |
Home> | AUTOMATION | >Condition Monitoring | >Enhanced predictive maintenance |
Home> | DRIVES & MOTORS | >Electric Motors | >Enhanced predictive maintenance |
Home> | DRIVES & MOTORS | >Geared Motors | >Enhanced predictive maintenance |
Enhanced predictive maintenance
11 December 2024
HIGHER EFFICIENCY and fewer breakdowns are STOBER’s objectives as the company continues to enhance its predictive maintenance capability.

The drive specialist has defined several functional stages of development: the drive train is continuously monitored, and maintenance recommendations are created based on an analysis of the relevant process and machine data. The options here range from analytical calculation models to AI and deep learning. STOBER has embraced an integrated solution strategy. No external sensors or accessories are required, and the solution is totally accessible for a wide range of controllers.
It was Tim Lang, head of applications at STOBER, and his team that commenced this latest development by asking: “How can we use predictive maintenance to make the transition from pure condition monitoring to real condition-based servicing for drive trains?”
Highlights Lang: “We know that predictability is becoming increasingly important for users who want to achieve higher availability, lower maintenance costs and longer life cycles. They have to answer questions such as: “How likely is it that the geared motor will fail soon?” or “When is the ideal time to service or replace it?”. As such, we began working on predictive maintenance several years ago to ensure we were in a position to be able to make these predictions and others.
“We are constantly evolving and, for this focal area, we have drawn up a three-stage plan. We are currently tackling step two."
First stage: Model-based analysis
In the first stage, users received a predictive maintenance solution that monitors the geared motor of a drive system. Its life performance is calculated using an analytical model and then output in the drive controller software via a life performance indicator, which is a value between 0 and 100 percent. At 90 percent, the software outputs a recommendation to replace the geared motor and provides it to a controller in the form of a readable parameter. This efficient solution for predictive maintenance requires neither external sensors nor additional wiring.
Second stage: Active measurement
“In the second step, we are incorporating active measurement into this calculation model,” explains Lang. To do so, STOBER is integrating an acceleration sensor into its system consisting of a gear unit, motor, cable and drive controller. External peripheral devices, such as additional power or voltage sources, are not required. This makes it possible to measure bearing seats, toothing and other drive components efficiently.
“Frequency analyses enable us to draw conclusions about impending damage based on a spectrum - right now, we are still in the implementation phase.” STOBER is working closely with HEIDENHAIN to develop a geared motor with an integrated acceleration sensor.
The goal in sight: A smart drive train
STOBER will continue to build on the first two steps and improve predictive maintenance with deep learning and artificial intelligence (AI). The aim is a smart drive train that can both recognize its own condition and provide important information from the field in real time.
“Since summer 2024, we have been able to implement useful enhancements for our release. Among other improvements, we have refined the analytical model and expanded the database to include over 80,000 gear unit and motor variations. In addition, special customer-specific versions can also be evaluated now. Users benefit from easier operation and improved visualization,” says Lang.
STOBER will also provide function blocks and sample programs in the future. This will allow the data obtained, and in particular the load matrix, to be read out via EtherCAT or PROFINET. The load matrix is a solid database for recording real-world load situations. The cumulative load condition of the drive system is continuously documented over the entire operating time.
Concludes Lang: “At the end of the year, we will also be able to offer our customers an analysis tool that can evaluate and compare several load matrices and create standardised reports. We now have condition-based servicing that offers us a very broad field of application. It can detect design and assembly influences via a machine type, for instance, or carry out long-term analyses.”
- Stober collaborates in drive to make mobile ventilators
- Energy-saving modular drive
- Motor removal on the vertical axis
- Automated drive for heavyweight loading
- Permanent magnet servo motors provide energy efficient solution
- RACK-AND-PINION REDESIGN CUTS GEAR SIZES
- Drive Design Can Be Based On Torque Required
- High power supply for multi-axis drive systems
- Stäubli specifies Stober axes to expand robot range
- Compact drives for depowdering system