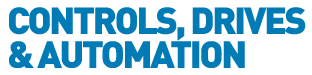
![]() |
Charlotte Stonestreet
Managing Editor |
Home> | AUTOMATION | >Robots | >Precision drilling and machining |
Editor's Pick
Precision drilling and machining
30 August 2022
DEMONSTRATING THE importance of precise working and optimised productivity in the aerospace engineering sector, automation specialist FANUC has used the Farnborough International Airshow (FIA2022) to unveil the latest version of its ROBODRILL machining technology – the a-DiB Plus series – for the first time in the UK.

“The ROBODRILL a-DiB Plus platform and its benefits can be largely defined by the epithet ‘high’, starting with its high reliability and high performance,” says Stefan Raff, FANUC’s head of sales ROBODRILL, ROBOCUT, ROBONANO Europe. “Add to this its high productivity, speed and power and the picture is almost complete.”
At the same time, the enclosed cell is extremely compact. It is available in versions suitable for an X-axis stroke of up to 300mm, 500mm and 700mm.
Productivity improvements are clear in the deployment of FANUC’s latest CNC system, which is at heart of the a-DiB Plus. One example is the Smart Overlap function, which allows machine adjustments to occur in parallel – for instance, a tool change and table repositioning. Such capabilities can lead to vastly reduced downtime and significant efficiency benefits over an entire shift. Similarly, tapping cycle times can be reduced by maximising spindle motor outputs without losing accuracy.
Servo control is optimised for an enhanced level of overall machining accuracy, and for options including smooth tolerance control and high-precision programme command. The system also offers a variety of high-speed and high-power spindles.
Smart adjustment
The stable machining features of the a-DiB Plus system can help to reduce wastage and maximise yield from parts and workpieces. Options for estimating thermal displacement include a touch probe and AI-based technology. These allow adjustments to be automatically factored in, based on the status of spindle and feed axes. They can compensate for temperature-driven changes, resulting from the transition between day and night, for instance, or between seasons. At the same time, the unit’s impressive levels of reliability are supported by its preventive maintenance function.
“Another ‘high’ that this system allows customers to experience is ‘high expandability’,” Raff adds. “The external interface function means that peripheral devices can be linked and controlled from the unit, without needing to integrate control panel hardware.”
A plant’s various ROBODRILL machining centres can be networked via Ethernet connections and linked to a management-level client PC, for instance. This can be used as part of an operation condition monitoring system, to collect and compare data – such as tool life data – from different units.
FANUC continues to carry out its own exhaustive in-house monitoring and testing with numerous ROBODRILL cells operating under different conditions, handling both aluminium and steel parts.
Meanwhile, for customers, the benefits of the system’s flexibility can be maximised thanks to the well-designed user interface. The 10.4-inch colour LCD human-machine interface (HMI) has the option of a touch-screen display. As well as production parameters, it allows the setup of optional devices and networks. CNC programmes and auxiliary robotics can be controlled from the same HMI.
Management screens, including production counters, machining mode and data on thermal displacement compensation, can be accessed in the same location, and programmes are easy to check through machining simulations.
- FANUC lands global robot deal with Volvo Cars
- Heavy lifting cobot
- New high-payload industrial robots
- Wake-up call for UK manufacturing
- Plug & weld robot cell
- Robotic pot swap
- Mollart unveils FANUC as exclusive CNC partner for the next generation MicroDrill range
- Recycleye wins FANUC award for innovation
- Commitment needed to change UK culture around automation
- Software Options Build Up Basic Robot Profile
- Balls to Gravity
- ROBOTS GIVE FASTER CELL TOOL CHANGE TIMES
- ROBOT FOR DELICATE ASSEMBLY
- NUMBER OF ROBOTS IN UK ON THE RISE
- The future is bright - The future is automation!
- High Demand For Grant
- More Capacity, Less Space
- FREEBIRD - THE THIRD DIMENSION
- PRECISION ROBOT CELL FOR THE PHARMACEUTICAL INDUSTRY
- ROBOT SALES REACH ALL TIME HIGH