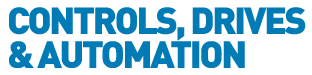
![]() |
Charlotte Stonestreet
Managing Editor |
SEVEN DRIVES FOR SEVEN SECTORS
31 October 2012
Research and design programmes arising from an extensive programme of market research have resulted in UniDrive M
A family of seven drives, UniDrive M has been designed to meet the requirements of a specific area of the manufacturing market, and able to address motor control applications from 0.25kW to 1.2 MW.
UniDrive M will be making its first appearance at SPS Nuremburg in November 2012. 30 patent applications have been submitted to protect the technical advances developed for Unidrive M
To create the Unidrive M family, Control Techniques has conducted the most comprehensive programme of market research in the company's history. Basing the design of its next generation of drives on market research conducted with users in the manufacturing sector, Control Techniques has been able to target their needs explicitly.
The initial programme of qualitative research consisted of a series of in-depth interviews with OEMs and other end users in the manufacturing market. This was followed up by a comprehensive programme of quantitative research which greatly expanded upon the findings of the interviews, ensuring that Control Techniques understood exactly which drive features each specific area of the manufacturing market requires.
The quantitative research consisted of web-based surveys which recreate the buying decision.
"Our research has enabled us to understand the manufacturing market more thoroughly than at any previous point, and the information we received was vital in deciding which customers to target with which products. We found that customers within the manufacturing sector are clustered into seven main groups, each with highly specific needs. As a result of our research, we decided to develop a range of seven drives - one for each main customer group," said Jay Wirts, Vice President of Strategic Marketing at Control Techniques.
Unidrive M offers seven functionfocused drive models, all with motor performance and an individual feature set to best match a specific application and system connectivity needs. "Once Unidrive M is released, Control Techniques will be launching additional ranges of drives that will be targeted at each of our other main market sectors," says Enrique Miñarro Viseras, President of Control Techniques. The Unidrive M family is, however, designed to extend the field service life of previous generations of products and provides the easiest possible upgrade for OEM machine designs that currently use Control Techniques’ Commander SK and Unidrive SP drives.
Standard Ethernet is used for communication across drives, I/O, HMIs, PLCs and other industrial devices. On-board real-time Ethernet (using IEEE 1588 V2) provides machine control with fast and flexible communications, achieving synchronisation rates across the network of below 1μs, update rates as low as 250μs and virtually unlimited node count.
Standard Ethernet also allows Control Techniques’ protocols to work alongside others - using onboard functions and click-in System Integration (SI) option modules, Unidrive M offers connectivity to all common Fieldbus communications such as Profibus, DeviceNet, CANopen and EtherCAT. The SI modules are certified by third parties to ensure full compliance with standards and trouble-free configuration and operation.
CONTROL PROTOCOL
Control Techniques’ new Real Time Machine Control Protocol uses standard Ethernet TCP/IP and UDP to provide a highly efficient and compact message structure that frees up Ethernet network bandwidth and minimises network loading. This allows Unidrive M models to talk directly to each other instead of using the traditional route of routing all communications through a machine controller. Each Ethernetenabled drive incorporates a dual port Ethernet switch with standard RJ45 connectors, greatly simplifying networking machines.
EACH ETHERNET ENABLED DRIVE INCORPORATES A DUAL PORT ETHERNET SWITCH WITH STANDARD RJ45 CONNECTORS, GREATLY SIMPLIFYING NETWORKING MACHINES
In fact, certain applications, such as electronic line shafts, can be set up without having to write any programming code at all. In these instances, the drives will start communicating with one another automatically, synchronising their control loops so that they can operate in seamless coordination.
Control Techniques’ new top range Unidrive, the M800, integrates a new breed of high performance MCi200 machine controller within the drive - a second microprocessor - designed to provide comprehensive machine control. The drives utilise open and industry standard technologies. They are configured using the CODESYS programming environment in accordance with IEC 61131-3, the international standard that specifies the five programming languages optimised for use in automation equipment.
Over recent years IEC 61131-3 has become widely used and is supported by the majority of automation vendors providing access to an enormous talent pool of engineers.
M800 is ideal for applications requiring machine axis control and high speed interfacing with other control devices such as PLCs, I/O and HMIs, such as gearing and ratio control, winding (coilers), web handling, and metal cutting.
The M810 variant takes this a stage further with the addition of a dual port switched Ethernet interface directly on the CODESYS microprocessor board. This greatly extends the machinery control performance through increasing the data throughput capability, it also enables simultaneous connectivity to two separate Ethernet networks.
Another area of innovation in the development of Unidrive M has been the PC tools - Unidrive M Connect and Machine Control Studio. To use the new tools, a user does not need to know about their specific drives or parameter menus, and can easily undertake drive and application set up, system and drive monitoring, optimisation of motor performance or write advanced system programmes.
OPTIMISE DRIVE TUNING
Unidrive M Connect is Control Techniques’ new drive configuration and monitoring software, designed to make it easy to access the full feature sets of the drive. It allows users to optimise drive tuning, back up the configuration set and troubleshoot more quickly.
The Machine Control Studio software provides a full-function automation development environment that uses open industry standard IEC 61131-3 programming languages and is powered by CODESYS to fully meet Manufacturing Automation application requirements. Unidrive M Connect and Machine Control Studio both use the same communications components, allowing them to run simultaneously using numerous communication protocols.
"Commissioning and maintenance tasks have been greatly simplified through a user interface that prioritises the most commonly performed tasks, simplifying the experience for all users, whilst advanced users will benefit from the fact that dynamic drive logic diagrams and enhanced searchable listings are present.
Meanwhile, the drive and motor performance can be optimised with minimal specialised drive knowledge," says Tom Alexander, Vice President of Technology at Control Techniques.
For the advanced motor control needed by the most demanding machine applications, the new Unidrive M family has more than double the bandwidth of the control loops. Proprietary motor control algorithms, combined with the advanced microprocessor technology, ensure that the Unidrive M range offers high stability and performance for all industrial motor types. This enables users to maximise machine throughput in every application and with every motor, from standard AC induction motors to high dynamic linear motors, from energy-saving permanent magnet motors to high performance servo motors.
Machine safety features enhance machine throughput while protecting people and assets, helping to meet SIL3 (Safety Integrity Level 3). Different Unidrive M models offer alternative levels of integrated safety functions to suit various manufacturing needs, reducing external components and machine costs.
- No related articles listed