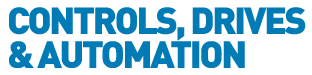
![]() |
Charlotte Stonestreet
Managing Editor |
Home> | AUTOMATION | >Condition Monitoring | >Open a window to compressed air energy savings |
Home> | POWER TRANSMISSION | >Pneumatics & Hydraulics | >Open a window to compressed air energy savings |
Home> | AUTOMATION | >Sensors | >Open a window to compressed air energy savings |
Open a window to compressed air energy savings
29 February 2024
Everybody is talking about digitalisation – and sometimes it is the simplest applications that demonstrate its power to transform. By opening a window to locate and calculate compressed air energy wastage in real time, production teams are saving up to 30% of their electricity costs, reports Charlie Walker

AS THE so-called 'fourth utility' of manufacturing, compressed air systems are one of the most expensive resources in production and logistics, accounting for for 10% of energy use in a typical manufacturing operation, rising to 30% in heavy use industries such as food and beverage, automotive, plastic products and pharmaceuticals.
Yet despite offering possibly the greatest opportunity for belt tightening, opportunities for savings are all too easily overlooked. With anything up to a third of compressed air being wasted in a typical operation, the cost-savings available can add up to big number.
Hit and miss
Yet, this apparently 'low hanging fruit' is simply often overlooked. Tracking down and fixing leaks can be a hit and miss affair; for some, only a matter of 'listen, look and detect'. When the pressure drops, it’s tempting to turn up the power – increasing the load on the compressor, and probably pushing more waste out from the weakest points.
But when fluctuations in pressure compromise production efficiency, there will be more unplanned maintenance, more unexpected machine downtime, and the compressor’s service life will be shorter. Product quality and reject rates could suffer if air is not delivered at a constant, optimum pressure.
Even with a modern energy management system in place, a maintenance team may only survey the plant every three or six months. External companies may be brought in to conduct periodic spot check audits.
Regular maintenance inspections are also costly and labour intensive and the data is reliable for only for one moment in time. If you walk around the factory today and fix all your leaks, tomorrow there might be three more you will not have found.
Very little can be gleaned from it about any trends or patterns. Do some machines use more compressed air than others, when, and why? How can compressed air energy reduction best be targeted across entire processes and production halls to maximise results?
‘Bolt-on’ transparency
By feeding the data from accurate sensing instruments into new cloud-based monitoring systems, sensor manufacturers like SICK are introducing digital services that are easy to ‘bolt on’ to existing production process with minimal set-up and no programming. The results can be remarkably revealing, and SICK customers have been surprised by the discoveries they can make.
One successful adopter of is a major European beverage manufacturer, whose production and filling lines consume one million cubic meters of energy-intensive compressed air every year. An annual saving of almost €60,000 was identified within a just a few days of the system going live. Further savings are being uncovered on a regular basis as new leaks occur.
Energy savings success
The turnkey digital solution was developed by SICK specifically for continuous compressed air energy management. The SICK FTMg multifunctional flow sensor enables the measurement of live values for compressed air energy in kWh. Using this data, collected from SICK FTMg flow meters strategically positioned close to machines or cells, a wealth of both real-time and historic data about compressed air usage, including energy consumption, is available.
At the beverage plant, about 50 of SICK’s FTMG multifunctional flow sensors are positioned across several production lines. The sensor data is analysed with intelligent algorithms to evaluate how compressed air is being consumed during normal operations, as well as during downtimes. The system can begin to pinpoint the source of potential leaks.
Data from the FTMg flow meter is made transparent through graphics presented in the SICK FTMg Monitoring App. With the click of a button, users can start to visualise the continuous compressed air data in a way that is easy to use and interpret. As well as values for pressure, temperature, flow velocity, mass flow rate and volumetric flow rate in real time, the system provides totals for energy use, volume and mass over a pre-defined period.
The user-friendly dashboard makes it easy to interpret data to detect leaks or overconsumption and to look for changes and trends. Email alerts can be set up for maintenance reminders or to give pre-defined warnings with job recommendations, for example, when data strays beyond pre-defined limits. Users can drill down to identify costs, for example for individual production centres or by shift.
Unexpected insights
We are already seeing how production planners, energy managers and maintenance engineers are gaining unexpected insights. As a result, they have been able, for example, to make start-up and shutdown management of processes and machines more efficient, improve compressor control, and manage peak loads.
By tracking consumption over time, losses are easier to spot and correct. For example, energy waste is clear if the compressed air usage graph does not baseline close to zero at weekends. Is there a surge in power usage on a Monday morning when machines are turned on? Then, perhaps, a more efficient power-up sequence could be adopted to prevent overloading the compressor.
The system makes it possible to monitor energy usage close to the machine cells where the compressed air is being used. Armed with additional information, production teams can pose specific questions: How much air is cell number 1 using, compared to cell number 2? If cell no 3 uses a lot more compressed air energy, then keep it offline as long as possible. How much compressed air energy is needed to produce one type of component compared to another?
Up to eight FTMG flow meters can be configured via each SICK Smart Services Gateway, which collects data, aggregates and encrypts it before sending it securely via the customer’s own IT infrastructure through a firewall to the SICK cloud. Alternatively, it is possible to by-pass the IT infrastructure by using mobile communications over 3G or 4G. Individuals then have access through a personal SICK ID from any device with a web browser.
SICK also offers alternatives for customers who do not require the FTMg Monitoring App. For customers wishing to integrate SICK FTMg flow meters into their own IT systems, one or more devices can be used with an IIoT gateway, such as the TDC-E from SICK, for data pre-processing and integration into customer-specific MES, cloud or energy management systems.
Measurable payback
Wasted compressed air adds up to a huge energy costs and carbon emissions that are easily fixed. Understanding the importance of compressed air energy efficiency as part of total cost of ownership demonstrates the benefits of investment in efficient in-line, real time instrumentation – especially when combined with the data transparency that is unlocked by new digital services. The payback could be instantly measurable.
Charlie Walker is digital services consultant at SICK UK
Key Points
- With anything up to a third of compressed air being wasted in a typical operation, potential cost-savings can add up to big number
- Feeding data from sensing instruments into cloud-based monitoring systems, sensor manufacturers are introducing digital services
- The SICK FTMg multifunctional flow sensor enables the measurement of live values for compressed air energy in kWh
- TDC gateway system
- Get started with IO-Link on the PLC
- High consistency & linearity
- Brings live sensor data to the Cloud
- High-speed sensing
- Is it time to rethink 3D vision?
- Sensor bolts-on for condition monitoring
- Ten second sensor change
- How safe is your cobot application?
- High-Integrity Series Connection