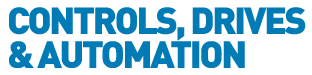
![]() |
Charlotte Stonestreet
Managing Editor |
Home> | MACHINE BUILDING & ENGINEERING | >Machinery Safety | >Safeguarding frequent access danger zones |
Safeguarding frequent access danger zones
01 November 2021
Safety, user friendliness and productivity should all be reconciled when it comes to area guarding of plant and machinery. Dave Scot looks at the latest solutions
WHEN PEOPLE require frequent access to the danger zone or when materials need to be fed in or out, optical safeguards are suitable for safeguarding protective devices. These include radar systems as well as optoelectronic sensors such as light curtains and laser scanners. Which sensor type is used and when depends largely on the application situation.
The following rule of thumb applies: scanners or light curtains are always a very good choice when it’s possible to work well with optical methods and there is a clean machine environment. In contrast, not only is the radar sensor well able to tolerate rugged environments contaminated with dirt and dust, but it is also the ideal protective measure in environments with extreme temperature differences and weather conditions. The use of radar technology should also be considered when it is a question not just of monitoring areas but also of detecting objects in a 3-dimensional space. Light curtains/light barriers and scanners safeguard two-dimensional areas such as access points and floor areas. They can detect either static (light curtain) or dynamic obstacles (AGV). Monitoring of dynamic obstacles can also cover static application areas – the key phrase: access control or protection against encroachment behind. The radar sensor can do that too. That again illustrates that there are several criteria to apply when deciding which protection technology can or should be used on a case by case basis.
If an intervention or access point to an application is to be monitored safely, with high resolution and short reaction times, then light curtains are the right choice. However, if entire areas with various protected fields are to be safeguarded, then scanner technology is suitable in this case, as it can also provide precise edge definition. Essentially, scanners record any type of object. In contrast, the radar sensor detects objects specifically by material – water, metal and movements, to which it reacts. So it is always beneficial when the environment requires a system to be highly robust and insensitive to environmental influences, whether that be dust, dirt, rain or similar rugged environments.
Safety light curtains
Safety light curtains are mainly used when the implemented safety solutions need to be barrier-free. This is the case when processes do not run one hundred per cent automatically, i.e. there are open access or intervention points on the machine, where operators need to intervene in the process, as is the case when feeding or removing products or parts. Particular care is needed for the safety-related assessment of these processes. In the case of light curtains, an invisible infrared protected field protects against access or entry into hazardous machine areas: if a light beam is broken it will immediately trigger a safe shutdown command. Depending on the requirement, light curtains provide finger, hand and body protection in accordance with EN/IEC 61496-1/-2 "Safety of machinery – Electrosensitive protective equipment". These have short reaction times measured in milliseconds, meaning that the safety distance can be minimised and the precious space can be used for production tasks.
Advanced functions such as blanking, as well as muting or cascading, have been established to maintain detection mode while still allowing material to pass through the light curtain. Two types of blanking are available, depending on the requirement: either certain light curtain beams will be blanked because an object – a conveyor for example – permanently protrudes into the protection zone; this is called fixed blanking. Or the object protruding into the protection zone moves, such as a cable; in this case floating blanking is used. Applications that protect against encroachment into and behind the protected area can also be implemented using light curtains. This is possible thanks to a light curtains’ cascading function, in which protected fields without dead zones can be connected together. In contrast, muting means that the light curtain beams are suspended temporarily during operation to allow material to pass through the detection zone. In other words, the muting sensors detect the material and the light barrier is automatically and temporarily interrupted in its machine cycle, under safety conditions.
Another requirement that a light curtain can fulfil well is shock resistance. The current version of the standard EN/IEC 61496 defines two shock classes: class 3M4 defines acceleration values up to 15 g and class 3M7 accelerations up to 25 g. Shock resistance functionality is an absolute must where rugged environments are concerned, in which vibration or collisions prevail. This is the only way to guarantee higher plant availability.
While safety laser scanners and radar sensors tend to safeguard larger areas or zones, light curtains can also be used in a confined space. With light curtains, the specifications for physical positioning can be implemented freely and flexibly in accordance with the implementation requirements, without adversely affecting their functionality: coding is one solution here, so that even several light curtain pairs installed in close proximity will not interfere with each other. They are simply coded differently.
Safety laser scanners
Safety laser scanners are suitable for area guarding of static or mobile danger zones, as access control or for applications that protect against encroachment behind the protected area.
However, as with the light curtains, under certain pre-defined conditions, part of the plant or the goods themselves can need to be moved within the protected area, without causing the machine to stop. This requires a dynamic muting function, or if necessary, also a partial muting function. Partial dynamic muting guarantees greater availability on plants, as does beam coding, which ensures that two scanners do not interfere with each other. For example, dynamic muting is always an enormous benefit to users when feeding in material of various sizes.
In conclusion, laser scanners are a good choice when a high edge definition is required, when the protected field needs to be defined precisely and there is a “clean” machine environment: radar systems are used where classic optical sensors reach their limits due to environmental conditions such as reflection, dust, water, dirt or sparks.
Radar technology
Radar technologies achieve a somewhat lower resolution and edge definition on the border of the protected field and, with a response time of approx. 100ms, react somewhat slower than the laser scanner; however they can penetrate all materials except metal and water. Environmental influences that can cause measurement errors on scanners are no problem for radar systems. That's because radar systems operate with reflected electromagnetic energy in the two-digit gigahertz range and react to movements. As with the light curtains, here too integrated muting for the whole system or for individual sensors enables the radar sensor to be used in material flow applications, with benefits for the plant's output.
The radar sensor has two safety-related functions in its sights: area guarding and protection against encroachment behind the protected area. The former guarantees that the machine is brought to a safe state when the danger zone is accessed; protection against encroachment behind the protected area prevents the machine restarting unintentionally when there is still somebody in the danger zone. Complex applications, even in rugged environments, present no challenge to such radar systems; industrial plants work efficiently despite the environment, because their availability is reliable. So typical application areas can also be found in heavy industry, for example, where dust, swarf, welding sparks or bright light prevail. As volume is monitored, radar technology can also be of benefit in the woodworking industry, on paint lines, in cold stores or in foundries. On outdoor applications, the radar sensor safeguards cranes or bulk cargo ports and storage facilities, even in the event of fog, snow and moderately heavy rain.
Dave Scot is technical support engineer at Pilz
Key Points
- If an access point is to be monitored safely, with high resolution and short reaction times, light curtains are the right choice
- Safety laser scanners are suitable for area guarding of static or mobile danger zones
- Radar technologies achieve a somewhat lower resolution and edge definition on the border of the protected field
- Security impacts everyone
- Compact safety gate system
- Industrial Security is no longer optional!
- Certified machinery safety training
- Safe & smart automation solutions
- Series of Machinery Safety Courses this June from Pilz UK
- Enhance your machinery safety knowledge
- Safety first for warehouse automation
- Meets PLe For Series Connected Switches
- Safe, perfect packaging