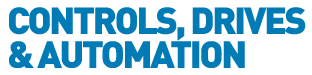
![]() |
Charlotte Stonestreet
Managing Editor |
Home> | MACHINE BUILDING & ENGINEERING | >Machinery Safety | >MACHINE SAFETY IN THE EU |
MACHINE SAFETY IN THE EU
29 October 2012
Many EU Directives and standards are applicable to the safety aspects of machinery, including control systems, but how do EU Directives develop? Leuze has published useful guidance and launched a new version of its software program SafeExpert to guide machine builders through the process
Key Points
- The laws and bodies of rules and regulations of the country in which the machine is operated always apply, even if the machine was constructed in another country
- If a product complies with the relevant harmonised EU standards, it is assumed that the basic requirements are met
- European safety standards can be divided into basic safety standards (type A standards), safety group standards (type B1 standards and type B2 standards) and machine-specific technical standards (type C standards)
Machine safety is becoming more and more important, and an integral element of machine construction. In addition to the moral obligation to protect and maintain the health of workers, machine safety also makes financial sense. Every workplace accident results in costs.
The examination and apportionment of responsibility occupies many high level departments in the company, right up to executive level.
Throughout the world, there are different concepts of machine safety and protection in the workplace. Along with differences in the requirements and evaluation of safety concepts, there are also differences with regard to responsibilities and legal consequences. The laws and bodies of rules and regulations of the country in which the machine is operated always apply, even if the machine was constructed in another country.
The European Union (EU) now has 27 member states with 500 million residents. The member states of the EU have set up bodies that apply across the Union, to which they have transferred parts of their single state sovereignty. The EU Commission and the EU Council compile Directives with basic requirements that then must be adopted by the member states into their national law. The European standards organizations, CEN, CENELEC and ETSI are then commissioned to draw up EU standards that technically solidify the applicable Directives and legal provisions.
So far, 20 Product Directives have been drawn up to dismantle obstacles to trade in the single European market. The relevant products may only be distributed if they satisfy these basic requirements. If a product complies with the relevant harmonised EU standards, it is assumed that the basic requirements are met. A manufacturer can also use other technical solutions if the same level of safety is proven.
Fulfillment of the basic requirements is determined in a formal conformity assessment procedure. Depending on the potential risk, this is performed, as much as possible, within the manufacturer's own area of responsibility.
MINIMUM REQUIREMENTS
Safety at Work Framework Directive 89/391/EEC contains minimum requirements and general basic principles for the prevention of work-related hazards, for safety and health protection, for minimising and eliminating risk and accident factors, and for the appropriate instruction of employees. These are minimum requirements. A its discretion, each EU Member State may increase the protection level in its national implementation or, for example, set higher test requirements.
Harmonised European standards specify the basic requirements of the EU Directives for safety and health protection as they are named, for example, in Annex I of the Machinery Directive. When the protective level of an applicable harmonised standard is reached, the corresponding requirement from the Directive is satisfied.
In contrast to Directives and their national implementation under the national law of the Member State, standards are not legally binding. If the level of protection described in standards of this kind is reached by other measures, then such solutions are also possible. The difference between satisfying an applicable harmonised standard and a different solution, however, does have consequences - in the latter case, the manufacturer must prove compliance with the Directive with additional documentation.
Differences can also result with the conformity procedure when harmonised standards are only partly met or no applicable harmonised standards are available.
Technical committees and the working groups below them, which for the most part are recruited from national standards committees and employees of manufacturers in the machinery manufacturing and sensor technology sector, are active in the CEN and CENELEC standards organisations with the formulation of standards in the area of machine safety. At the end of this process is an approval process in which the members of the CEN, including Switzerland, decide in accordance with a quota system for or against the adoption of a standard as a harmonised European safety standard.
A total of 29 states participate in this process. With the publication of a harmonised European safety standard in the Official EU Journal, the aptly-name "presumption of conformity" applies - it is assumed with the achievement of the protective objectives of this standard that conformity with the corresponding Directive for this safety aspect is ensured.
European safety standards can be divided into basic safety standards (type A standards), safety group standards (type B1 standards and type B2 standards) and machine-specific technical standards (type C standards).
The design principles and the basic concepts of type A standards, such as EN ISO 12100, are binding for all machines.
Instructions for determining risks that are connected with the machine can be found here.
Avenues of approach and their order for preventing risks are provided with the objective of integrating safety, even before machine manufacture begins.
Type B1 standards describe general safety aspects and provide solutions for this. Examples would be the design of hard guards, or the approach speed that is required for calculating the safety distance for safety light curtains or multiple light beam safety devices.
Special protective devices, such as E-Stop buttons, safety door switches, safety mats and strips or safety light curtains, are grouped together in the type B2 standards.
Notes on the design and testing of safety components that both the manufacturer of such products and the machine designer must take into account with the use in their machine can be found here.
Type C standards describe significant hazards, specific risks and measures for reducing these risks at special machines or machine types. If a C standard exists for the machine type in question, it takes priority over a B or A type standard. If there are additional hazards that are not addressed in the standard, or if there is no special C standard for the machine being planned, risk reduction in accordance with A and B standards must be made.
SAFETY RELATED
Parts of machine control systems performing safety tasks are described by those who set standards as "safety-related parts of control systems". These parts can consist of either hardware or software and stand-alone or integrated components of the machine control system. Safetyrelated control components incorporate the entire effective chain of a safety function provided by sensor, control unit and actuator.
Each can be set up in different ways, and, for example, may consist of a safety switch and a safety relay, or they can also be implemented as a safety related PLC of an entire system.
The general objective is to design these control components so that the safety of the control function and the behaviour of the control unit in case of a fault corresponds with the level of risk reduction determined in the risk assessment.
Specific control-related measures for fault prevention in systems used in low-risk applications may not be sufficient for applications with a higher risk. For these applications, for example, additional measures for fault tolerance or fault detection would then be required. The higher the risk reduction to be provided by the safety-related control component, the higher the required safety level or the safety-related performance level of the control component.
The standards described in Table 3 use different classification systems and definitions for these safety levels.
- 2D-code readers get automation rolling
- Material flow with safety
- Small but mighty: always on the right rack
- Reliable navigation with safety laser scanner RSL 400
- "With AI we can find the needle in the haystack"
- Quick-action integration via IO-Link
- Muting reinvented
- Safety to the Power of 3
- Laser diffuse sensor
- New guidelines for safer sensor positioning
- MAKING SENSE OF SAFETY
- Handwheel Valve Position Indicators
- Modular Heavy Duty Interlocks
- SAFE APPLICATION OF RCDS WITH VSDS
- Requires Little Installation Space
- Failsafe Element
- Versatile Machine-Guarding
- Meets PLe For Series Connected Switches
- Improved Arcing Protection
- Free-To-Access Machinery Safety Manual