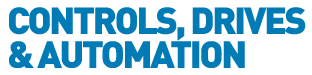
![]() |
Charlotte Stonestreet
Managing Editor |
Home> | DRIVES & MOTORS | >AC Motors | >Downtime minimised |
Editor's Pick
Downtime minimised
28 April 2020
TEC, the UK’s largest electric motor distributor, has collaborated with Newton Tesla, a leading supplier of inverters, to help a plastic extrusion facility overcome downtime
Plastic extrusion is a heat process, which means equipment operates optimally at a higher temperature range. If the line is stopped due to motor failure, equipment can develop faults and seize as it cools below its operating threshold. This knock-on effect can increase required maintenance work, and consequently, the overall cost of downtime. Carrying out maintenance work fast is therefore imperative.
Andy Donaldson, Regional Sales Manager at TEC Motors, sets the scene: “A 300 kW square frame DC motor had failed on the line, so a quick replacement was required. At TEC, we offer motors up to 630 kW off the shelf - our service relies on delivering big motors quickly. However, sourcing DC motors within an economic timeframe for this project simply wasn’t possible. A DC motor refurbishment would also be time consuming, so the current motor specification was actively holding up repair work.
“After visiting the line and assessing the options, it was decided to replace the DC motor with an AC alternative. An AC motor was readily available, but it would require some specialisation to ensure an optimum replacement.”
Accurate speed holding
After evaluating the DC motor kW / base speed, it was clear that a TEC 280 kW 4 pole AC motor would actually produce 20% more torque than the 300 kW DC unit.
An inherent benefit of DC motors is their ability to run at very slow speeds thanks to high levels of control. AC motors are less adapted to this, so to compensate TEC factory fitted an encoder to the new motor to give accurate speed holding over the entire speed range with full torque. Clearly a new inverter control panel to replace the old DC controls was required - which is where Newton Tesla comes in.
George Newton, Managing Director at Newton Tesla, commented: “We are experts in the design and manufacture of control panel systems and supplying inverters for systems up to 2,000 kW. The combination of our expertise and our stock items has enabled us to work with TEC to get the customer up and running as quickly as possible.”
With an inverter fitted to ensure efficiency at slow operating speeds, attention moved to cooling. Traditionally, AC Motors mount cooling fans to the rotor at the back of the device, which rotates at the same speed as the output shaft. However, this can present cooling issues during slow speed operation with an inverter. The solution was to fit a force ventilation fan which delivers the required cooling, regardless of motor speed. TEC offer this forced cooling option from stock across the range.
A new motor plinth and coupling were manufactured and delivered to site to house the motor - all managed by TEC. An insulated bearing and thermistors were also fitted to the motor to ensure long-term durability for the application. The inverter monitors the temperature of the motor windings, shutting it down in the case of overload.
The end customer was delighted with the upgrade as the new AC motor requires very little maintenance compared to the DC motor which required frequent attention to the brushes and commutator. The reduced maintenance allows the extruder to run for longer periods, making the line more efficient.
Donaldson concludes: “With our expertise in motors and Newton Tesla’s on-site inverter services, we were able to have the new AC motor and inverter up and running within 10 days of the initial failure. This ensured that extruding could continue at the facility within a shorter timeframe, which helped to minimise the risk of downtime to other equipment on the line
“In this case, a combination of our on-site services, our inherent knowledge of motors and supply flexibility meant we could overcome this issue in a timely manner for the customer.”
Key Points
- Continuous processes require the utmost equipment reliability, so when a large drive motor fails a replacement is needed quickly
- In this case it was decided to replace the DC motor with an AC alternative which required some specialisation
- TEC factory fitted an encoder to the new motor to give accurate speed holding over the entire speed range with full torque
- HIGH EFFICIENCY
- BAE SYSTEMS TEAMS WITH QINETIQ TO DELIVER HYBRID ELECTRIC DRIVE
- Efficient Drives
- Loher motors available in UK
- HYGIENE SENSITIVE
- Surpass European Efficiency Levels
- EXTENSIVE STOCK & RAPID DELIVERY
- QUANTUM DELIVERS THE FACTS TO CLEAR UP THE FICTION
- IMPROVED MOTOR CONTROL
- Updated installation guide for power drive systems