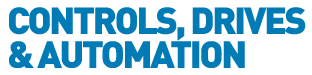
![]() |
Charlotte Stonestreet
Managing Editor |
Editor's Pick
Vision for transition
03 October 2024
Building machine vision into a factory’s smart infrastructure creates a wealth of opportunities to make operations more efficient. Ankur Tomar looks at the possibilities

THE TRANSITION to Industry 4.0 sees advanced sensors working hand in hand with embedded software and sophisticated data analysis tools to create smart factories. Adding the connectivity provided by the Internet of Things and cloud computing infrastructure creates additional value by linking with other aspects of the business. These rapid advances require a solution for everything from keeping track of inventory to maintaining quality control, at costs affordable to businesses of all sizes.
Machine vision is one example of this trend in action. Although it has been around since the first simple systems were introduced in the 1970s, it is becoming increasingly relevant because of its ability to underpin systems that are not just faster and more efficient but can free up valuable human capital.
It is important to distinguish machine vision from the computer vision systems which process images and interpret them based on algorithms; a machine vision system uses a camera to capture image data that computer vision can work with, often making decisions that are the basis for instructions to other system components.
Vision in Industry 4.0
The ability of Industry 4.0 to create high-value, innovative solutions based on data-sharing between different elements is a compelling reason to introduce machine vision in processes where it may not have previously played a part. The growing importance of AI in manufacturing is boosting this trend. AI models trained with existing data captured by machine vision systems can use deep learning inference to recognise the most subtle anomalies. Input doesn’t have to be in the traditional form of two-dimensional photographs either. It can come from thermal or infrared sensors, and machine vision systems are increasingly able to process three-dimensional and moving images.
The sheer number of potential applications for machine vision within the context of Industry 4.0 transition can make it hard for a business to know where to start. Benefits can be extensive, but adoption isn’t a case of simply buying a few cameras and dotting them around a manufacturing facility. It requires foresight, planning, and – most importantly – a clear definition of what needs to be achieved.
The good news is that even a relatively modest investment can be justified by the measurable returns in terms of improved flexibility, automation, product design, manufacturing, workforce optimisation and power consumption.
Fundamentally, machine vision excels at the repetitive, focused tasks that even the most patient human can find challenging to focus on for extended periods of time. Electronics manufacturing provides a good example of the benefits of careful adoption. A semiconductor manufacturer still using manual inspection to check wafers as they are fabricated could free up workers for more productive tasks by letting them work hand-in-hand with automated quality control that is faster, more efficient and more accurate than even the best trained humans. Similarly, monitoring components as they pass through a PCB etching process is the sort of tedious task that can be performed to a consistently high standard - right through to final packaging - by an infinitely patient machine-vision system.
Beyond quality control
In an Industry 4.0 environment, machine vision’s role can expand to monitoring every aspect of how a facility operates. Imagine being able to walk around a factory and ‘seeing’ in real time where a pipe is approaching – or has exceeded – its normal operating temperature or is vibrating a little more than it should. Machine vision makes that possible by providing data gathered by thermal imaging and motion-capture cameras. Once monitored by AI models capable of spotting anomalous behaviour, information can be passed straight to maintenance engineers via an augmented reality interface so that the potential problem can be assessed, and action is taken proactively.
Another application enabled by AI is the ability to reinforce health and safety protocols. A machine vision system backed up by algorithms that know which locations within a facility are restricted, who is allowed to enter and what protective equipment they require can keep an eye on this aspect of operations more efficiently than relying on human monitoring.
But it doesn’t stop there as the limits of AI’s potential applications are unknowable. For example, the ability to automate inventory management provides accurate tracking, reduces errors, and optimise stock levels, which minimises excess inventory and reduces storage costs.
In terms of sorting and packaging, AI can ensure accurate and efficient use of materials, which reduces waste. Of course, waste monitoring itself can also be controlled by AI to identify and reduce the number of waste-generating activities.
Utilising machine vision-guided robotic systems to improve precision and reduce material handling errors can also vastly improve many aspects of material handling, not least of which are safety compliance protocols, which can be monitored and enforced to reduce the risk of accidents and resource losses.
What’s on offer
Machine vision technology is ideal for use where machines of varying types are constantly connected and interacting, which is in part why it is being so rapidly adopted for many different applications. This rapid take up is, in large part, due to the affordability of the components, which in turn fuels the ability to develop a wider range of improved hardware and software. Although every business will approach the adoption of machine vision at a pace that makes sense for their organisation, the best option will typically depend on clearly identifying the specific benefits expected and how those benefits will enhance the overall strategy.
For many, the primary benefit of machine vision will be the ability to gather, process and automatically act on huge volumes of information – all in a fraction of a second. This is what Industry 4.0 is all about, and those data processing and analysis capabilities alone are compelling enough reasons to get started.
Fortunately, the availability and affordability of a range of components makes it easy to get started without committing to significant investment. As well as evaluation kits from well-known names including Analog Devices and Microchip, Farnell’s extensive machine vision offering includes affordable and open-source solutions from vendors such as Raspberry Pi, BeagleY-AI and China’s LattePanda as well as Arduino’s Portenta & Nicla family. AMD Xilinx offers the Kria-26 system on module, optimized for vision, AI and robotics applications, while NXP’s EdgeReady range has hardware and software AI solutions for vision applications like facial recognition. AI machine vision sensors from HUSKYLENS are another low-cost and simple way of starting a machine vision journey.
And the number of options extends to devices like the Hamamatsu evaluation board and mini-spectrometer; Pepperl+Fuchs’ event camera; and Omron Industrial Automation’s monochrome camera to name a few. These and other advances are further raising the bar of what is possible with machine vision devices and technologies.
Whatever path you take, it is already clear that machine vision is the cornerstone of the digitalisation of manufacturing. As Industry 4.0 rapidly becomes the norm, companies that delay at least considering how they will use machine vision run the risk of losing vital ground to their more ambitious competitors.
Ankur Tomar is technical marketing manager at Farnell
- Smart sensors whitepaper
- WIN an IIoT Starter Pack sponsored by Schneider Electric!
- Industry 4.0 ebook
- Keep on running
- Farnell launches fourth global IoT survey
- Whitepaper to support purchasing professionals
- Latest products from TE Connectivity available from Farnell
- Farnell appoints new VP of eCommerce
- Farnell expands offering of energy-saving products
- Farnell scoops global performance award
- No related articles listed