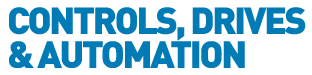
![]() |
Charlotte Stonestreet
Managing Editor |
Predictive tool to improve human-machine interactions
08 August 2018
As manufacturing shifts towards smart factories, with interconnected production systems and automation, engineers at the University of Nottingham are leading a £1.9m project to develop a predictive toolkit to optimise productivity and communication between human workers and robots.
DigiTOP is one of seven national projects to create novel digital tools, techniques and processes to support the translation of digital capabilities into the manufacturing sector, funded by the Engineering and Physical Sciences Research Council (EPSRC).
It comes following the industry-led Made Smarter review, chaired by Siemens Chief Executive Juergen Maier, which stated that industrial digitalisation could be worth as much as £455bn to UK manufacturing over the next decade.
A digital toolkit for the optimisation of operators and technology in manufacturing partnerships, DigiTOP will be led by Professor Sarah Sharples at the University of Nottingham in collaboration with Loughborough University, Cranfield University, University of the West of England, BAE Systems, Babcock International, Synertial Labs Ltd, Artinis Medical Systems B.V., High Value Manufacturing (HVM) Catapult and Jaguar Land Rover.
The toolkit will focus on using human factor theories and data to digitally capture and predict the impact of digital manufacturing on future working practices. Demonstrators will be used to test the implementation of sensing technologies that will capture and evaluate performance change and build predictive models of system performance.
The project will also provide an understanding of the ethical, organisational and social impact of the introduction of digital manufacturing tools and digital sensor-based tools to evaluate work performance in the future workplace.
DigiTOP's findings will help companies that are planning to implement digital manufacturing technologies to understand how it will alter working practices, and how to optimise workplace designs to take these changes into account.
The tools developed within DigiTOP will help industry to design future work which might take place with a human and robot working in collaboration to complete a task or help with understanding how to design a data visualisation which shows how current parts of the factory are performing, and where maintenance or systems change might be needed in the short or long-term future.
Professor Sharples said: “The manufacturing industry, with the drive towards 'Industrie 4.0', is experiencing a significant shift towards digital manufacturing. This increased digitisation and interconnectivity of manufacturing processes is inevitably going to bring substantial change to worker roles and manual tasks by introducing new digital manufacturing technologies to shop floor processes.
“It may not be enough to simply assume that workers will adopt new roles bestowed upon them; to ensure successful worker acceptance and operational performance of a new system it is important to incorporate user requirements into digital manufacturing technologies design.
“New approaches to capture and predict the impact of the changes that these new types of technologies, such as robotics, rapidly evolvable workspaces, and data-driven systems are required," adds Professor Sharples, who is Associate Pro-Vice Chancellor for Research and Knowledge Exchange for Engineering at Nottingham.
"These approaches consist of embedded sensor technologies for capture of workplace performance, machine learning and data analytics to synthesise and analyse these data, and new methods of visualisation to support decisions made, potentially in real-time, as to how digital manufacturing workplaces should function.”
The EPSRC investment arose out of work conducted by the Connected Everything Network Plus, which was established to create a multidisciplinary community focussed on industrial systems in the digital age.
EPSRC’s Executive Chair, Professor Philip Nelson, said: “The adoption of advanced ICT techniques in manufacturing provides an enormous opportunity to improve growth and productivity within the UK.
“The effective implementation of these new technologies requires a multidisciplinary approach and these projects will see academic researchers working with a large number of industrial partners to fully harness their potential, which could generate impact across many sectors.”
- 3D Hubs launches Online Engineering Summit series
- £10k manufacturing grant for start-ups directed by under 30s
- Driving Trends & Developments
- Chancellor backs 4IR at parliamentary group launch
- What is driving demand for ultra-low voltage motors and drives?
- Laser Interferometry & automated manufacturing
- Williams Racing announces new tech partnership
- Ai-Da Robot announced as artist in residence at Glastonbury
- Cutting-edge motor-drive design hub
- What does maintenance mean for aerospace?
- No related articles listed