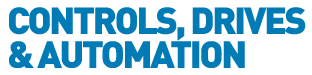
![]() |
Charlotte Stonestreet
Managing Editor |
Home> | DRIVES & MOTORS | >DC Drives | >Driving Trends & Developments |
Home> | DRIVES & MOTORS | >Induction Motors | >Driving Trends & Developments |
Home> | CONTROLS | >Motion Controls | >Driving Trends & Developments |
Driving Trends & Developments
17 January 2013
Two major industry events took place in November. Following hard on the heels of the Motor Drives Systems Conference (MDS) in Solihull was the SPS Drives exhibition in Nuremberg. Andy Pye visited both and reviews the trends and key developments
To some degree, MDS and SPS are events at the opposite ends of the drives spectrum. The MDS Conference attracted around 50 delegates to a small hotel in Solihull to hear a small series of high profile speakers, while SPS occupied 10 halls of one of the largest exhibition complexes in Europe and targets an audience of some 50,000 visitors.
The main focus of MDS is the financial and energy efficiency benefits of adopting a systems-based strategy to motor-driven equipment. Enabling investment in technologies such as low energy lighting, energy-efficient motors, low carbon air conditioning, solar photovoltaic and biomass heating helps businesses cut costs, reduce energy waste and supports UK goal of lower carbon emissions.
Electric motor systems use approximately 40% of total global electricity, and their share in industrial electricity consumption is much higher, standing at 65%, according to the International Energy Agency. According to a recent study published by Siemens Financial Services, full implementation of variable speed drives (VSDs) on motors could help the UK industry save up to £2503 million of energy costs over the next five years.
However, the full energy and cost-saving potential of VSDs is a long way from being realised. Globally, the penetration of VSDs (as a proportion of installed motors) is still low, with market penetration of VSDs in the UK as low as a mere 10%.
Similarly, as motors usually run for thousands of hours every year, any gain in efficiency by replacing motors with higher efficiency versions will translate into considerable savings which would pay for the investment in a few years and in some cases even months.
Any gain in efficiency by replacing motors with higher efficiency versions will translate into considerable savings
Why is the UK so slow to take advantage? Steve Brambley of GAMBICA showed that £20,000 invested in energy efficient equipment would return £180,000 in 10 years – a far better return than you could expect from ISAs, investment in housing stock or the stock market.
In the UK, access to capital for companies has been highly restricted since the financial crisis, and the squeeze continues because of factors such as slow economic growth and concerns about stability in the Eurozone.
So how can businesses afford investment in energy efficiency in the current continuing credit squeeze? To help companies overcome the financial barrier of investing in energy-saving technologies, the Carbon Trust and Siemens Financial Services Limited (SFS) have launched the Energy Efficiency Financing scheme. It is designed to provide finance for organisations acquiring energy-efficient equipment, with affordable monthly payments designed to match – and be offset by – the average monthly savings on energy bills, effectively meaning the equipment pays for itself. In some cases, the savings can be greater than the monthly costs, allowing the end customer to be cash positive from day one.
The service is aimed at all organisations who have been trading for more than 36 months and are seeking to reduce their own energy use.
Another way to improve the energy-efficiency of motors is to move to high energy motors. A wealth of information is available from the European Community on the Energy Efficiency of the so-called EuP Lot 30, otherwise known as Electric Motors and Drives. Motors in the power range of 0.75-375kW manufactured in or imported into the EU after June 2011 must have met or exceeded the IE2 efficiency level as defined in the IEC 60034-30 standard until the end of 2014.
The next stage in this programme is that motors with a power rating over 7.5kW manufactured in or imported into the EU after 1 January 2015 must meet or exceed the IE3 efficiency level as defined in the IEC 60034-30 standard. Motors with a power rating over 0.750kW (included) manufactured in or imported into the EU after 1 January 2017 must meet or exceed the IE3 efficiency level as defined in the IEC 60034-30 standard.
WEG’s W22 Super Premium Efficiency line of induction motors, featured at SPS Drives, is believed to be the only complete standard range currently available that meets the yet-to-be-ratified IE4 regulations. This is achieved by incremental attention to all the areas in motors where losses occur, such as mechanical losses, stray losses (SLL) and iron losses (Pfe).
The PowerXL variable frequency drives offer different open and closed-loop control methods
Drives eliminate wiring
Eaton launched PowerXL variable frequency drives with a rating up to 250kW for the machine building and panel building sectors. Pluggable modules enable the PowerXL variable frequency drives to be incorporated quickly and simply into the company’s SmartWire-DT connection and communication technology, eliminating control circuit wiring.
There are two models: the DC1 Compact and the DA1 Advanced Machinery Drive. The DC1 is the basic model covering ratings from 0.37 to 11kW, and was developed for applications where robust design, availability and universal functionality are the main requirements. The DA1 series is designed for ratings from 0.75 to 250kW, and is suitable for demanding, high performance use. The PowerXL variable frequency drives also offer different open and closed-loop control methods. The DC1 controls the motor with U/f characteristics, enabling increased torque and allowing the inverters to operate the motors at 150% of the rated power for 60s, and at 175% for 2s.
From an energy efficiency viewpoint, the DA1 series supports both the standard three-phase motors that normally comply with the current IE2 and IE3 standard, as well as the highly efficient permanent magnet motors (such as that from WEG) that are designed for the future IE4 standard.
Siemens platform upgrade
Siemens announced the first major upgrade to its 16 year old Simatic S7 platform. The S7-1500 is a new controller platform targeted to replace the mid-range S7-300 family immediately, but will also eventually replace Siemens’ high-end S7-400 controller family. In turn, the S7 succeeded the Simatic S5 after 17 years, but the two platforms were still sold in parallel for many years after that, resulting in net lifetime for the S5 of over 25 years.
The new S7 hardware is an opportunity for Siemens to take a great leap forward not just in speed, but also in other areas like integrated diagnostics resulting from more intelligent, self-diagnosing hardware and peripheral devices.
The S7 platform now integrates motion control in the PLC. While other suppliers have offered this for many years, Siemens developed and promoted a second platform called Simotion as its primary platform for motion-heavy applications. Now, the PLC can take care of planning and executing motion commands and sending motion data via Profinet directly to the drives. However, Siemens has stated that the integrated motion in the S7-1500 will be at the basic level and that Simotion will remain the controller of choice for motion-intensive applications.
Automation software
Beckhoff's TwinCAT 3 automation software suite was released in late 2011. Though the release of TwinCAT 3.1 is planned for the second quarter of 2013, Beckhoff presented a pre-release at SPS IPC Drives 2012, Germany. A major new item is support for 64-bit operating systems. This makes more effective use of RAM possible. Nowadays, PCs are equipped as standard with a 64 bit version of the Windows operating system. The TwinCAT runtime can now also be used on these PCs alongside the engineering environment. The PLC runtime for Windows CE operating systems is also supported with TwinCAT 3.1.
Version 3.1 of TwinCAT provides the user with new and extended functions: integration in Microsoft Visual Studio 2012 means that the latest version of the software suite can now be used. The source code control databases such as Microsoft Team Foundation Server or Subversion are available in TwinCAT 3.1, including a compare-and-merge function for all programming languages. Configuration and programming can be generated automatically with the extended automation interface, which is new for the PLC sector.
TwinCAT 3.1 also offers extended possibilities for Motion Control applications; for example, by integrating transformations conveniently in NC I and CNC. New Scope 2 functions facilitate the display and analysis of data even over a long period with many new trigger functions. Additional reporting and print functions are available. The user benefits from the co-operation with TwinCAT Scope 2 in particular in connection with the Condition Monitoring library.
In addition, the TwinCAT OPC UA implementation has been extended by function blocks. A connection from the PLC to a further OPC UA server can be established directly via the OPC UA channel.
The DC drives of Sprint Electric’s PLX range are available as two quadrant or regenerative four quadrant types
Digital DC drives heavy industry
Sprint Electric presented its range of digital DC drives up to 2250A for controlling DC motors used in heavy industry applications such as metalworking, steel mills, mining, or the cement, rubber and plastics industries. Thanks to the new control technology drive.web, the drives can be controlled over the Ethernet without the need for a PLC or supervisory computer.
The DC drives of Sprint Electric’s PLX range are available as two quadrant or regenerative four quadrant types. All models ranging from 650 to 2250A (980kW) are offered with two AC busbar position options: top entry or bottom entry. This means that for retrofit installations the two options make it easier to use the existing cabling and will save the cost of adding more expensive copper cabling; In new designs, the choice of wiring options can save money and space when designing new control panels. This increased drive range is available as high voltage (690VAC) or standard voltage (480VAC) models. A 690V AC supply allows the use of 750V DC armature motors. Compared to the standard voltage this provides an increase in shaft power, up to 1500 KW/2000 HP for the 2250A model. That is 50 percent more power delivered without an increased cable size.
The PLX has an extensive range of software functions and fieldbus communications options such as Profibus, DeviceNet, CC-Link, EtherNet/IP, Modbus and CANopen. The Ethernet-based drive.web control system includes graphical configuration tools that provide diagnostics and configurability of all drives on the network, either locally or remotely via the Internet. The graphical tools allow the full configuration of the drives, provide service diagnostics, full documentation and an operator interface for local control.
Key Points
- Electric motor systems use approximately 40% of total global electricity
- The full energy and cost-saving potential of VSDs is a long way from being realised
- To help companies overcome the financial barrier of investing in energy-saving technologies, the Carbon Trust and Siemens Financial Services (SFS) have launched the Energy Efficiency Financing scheme
- Alternative to furlough urged for engineers
- Machine tending automation
- Future technologies receive government cash boost
- AVEVA expands collaboration with Microsoft with focus on Cloud & AI
- Industrial control & factory automation worth USD 293.2b by 2025
- £450m fund to unlock innovation in gas & electricity networks
- What can be learnt from the Oldsmar water supply hack?
- £10k manufacturing grant for start-ups directed by under 30s
- Industry 4.0 enabler
- Drive to improve efficiency & reduce emissions