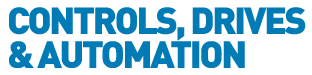
![]() |
Charlotte Stonestreet
Managing Editor |
A (re)shore thing?
20 January 2021
While the coronavirus has seen many UK businesses step up to the mark and fulfil incredibly important roles under unprecedented circumstances, there is also no doubt that the crisis has also exposed weaknesses in many UK supply chains and highlighted just how much reliance there is on the the supply of critical items from overseas.
In the early days of lockdown the severe shortage of PPE, ventilators and critical components for medical devices, and the impact seen throughout the NHS was stark reminder that much of UK manufacturing has depended in overseas production of decades.
Of course, there are many valid reasons (mostly financial) for offshoring elements of production - but as we have seen recently, when the extraordinary happens we are left with little control in terms of delivery, costs, and even quality. So then, is it time to consider reshoring? Well, it would certainly seem so. And the movement isn’t solely driven by global pandemic either.
Even before the global threat from COVID-19 there seemed to be a a trend amongst OEMs to consider the benefits of reshoring. Indeed, the University of Warwick’s ‘Realities of Reshoring: A UK perspective’ survey of 262 UK manufacturing organisations, carried out in association with Reshoring UK, asserts that the global economic crisis of 2008 forced companies to re-evaluate their manufacturing location decisions and was perceived to have accelerated the trend towards reshoring manufacturing back to the UK. This has only been exacerbated by Brexit, particularly as the possibility of ‘no deal’ circumstances raises the possibility of severely disturbed supply chains.
In Lloyds Bank’s 2019 report ‘Business in Britain: Manufacturing’, more than a third of firms said they were planning to move manufacturing processes back to the UK that had previously been offshored to territories including Asia and eastern Europe. The prime motive for this, cited by 71% of those with these plans, was to improve quality – a telling endorsement, said Lloyds, of the high standards that British manufacturers and workers uphold, which could also have positive implications for UK supply chains.
To assist manufacturers connect with trusted, accredited suppliers capable of delivering UK-based products and services, leading industrial engineering associations are working together on the Reshoring UK initiative (details at www.reshoring.uk). Members include Gambica, the High Value Manufacturing Catapult, and BCAS, to name just a few.
Another member of Rehoring UK, the Manufacturing Technology Centre is helping Albert Jagger Engineering to reshore component production from China. The Bloxwich-based supplier of commercial vehicle engineering and industrial hardware has already re-shored production of almost a quarter of a million fastening components and in the process has, in some cases, reduced costs by up to 50%.
An SME team from the MTC's Manufacturing support Services operation worked with Albert Jagger to revolutionise its factory; producing a new factory layout, introducing new technology including CNC machines and automation, and re-training staff using virtual and augmented reality.
As a result the firm was able to produce fastening components which had previously been imported from China for between 20% and 50% of the cost. In addition it has slashed stockholding costs by 50% and created space in the factory for future growth.
While reshoring is by no means without challenges, results like these are certainly a fantastic advertisement.
- We have the technology
- Automation gets a bad press - again
- What would you do with Arduino?
- Manufacturing at increased risk of cyber attacks
- Manufacturing needs its mojo
- Digital skills gap grows
- Industry 5.0 - coming to an industrial facility near you soon
- Adapt & specialise
- The new norm
- A game of catch up?
- No related articles listed