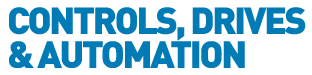
![]() |
Charlotte Stonestreet
Managing Editor |
Home> | IIot & Smart Technology | >Big Data | >Right here, right now |
Home> | AUTOMATION | >Condition Monitoring | >Right here, right now |
Home> | IIot & Smart Technology | >Connectivity | >Right here, right now |
Editor's Pick
Right here, right now
03 March 2025
While Rockwell's Automation Fair brings the future of industrial operations to life, the event also acts as a showcase for what is already being achieved. Charlotte Stonestreet reports

OPENING THE “Making it Matter’ keynote, senior vice president lifecycle services, Matt Fordenwalt talked about what Rockwell is achieving in the here and now using a multitude of different technologies.
“For decades, Rockwell has been synonymous with industrial automation, and with decades of experience, we see an opportunity to take this forward, to move towards industrial autonomy,” said Fordenwalt “Autonomous operation is really a combination of programming with learning and adapting to the environment around you. And it’s possible now with advances of multiple different technologies like artificial intelligence, robotics, and advanced computing power.”
In order to expand automation into previously untapped areas, such as material movement within a facility, Fordenwalt talked about a three-pronged approach: Technological innovation; a system model to ensure the technology fits together; and domain expertise to achieve desired outcomes. “We are taking a systems approach to ensure that everything we do works seamlessly together, with relevant data that is readily available to drive innovation. The simplified experience we aim to deliver spans all roles and the entire equipment lifecycle – from engineers programming the system, to operators running it on the plant floor, to maintenance teams providing ongoing support,” said Fordenwalt.
He also emphasised the importance of people in this picture. “At Rockwell Automation, people are at the centre of all that we do. We combine the imaginations of people with the potential of technology to expand what's humanly possible, empowering people to work differently; empowering and enabling people and machines to work more closely together.”
Integrated content
Taking up the narrative, senior vice president software and control Matheus Bulho started by talking about IT/OT convergence, particularly when it comes to how automation software content is developed. He pointed out how in large projects with multiple people contributing to the same codebase, integration often happens at the very end – right when the machine is expected to be operational, producing products, and generating revenue. However, this approach often reveals numerous integration issues, as components have been developed independently without continuous testing. This not only drives up engineering costs but also significantly delays the machine’s ‘time to value’.
“So the idea of continuously integrated content, making it easier for multiple people contributing to the same code base, having a single pipeline of content that's always green, that's being tested and always ready for deployment, is something that we've been very serious about,” said Bulho.
Once environments are in the cloud, it becomes much easier to provide an Office 365-like experience. This includes native integration of version control systems within FactoryTalk Optix Studio, along with a FactoryTalk Design Studio environment that allows users to easily visualise code conflicts from multiple contributors, resolve them efficiently, and push the changes into a single, continuously ready pipeline. Rockwell is also actively working to simplify the adoption of modern DevOps workflows for software development within its environment, and users can expect to see ongoing improvements in this area.
Virtual environment
Moving on, Bulho described Rockwell’s concept of a complete technology stack that enables users to design and commission entire systems in a virtual environment. FactoryTalk Echo provides a high-fidelity virtual representation of Logix, seamlessly connected to Emulate3D, which provides virtual models of Rockwell devices –including I/O, drives, and entire machines.
“And now with our partnership with Nvidia, what you see is the ability to take that to the next level. You know, with the integration between emulate 3d and NVIDIA Omniverse, you can bring in multiple models from multiple machine builders all together into a single virtual representation of an entire production line,” continued Bulho.
Another area Rockwell has been actively focused on is integrating co-pilot capabilities into the design environment, particularly within FactoryTalk Design Studio. This is achieved through an agent-based approach to co-pilot functionality. Currently, FactoryTalk Design Studio supports multiple user roles, each capable of performing various tasks within the platform.
Often one person will design a system, while another is responsible for operating and maintaining it. That’s why, beyond just creating content, it’s equally important to clearly explain structure and purpose, asserted Bulho. Over time, FactoryTalk Design Studio will incorporate more autonomous agents that not only generate code but do so within the specific context of individual specifications.
Software-defined automation
When it comes to software-defined automation, Rockwell takes a broad view; not just as a control system form factor, but as a foundational concept the company has embraced for years. In fact, decades ago Rockwell introduced the first tech-based control system with Logix, which eliminated the need for rigid, fixed I/O memory mapping during application design, offering greater flexibility and efficiency. This enabled users to define logic entirely in software and later bind it to the I/O in their production system – an approach that has continued to evolve.
“For example, in FactoryTalk Design Studio today, not only can you bind I/O later in the process, but you can also defer execution binding. Applications are created in an object-oriented manner, fully abstracted from where they run or how many control systems they use. This flexibility allows you to develop a single entity and later decide whether to deploy it to one or multiple controllers. Even our I/O hardware now includes software-defined capabilities,” said Bulho.
He went on to cite as a example the Flex 5000 HART I/O. The physical layer of this process I/O is entirely software-defined. With a single piece of hardware, users can configure it in software as an analogue input, analogue output, digital input, or digital output, providing maximum flexibility. Rockwell’s visualisation system, Optix, follows the same principle. Users can create a single visualisation runtime without needing to specify the hardware upfront. Later, they can choose to deploy it on Rockwell hardware or on open platforms, for example an ARM or x86 machine, running Windows or Linux.
Another investment area for Rockwell has been developing ArmorBlock products, including ArmorBlock, ArmorKinetix, ArmorPowerFlex, and ArmorMiniBanks. The goal here is to simplify equipment construction by significantly reducing, or even eliminating, the need for control cabinets.
The company is also innovating to simplify applications where cabinets are still a necessity; an Ethernet/IP-in-cabinet solution, for example, streamlines industrial component wiring and drastically reduces termination requirements.
Operation and maintenance
Beyond the design process, once equipment has been manufactured and is in use, the focus shifts to operation and maintenance. As Bulho emphasised, operating and maintaining equipment effectively requires a clear understanding of its performance. To achieve this, users need seamless access to reliable, contextualised data within the application, something which Rockwell has long been facilitating. From pioneering the first tag-based control system – and effectively eliminating fixed memory mapping – to enabling robust user-defined data types and open, unmodified Ethernet for simplified data flow, the company has continually advanced how information moves between equipment and systems. Standardised, rich data sets ensure consistent device representation within the control system, culminating in Smart Objects that natively provide key insights into machine performance.
Beyond monitoring industrial operations, Rockwell provides the means to optimise performance. One example of this is FactoryTalk Analytics VisionAI, hailed by Bulho as a breakthrough in simplifying vision control systems. This sensor-agnostic solution leverages machine learning to recognise good and bad parts, making advanced vision technology more accessible. The system is trained in the cloud but runs on-premise, and because of its deep integration with Logix, it doesn’t just detect issues, it enables a fully closed-loop quality control system.
In addition to VisionAI, Rockwell is also enabling autonomous control with Logix AI, which applies machine learning to understand relationships between control inputs and autonomously optimise outputs – without requiring manual programming.
“So this idea of not only detecting issues with machine learning, but also applying autonomous control to correct issues is here for you today,” said Bulho.
And this goes for maintenance too, with Rockwell’s Guardian AI which brings the ability to leverage sensing capabilities already present in industrial plant and equipment. It continuously monitors signals and uses that data to detect maintenance needs proactively. The first implementation of Guardian AI integrates with PowerFlex devices, and the company will continue expanding support for more devices in the future.
Guardian AI helps users shift from reactive to predictive maintenance. When combined with the CMMS solution, Fiix, and its built-in predictive capabilities, users can automate workflows for creating and managing work orders, as well as streamlining maintenance operations.
Connected machines
Continuing the address, senior vice president intelligent devices, Tessa Myers spoke about Rockwell’s efforts in driving end-to-end performance in manufacturing by helping customers build on the foundation of high-performance, smart, connected machines. The focus is on creating a unified system rather than isolated machines, processes, or islands of automation. The goal is to coordinate and optimise production planning, material movement, and production execution.
“Our vision at Rockwell is to enable you with highly automated systems that allow you to orchestrate and execute across your entire production cycle,” said Myers. “We're bringing together the technology in an integrated solution that makes it easier for you to deploy and faster for you to get to value. Our vision of this in-work, end-to-end, well orchestrated manufacturing system – we refer to that as Production Logistics.”
Production Logistics is all about driving optimisation, reducing costs, and increasing efficiency across the entire manufacturing supply chain. By combining operations management software with advanced material handling technologies – such as independent cart systems, integrated robotics, and autonomous mobile robots (AMRs) – Rockwell aims to help manufacturers create more streamlined and intelligent workflows.
“There's an enormous opportunity in manufacturing for us to reimagine how material moves through our manufacturing lines and processes,” said Myers. “And the ability to autonomously move production and product through manufacturing facilities gives the ability to unlock substantial benefits in terms of cost, labour, efficiency, quality and safety.”
Rockwell’s overall approach isn’t just about technology – it’s about empowering teams. With the right tools and infrastructure, teams can make faster, more informed decisions, driving operational performance and maximising the potential of equipment, assets, and overall operations, asserted Myers.
You can catch up with more of the Automation Fair keynotes on demand at:
www.rockwellautomation.com/en-gb/events/automation-fair-on-demand.html
- Versatile Machine-Guarding
- Makes short production runs more efficient
- Just enough control
- Deploying wireless equipment in The Connected Enterprise
- Rockwell Automation Releases New DCS Migration White Papers
- Visualisation for visionaries with a cloud-based HMI platform
- Rockwell acquires ESC Services
- Taking on the challenge
- Integrated condition monitoring
- Variations in product variety and volume resolved