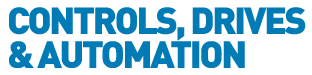
![]() |
Charlotte Stonestreet
Managing Editor |
Home> | AUTOMATION | >Condition Monitoring | >Integrated condition monitoring |
Editor's Pick
Integrated condition monitoring
10 March 2015
Manufacturers can monitor and protect machinery at a lower total cost of ownership with the Allen-Bradley Dynamix 1444 Series monitors from Rockwell Automation.
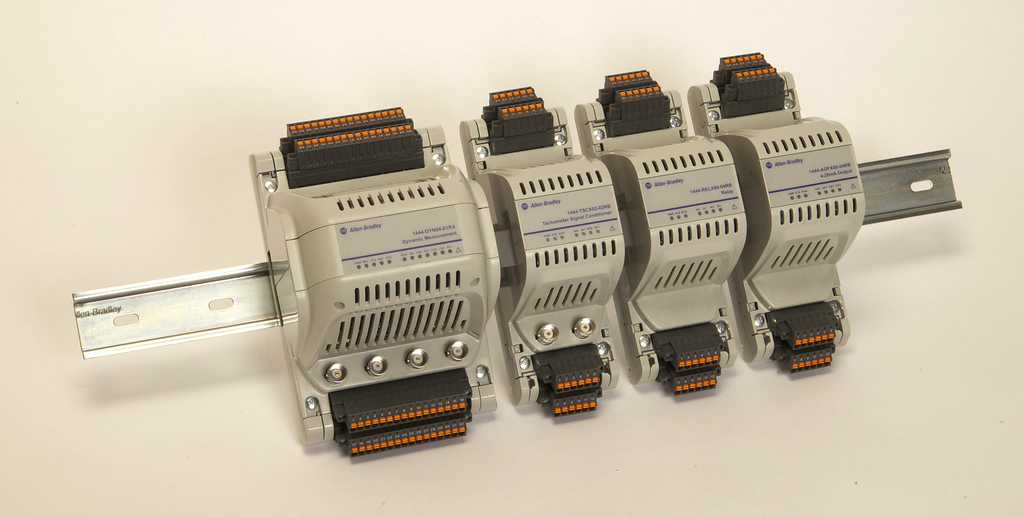
The new integrated condition-monitoring system allows manufacturers to leverage the Rockwell Automation Integrated Architecture system, rather than an isolated condition-monitoring device, to assess current equipment health, predict potential issues, and help avoid damage to critical machinery. Integration of machinery health into control architectures using a standard Ethernet TCP/IP EtherNet/IP network brings unprecedented flexibility to machine instrumentation design and operational efficiency on the manufacturing floor.
"Industrial producers need a device that performs the full scope of protection and condition monitoring, and the Dynamix 1444 monitor does that while improving the ease of use and cost of such monitoring,” said Pat Carle, product manager, Rockwell Automation. "The monitors can serve a broad range of applications because they are massively configurable.”
Primarily used as a machinery protection system for rotating and reciprocating equipment, Dynamix 1444 monitors supervise critical operating parameters in real time. They also provide operations and maintenance personnel with the information to assess current equipment health and perform predictive-maintenance planning.
To protect equipment, the Dynamix 1444 device measures and monitors a machine’s critical dynamic and position parameters, and assures appropriate actions are performed with the precision, reliability and performance required by industry and regulatory standards.
For general condition monitoring, Dynamix 1444 monitors offer unprecedented signal processing and measurement capabilities allowing users the tools necessary to detect and identify the faults and status across all classes of industrial machinery. Information can also be sent to plantwide and enterprisewide databases for storage and trending. Armed with this information, engineers can take appropriate maintenance action, such as replacing worn-out components before they fail, and protecting production processes and equipment while reducing maintenance costs.
The tight coordination between condition monitoring and the control system allows manufacturers to leverage existing investments in visualization and information solutions to improve machine builder and end user productivity, and lower total cost of ownership. For example, with Rockwell Software Studio 5000 software from Rockwell Automation, users can deploy and maintain condition-monitoring programming in the same design environment used for automation control.
Dynamix 1444 Series monitors are rated for minus 25 to 70˚C and 18 to 32V power. They are designed for use in hazardous environments and rated to marine standards for shock and vibration.
- Rockwell launches new open architecture industrial computers & thin clients
- Scalable drive solution
- Medium-voltage drive tech cuts energy consumption
- Perfect pairing to accelerate time to market for panel builders
- Rockwell launches connected worker solution
- Easing entry to smart manufacturing
- Improves machine performance
- Rockwell releases 2024 sustainability report
- Motion Application Efficiency Improved Without Sacrificing Performance
- Rockwell's ethical credentials recognised
- IO-LInk Now Included
- As Long As The Wind Blows
- CONDITION MONITORING FOR THE COMMON MAN
- Breakdown Avoided Thanks To Condition Monitoring
- "Try & Buy" Offer For Thermal Imaging Camera
- New generation condition monitoring
- Diagnostics from a distance
- Power plant protection
- Real-time monitoring
- Cost-effective protection for smaller machinery