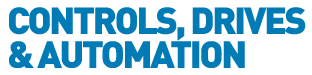
![]() |
Charlotte Stonestreet
Managing Editor |
Home> | DRIVES & MOTORS | >Soft Starters | >Getting ready for better times |
Getting ready for better times
14 January 2013
With evidence that the recession is now behind us, factory owners at last have the time to take stock of their plant and equipment to see if some TLC or maybe even a small investment is in order. Stuart Harvey of SoftStart UK, offers some pointers on what can be achieved without breaking the bank
Most manufacturing companies will have been sweating their assets for the past few years, working them hard and perhaps not being so strategic when it came to thinking about maintaining, developing and updating them – or even replacing them. This is a natural reaction to the hard times the nation has endured over recent years.
But with growth returning to the economy, people should take the opportunity to review their machinery. There is no magic money tap being turned on, but it is once again possible to undertake some first class maintenance and perhaps modernisation to improve performance without breaking the bank.
Maintenance may include replacing bearings or drive train components, checking software and sensor setting, and even mundane things like checking the lubrication. This all may sound simple, but it can be remarkably effective, and there is always the possibility that it will avert a break down that would be disruptive to production.
A very useful thing to do is to look at energy consumption. The price of energy, in just about every form, has been rising at a rate considerable above general inflation for a number of years and it is likely to continue doing so for some time yet. There are several ways to assess energy usage, but it makes sense to look first at the machines that consume most energy, measuring their actual consumption with an energy meter and comparing this to the theoretical value based on load and run time calculations. If there is a discrepancy, there may be an opportunity for long term savings.
Drives
Perhaps the most likely solution is to fit a variable speed drive or inverter to the drive motor. This can be programmed to reduce the running speed of the motor, either permanently or in response to a changeable parameter. Savings are proportional to the square or cube of the speed reduction (depending on the type of load) so can be substantial. Pay back of the cost of fitting drive is usually 12-24 months.
It should be noted that in some applications a drive is used to reduce a motor to idling speed or even stop it altogether over a major part of its duty cycle, in which case energy savings can be huge.
In other cases motors may be driving pumps or fans at full speed, producing far too much flow. Again a drive can be used to match flow to actual demand, and to vary flow as demand changes.
It is also worth mentioning soft starts here. These can reduce energy spikes during start up and major speed changes, but perhaps their greater role is to reduce the transmission of stresses through the drive train and into the machine.
In an application where there are frequent stop/starts, starting under load or the likelihood of sudden overloads, a soft start will help to reduce damaging shock loads to the system. The working life of a drive or soft start is typically 5-10 years, and it is a fair bet that considering the prevailing economic conditions since 2008, there are many installed in industry that are due for replacement sometime soon. Drive technology has moved on significantly over the last five years, so swapping out a drive for a new one should bring a range of extra benefits including renewed reliability, better performance and more features.
The same can be said of motor technology; there have been significant improvements in operating efficiency as the world has striven to reduce greenhouse gas emissions. Motors’ efficiency can decline significantly over time; a ten year old motor is likely to be very much less efficient than it was when new. Thus a new motor may pay handsome dividends in a very short time.
Further there has been a sea change in thinking. It used to be common to oversize a motor quite considerably to allow for overloads and shock loads. This did impart reliability through robustness to a machine, but at a heavy energy price, especially of the motor was running much of the time. Nowadays it is considered best practise to ‘right-size’ a motor and use an inverter to electronically give it boost capacity to ride through overloads.
Controls
If drive and motor technology have advance, then control technology has rocketed, and it is well worth considering renewing or upgrading machine control systems. PLCs (programmable logic controllers) have become very much smaller than they were, and also more powerful and adaptable. It is now possible to easily build a sophisticated SCADA (supervisory control and data acquisition) or DCS (distributed control system) using modern rack based PLCs onto which you simply mount standard control modules.
Such a system is also easily adaptable and/or extendable, and this opens up the possibility of connecting previously separate machine controls system to create a much more controllable production environment. You can then add a higher level controller – perhaps a larger PLC or a PC – to collect and analyse large amounts of real time data and thus optimise production to a level that was simply not possible just a few years ago.
In summary then, now is a good time to review machinery performance. It will almost certainly benefit from a good wash and brush up, while investing in some common sense upgrades is likely to pay dividend for many years to come.
- VSD control cabinets for hire
- Softstart achieves best Delta sales growth
- Energy efficient option
- Field Oriented Control
- No run of the mill starter
- Softstart UK & Delta Electronics in strategic partnership
- Bringing Life To The Desert
- Hazardous area system design video
- Multi-Voltage capability for pump test station