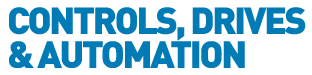
![]() |
Charlotte Stonestreet
Managing Editor |
Home> | POWER TRANSMISSION | >Electric Motors | >Roller table motors for harsh applications |
Home> | DRIVES & MOTORS | >Roller Drives | >Roller table motors for harsh applications |
Editor's Pick
Roller table motors for harsh applications
17 June 2014
According to Regal Beloit, roller tables used in modern steel mills tend to use individually driven rollers rather than a single group drive such as a chain or belt and require special motors with a high dynamic constant, plus a robust overall design to withstand the extreme heat and dirt of a steel mill.
Such motors are used throughout the rolling mill on general conveying duties, but on the reversing mill and associated approach tables, the operating duties are extreme with constant stop/starts and instant reversal of directions.
In operation the most important issue is the rate of acceleration and deceleration of the stock. This determines the rating of the motors, which is usually expressed in terms of starting torque.
It is important to note that the starting torque requirement depends on the type of stock being rolled. Slab stock is rolled one piece at a time and the starting torque relates to its weight. If the motors are overpowered, the rollers could skid over the surface of the slab, causing imperfections to the surface.
However, rod and billet stock is often rolled several pieces at a time, so there is potential for the pieces to become jammed against one another or against the mill sides. In these cases the motors have to have sufficient torque to reverse and drive through to clear jams. However, the availability of this 'extra' torque means skidding may occur, causing damage to the stock's surface, which then has to be rolled out with additional passes through the mill.
Theoretical maximum and minimum torques for each application are relatively easy to calculate, based on: roller diameter and length; roller spacing; size, type and weight of stock; acceleration time; and maximum velocity. The skidding torque can also be calculated using the same techniques, and lies between maximum and minimum.
For slab rolling applications, motors whose torque characteristics lie between minimum and skidding torques should be selected. For billets and rod stock, motors that lie between skidding and maximum torque are ideal. Motors that exceed the maximum torque will be overly prone to skidding in use and also will consume excess power, compared to optimally sized motors.
It is a characteristic of roller mills, particularly those working with billet and rod stock, that jams and blockages occur. Because of the proximity of literally tonnes of very very hot metal, these cannot be cleared by manual intervention, but only by driving and reversal of the rollers. In such an event it is likely that one or more of the rollers will be in a stall condition for an extended time, so they have to be able to withstand the electrical stress this creates. There are international standards that cover this situation: for straightforward applications, they generally recommend a capacity to withstand stall conditions for up to three minutes; for more demanding situations, this figure can rise to 15 minutes or more.
Another key characteristic of roller table motors is the ability to dissipate heat. This relates to the load, acceleration and frequency of starts, plus – importantly – a factor to account for the thermal consequences of stalls. Within the industry, this is referred to as the 'B value' and is always quoted on technical specifications because of its fundamental importance.
Design criteria
- When designing or specifying a roller table motor, essential criteria include:
- Speed/torque characteristics to match the specific application
- Lowest possible rotor inertia
- Very high mechanical rigidity to withstand the constant reversals
- Robust mechanical design to withstand high loads, shock loads, rapid accelerations and reversals
- Large bearings and high-temperature lubrication
- Robust electrical design to withstand prolonged stall conditions
- Insulation to Class F or H to cope with the high temperatures within the motor
- Recognition of the high ambient temperature and suitable derating of motor performance
- Duty cycle is likely to be 24x7 over many years, with minimal maintenance
Additionally, the motors will need to be totally enclosed for the protection of operators and consideration will also need to be given to cooling. While forced draught cooling is effective thermally, it can have the drawback of stirring up dust and dirt, so natural cooling through fins or heat sinks may be a better solution.
Increasingly, there is also an emphasis on energy efficiency, as a set of table roller motors will consume a considerable amount of power. The basis of this is often the use of a cast aluminium rotor and careful design of other elements of the electrical engineering.
For many years AC motors have been preferred for roller table applications because they require less maintenance than DC motors and the use of inverter drives is well-proven in the field.
In conclusion, we can say that roller table motors have a very arduous duty cycle in extremely harsh conditions. Because of the cost of downtime, they must be so robust that they can stand up to almost anything and keep on performing. A good roller table motor will pay for itself through years of reliable performance.
- EXTENSIVE STOCK & RAPID DELIVERY
- Explaining the different types of AC electric motor
- Surpass European Efficiency Levels
- Drip-proof motors
- Comparing motor efficiencies
- Are inverter-rated motors essential: YES or NO?
- When two-speed motors are the best solution
- Stainless Motors For Washdown Environments
- Washdown Motors
- For Remote Or Outdoor use