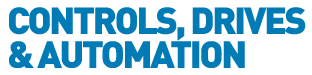
![]() |
Charlotte Stonestreet
Managing Editor |
Editor's Pick
Clear benefits of standardised control
18 June 2014
Siemens Industry and solution partner, ACSI, have worked together to help leading glass manufacturer, Beatson Clark create an integrated controls system and deliver real benefit for the business
The new solution will drive a standardised approach to support a centralised system control strategy, lay the foundation for future upgrades on site and provide a flexible platform that can allow future add on tools – for instance in crucial areas such as energy monitoring.
Beatson Clark, based in Rotherham, specialises in providing glass packaging solutions for niche brands in the pharmaceutical, food and beverage markets across the globe. With production of more than 500 million units per annum, the two busy furnaces that sit at the heart of the Beatson Clark operation are key to the success of its market position.
Ageing legacy control system
The furnaces are heavily used and are expected to operate for up to 15 years following commission and a critical factor is the requirement to make them as operationally efficient as possible. With one of the main furnaces at the Rotherham manufacturing facility coming towards the end of its current lifespan, the management took the opportunity to examine how best to improve what was also an ageing legacy control system.
Martin Coley from Siemens Industry explains: "The site did not have an integrated control system and the rebuild of the furnace in question presented an ideal opportunity for an upgrade of the control architecture.
"Previously the site had been subject to ‘islands of automation’ that offered little or no coherent visibility of the plant-wide operation. The legacy system was based on various components and elements supplied from a variety of sources all using different programming tools and techniques.”
After discussions between Beatson Clark management, ACSI and Siemens, the chosen solution was to be based on Simatic PCS7 process control. This provides a starting point for the site to establish a more integrated controls strategy to support the future operation of the plant going forward. In particular, it will help when further additional furnace upgrades are to take place, as well as helping to integrate the need for a required energy monitoring platform. All these objectives could be met through PCS7 implementation.
Martin Coley continues: "The PCS7 solution was recommended because of its ‘out of the box’ functionality and the adoption of a standardised software approach using the standard PCS7 library functions. This will create the integrated control the site was seeking with 24/7 high availability. It also features easy functionality additions such as the PowerRate tool, which enables energy monitoring and reporting to be seamlessly added as part of the overall control platform.”
Greater visibility
Dave Douglas, Operations Director of ACSI, commented: "The new system now allows for far greater visibility of the control functionality and has set the basis for a scalable solution that supports future plant expansion."
"An important benefit also made possible by the standardisation strategy on site is the positive impact it can have on controlling the lifecycle costs associated with the system.”
Such has been the initial success of the migration to a standardised PCS7 solution that further work will ensure the additional furnace on site will also be upgraded and integrated into the site-wide centralised control system in due course. In addition, the initial use of the PowerRate energy monitoring and reporting tool is providing invaluable feedback to the management team to gauge and more effectively manage, the site’s energy consumption and implement energy saving initiatives. This is a very important aspect for a high energy user at a time of escalating costs.
Key Points
- Legacy system of various components and elements supplied from variety of sources, all using different programming tools and techniques
- New integrated system drives a standardised approach to support a centralised control strategy going forward
- PCS7 solution recommended because of its ‘out of the box’ functionality and standard library functions
- Continuous pharmaceutical manufacturing conference
- Siemens collaborates with HVM Catapults
- Siemens & Spire in tech partnership
- AI-powered maintenance capability
- Siemens & Chronicle join forces to provide industrial monitoring for energy industry
- Narrow IO modules
- Business leaders outline digital roadmap for industry
- Siemens & OCR launch UK engineering skills partnership
- Entry-level rack mount PC
- Battery partnership
- Reduce Fault Times
- Vision Control Makes The Cut
- MULTIPLE PROTOCOL CONVERSION
- MAKE SURE YOU CATCH THE RIGHT BUS
- Smarter, Faster & More Compact Robot Controller
- What Does Windows 8 Mean For Test & Measurement?
- Thyristor Stack Controllers
- Easy To Automate
- Understanding Thyristor Control
- Introduction to embedded control and monitoring webcast