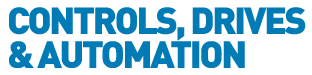
![]() |
Charlotte Stonestreet
Managing Editor |
Home> | MACHINE BUILDING & ENGINEERING | >CAD/CAE | >Embedded electrical systems development simplified |
Embedded electrical systems development simplified
24 June 2014
According to SOLIDWORKS reseller, NT CADCAM, the new SOLIDWORKS Electrical software solution is set to transform the working lives of those who design, operate and maintain complex PLCs
A Programmable Logic Controller, or PLC, is a digital computer widely used for the automation of electromechanical processes in many industries and machines, such as the control of machinery on factory assembly lines. A PLC is designed to handle multiple inputs and outputs in real-time. Any mistakes will result in unintended – and undesirable – outcomes. With each PLC controlling hundreds or even thousands of outputs, any errors could yield catastrophic results.
The biggest weakness in the operation and maintenance of any PLC lies in the design of its schematic. Schematics have traditionally been designed by humans, by hand. It’s a meticulous task, which is not only time-consuming but also carries with it the risk of human error. Moreover, each time a modification is made to a PLC, for example rewiring by an electrical engineer, the schematic needs updating, again by hand.
SOLIDWORKS Electrical’s schematic design capability simplifies the development of electrical systems embedded in PLCs, with specialist tools for planning electrical systems. With an integrated database of thousands of symbols and over 500K manufacturing parts for use in the design of schematics, development time is reduced as users can copy and paste common circuit segments either within a schematic or across multiple projects, streamlining the design process.
This automation reduces the time invested by the developer, removes the risk of human error and improves efficiency, ultimately resulting in cost savings for the company.
Ron Chappell, lead technical consultant for NT CADCAM has first-hand experience of manually designed schematics and puts the perils into simple terms.
"Having a solid schematic for a PLC is critical for efficiency. If your schematic doesn’t make sense to begin with, it’s going to take you a long time to decipher it and make any sense of it," says Chappell. "Moreover, when the time comes for you to share the schematic with others working with the PLC, if the schematic’s not clear from the outset, then you’re going to have to invest many hours explaining it, and that explanation is wide open to misinterpretation."
With SOLIDWORKS Electrical, you can easily generate drawings, wire lists and ‘from-to’ lists, so that those engaging with the PLC can easily work together as a team. This is particularly useful if modifications are required. If rewiring needs to take place, for example, then a comprehensive schematic can easily be delivered to the electrical engineer. The resultant changes across the PLC’s connections are automated within the software too. If multiple connections are rewired, for example, these are automatically renumbered and a new version of the schematic can be saved. When combined with SOLIDWORKS 3D design software, changes in both the schematic and the 3D model can be saved simultaneously.
Quicker process
Calorex Heat Pumps, a leading manufacturer of heat pumps and dehumidifiers, has recently adopted SOLIDWORKS Electrical through NT CADCAM. Calorex’s core heat pump business is in the design of swimming pool heaters and swimming pool environmental control. It also manufactures heat pumps to recover energy from the air to heat water in commercial buildings.
"My core role within the company is looking at the design and drawings for the mechanical packaging of our products," says Kevin Wood, design draughtsman for Calorex. "In taking the product from proposed concept through to full manufacturing and assembly drawings, schematics are central to my work."
Calorex currently has a three-step approach to its electrics:
- A schematic circuit diagram is drawn up by an electrical engineer
- A wiring diagram, showing point to point wiring information is drawn up by a draughtsman
- A loom diagram is also drawn up by a draughtsman
"This is a time-consuming process involving a lot of cross-checking and three finished documents, which are open to errors," says Wood. "By adopting SOLIDWORKS Electrical we hope to speed up the process and reduce the number of errors that get through. We also believe it will provide a lot more up front control to our electrical engineer (not relying on the draughtsman’s interpretation of his requirements) and allow for a more flexible approach to the electrical design of the product, as changes to the circuit or component positions will update wiring information concurrently."
Key Points
- The biggest weakness in the operation and maintenance of any PLC lies in the design of its schematic
- SOLIDWORKS Electrical’s schematic design capability simplifies the development of electrical systems embedded in PLCs
- Development time is reduced as users can copy and paste common circuit segments either within a schematic or across multiple projects
- MODELLING EXPERTISE
- Free 3D CAD Models
- SWITCH TO THE POWER OF CAE
- Efficiently drive your electrical projects with SEE Electrical V7R1
- Free To Download Software
- SEE Electrical
- Eplan is Siemens PLM Solution Partner
- The future’s bright, the future’s CAE
- Upgrade to CAE
- Circuit simulation & design software