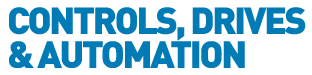
![]() |
Charlotte Stonestreet
Managing Editor |
Do PLe applications need two interlocks?
23 June 2014
Rob Lewis, managing director at Fortress Interlocks, looks at interlock redundancy
There is a lot of interest in whether redundancy is required when it comes to interlock actuators. This debate has been on-going for many years but really gained momentum in 2012 by the inclusion of a note in table D8 in 13849-2-2012:
‘For PLe a fault exclusion for mechanical (e.g. the mechanical link between actuator and contact element) and electrical aspects is not allowed. In this case redundancy is necessary’
Now that EN ISO 14119 (The Interlock standard) has been published it adds to the debate with the following two paragraphs in section 8 with relation to ‘Assessments of faults’ and ‘Fault Exclusions’.
‘Where an interlock system requires PLr e……... In order to achieve this it is normally not justifiable to exclude faults, such as broken actuators.’
‘There should be a proper selection of the device ensuring that the holding force (Fzh – see 5.7.4) of the guard locking device is sufficient…….. In this case the use of fault exclusion for breakage of the locking element does not necessarily limit the PL or SIL for the guard locking function.’
So what exactly does this all mean?
Clearly there is variability in what the standards say about fault exclusions, with statements ranging from ‘not allowed’ through ‘normally not justifiable’ to ‘not necessarily limit’, however the common thread is: Actuators breaking must be considered very carefully for PLe applications.
With a typical interlock this is fully understandable, as it is not uncommon for typical actuators to break leaving the interlock in a fail-to-danger condition.
When designing the Fortress amGard Pro Heads and Actuators the objective was to create an indestructible solution to meet the interlock standard. With all loadbearing components manufactured from over-dimensioned cast stainless steel, Fortress has constructed an actuator that absorbs more than 50 times the energy of a typical actuator and a head that remains attached beyond 4000kg of load. The end result is a unit with strength beyond that of the hinges, fittings and the guarding itself.
It is the over-dimensioning, rigorous testing and data from 3 billion hours of in-service use that gives Fortress and TÜV SÜD the evidence to state the amGard Pro as a PLe interlock without the use of a secondary interlock
Conclusion
For PLe applications careful consideration must be given to the actuator. If a normal pressed actuator is to be used then, in all but the lightest duty applications, a secondary interlock should be used. Alternatively an interlock which incorporates an actuator and a separate non-contact sensor could be used. However a Fortress amGard Pro interlock, with its actuator that is stronger than the rest of the guarding, provides the simplest solution to achieving a PLe rating.
Machine Safety Alliance
Safety Interlocking company Fortress Interlocks is a member of the Machine Safety Alliance with Festo, Pilz Automation Technology, Troax, UK Engineering, and Werma.
The Machine Safety Alliance aims to share its collective knowledge and expertise to help machine builders and users make sense of safety and safeguard their productivity. For more information, please visit the website at www.machinery-safety-alliance.co.uk or see www.fortressinterlocks.com
Key Points
- The debate on whether redundancy is required when it comes to interlock actuators gained momentum in 2012 with the inclusion of a note in table D8 in 13849-2-2012
- There is variability in what the standards say about fault exclusions, but the common thread is: Actuators breaking must be considered very carefully for PLe applications
- When designing the Fortress amGard Pro Heads and Actuators the objective was to create an indestructible solution to meet the interlock standard
- No related articles listed