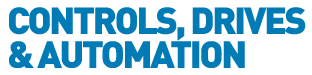
![]() |
Charlotte Stonestreet
Managing Editor |
Home> | AUTOMATION | >Machinery Safety | >Safety in control |
Editor's Pick
Safety in control
21 October 2014
The Machinery Directive stipulates that machines should not pose any danger, however, as no machine can realistically be 100% safe, the directive requires measures to be put in place to reduce residual risks to a tolerable level. Stuart Greenwood, product marketing manager for industrial control and automation at Eaton, looks at how this requirement affects control systems.
For any commodity to be legally supplied in the EU, it must comply with relevant directives and, in most cases carry the CE marking. In the case of machines, which are broadly defined as "an assembly… of linked parts… which are joined together for a specific application”, a key directive to which it must comply is the Machinery Directive 2006/42/EC. The directive came into force on 29th December 2009 and applies to all machinery supplied after that date.
Machine suppliers in the UK are legally obliged to show that they have met the requirements of these regulations by showing that the design and construction of their machines complies with relevant standards. In the case of machines, one of the most fundamental is EN ISO 121000, ‘Safety of Machinery – Basic concepts, general principles for design’.
This standard dictates that all protective measures used to remove hazards or reduce risk must be implemented in a fixed order. Firstly, eliminate or reduce risk by design measures during the development of the machine. Secondly, if the risk still remains, reduce this by the use of protective measures. Finally, when all possibilities for risk reduction have been exhausted, provide warning of the hazards associated with any residual risk.
The design of the machine control system can be influenced by the outcome of any of these stages, but it is most likely in the second stage. This is because the control system itself is often designed to provide specific risk-reduction functions.
The sections that do this are officially designated as ‘safety-related parts of control systems’ or SRP/CS. They can consist of hardware or software and can be separate or integrated elements of the machine control system. The standards for SRP/CS are IEC 62061, which applies only to electrical and electronic element, and EN ISO 13849-1/-2, which covers these and also others, such as hydraulic and pneumatic types.
The two standards have different ways of determining and designating safety categories. ISO 13849 uses performance levels PL a to e which loosely correspond to suitability for applications involving increasing levels of risk. IEC 62061, uses safety integrity levels SIL 1, 2 and 3.
Approved products
When it comes to implementing control systems with safety-related functionality, control equipment suppliers have made designer’s task easier by offering specially designed and approved SRP/CS products. These fall into two categories: logic units, with a specific safety function or a small range of user-selectable safety functions, and programmable safety relays.
Products in the first category, including the Eaton ESR5 range of safety relays, are an inexpensive compact and easy to use option where only a small number of safety functions are needed. They are suitable for simple applications, such as providing emergency stop functionality.
For larger and/or more complex applications, programmable safety relays are a versatile and often cost-effective choice, particularly as the latest types, like Eaton’s easySafety range, combine standard control functions and safety functions in one device. Though they are slightly bigger than safety-only relays, these devices can replace several individual relays, therefore, saving space in the control panel.
Programmable devices do need more setting up than dedicated-function relays, but in the best types this task is simplified using built-in safety function blocks, which users simply select to match the requirements of the application. Typical safety function blocks cover guard monitoring, emergency stop, zero-speed and over-speed detection, and monitoring for electro-sensitive protection equipment such as light curtains.
This article has only scratched the surface of the important subject of control systems and safety. More help and guidance is available from Eaton’s free machine safety manual, which can be downloaded from http://bit.ly/EatonSafetyManual.
Key Points
- Machine suppliers in the UK are legally obliged to show that they have met the requirements of the Machinery Directive 2006/42/EC
- When it comes to implementing control systems with safety-related functionality, control equipment suppliers offer specially designed and approved SRP/CS products
- For larger and/or more complex applications, programmable safety relays can provide a versatile and cost-effective choice
- OVERVOLTAGE PROTECTION
- MAKING THE MOST OF SAFETY BENEFITS
- EXTEND MOBILE INTO MAINTENANCE
- Electronic Locking
- Machinery Safety Roadshow
- Machinery Safety UCPD Courses
- GUIDE TO EX NA INSTRUMENTATION INSTALLATION
- Safety Relays Meet SIL3 Requirements
- IECEx Approval
- ARE YOUR SAFEGUARDS AS SAFE AS YOU THINK?