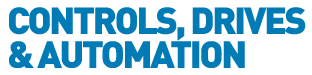
![]() |
Charlotte Stonestreet
Managing Editor |
Home> | DRIVES & MOTORS | >Electric Motors | >Motor efficiency – the other options |
Home> | DRIVES & MOTORS | >Variable Speed Drives | >Motor efficiency – the other options |
Motor efficiency – the other options
20 October 2015
The ErP Directive - the second stage of the EU motor efficiency regulations - took effect at the start of this year. Until now, industry has mainly focused on electric motors, but that no longer enough, says Eaton UK's Stuart Greenwood,
Product selection is only part of the answer to meet the requirements of the ErP directive. It is also necessary to analyse entire processes and systems in order to comply with the required minimum efficiency levels. To optimise the efficiency of machines and systems, the switchgear also has to be taken into account.
In the UK, electric motors account for almost two-thirds of industrial electricity consumption. However, according to GAMBICA, if variable speed control were added to the motors of relevant applications which are not currently using it, savings of around 25,000GWh could be achieved, roughly the output of 6000 medium-sized wind turbines.
The EU Energy-Related Products (ErP) Directive for motors 640/2009/EC prescribes minimum efficiency classes for three-phase low-voltage induction motors. The first stage of the regulation, which stipulates efficiency class IE2 as the minimum for new motors, took effect in mid-2011. As of January 2015, machinery and system manufacturers using new motors with a rated output power between 7.5 and 375kW were required to achieve at least efficiency class IE3. IE2 motors may be used as an alternative, but only in combination with a variable speed control. From 1 January 2017 this stipulation will also apply to motors with rated output power of 750W or more.
System analysis
Machine manufacturers are faced with the challenge of having to redesign their systems and that are not yet equipped with IE3 motors or variable speed drives. However, simply replacing IE2 motors with IE3 motors is not enough to make machines and systems more energy efficient. To ensure safe and reliable operation, the entire drive system must be analysed and the effects of design changes on the application must be considered.
To improve the energy efficiency of electric motors, manufacturers have altered the designs of their products. These alterations also affect the electrical profile, resulting in higher starting currents for high-efficiency motors. This situation also impacts on protection devices and switchgear. Possible consequences include unwanted shutdown due to circuit breaker tripping from higher starting currents or contact bounce due to higher current levels, leading to contact burning and reduced lifetime or even, in the worst case, contact welding.
Eaton has studied the behaviour of motor protection devices in detail in practical tests. Its DIL series of contactors and the PKZ and PKE series of motor protection circuit breakers were checked for compatibility with IE3 motors from well-known manufacturers and improved as necessary. The results showed that the values stated in the currently applicable standard for motor starters (EN 60947-4-1) are not valid in practice for IE3 motors. Work on a draft amendment to update the standard is in progress. Eaton’s current "IE3-ready" product families ensure reliable operation of both IE2 and IE3 motors.
Though variable speed control is usually necessary to reduce losses, it may be functional overkill for many simple applications. One alternative is motor starters, but although they have are easy to use, their functionality is limited. For applications involving fixed speeds or low operating cycles, motor starters in combination with IE3 motors are still the most energy-efficient approach. However, if the aim is to improve the energy efficiency of existing systems that run at constant speed but less than full rated load, there is now a third option in the form of variable speed starters.
Eaton's PowerXL DE1 variable speed starters bridge the gap between motor starters and variable speed drives. They are as easy to use and as reliable as conventional motor starters, with the added advantage of variable speed control. Additionally they can be put into service immediately. They support user configuration, using a plug-in module that allows the default values of key parameters to be individually adjusted with a screwdriver, with no need for a keypad, software or a manual.
Key Points
- Simply replacing IE2 motors with IE3 motors is not enough to make machines and systems more energy efficient
- Eason's DIL contactors and the PKZ and PKE motor protection circuit breakers were checked for compatibility with IE3 motors from well-known manufacturers
- The results showed that the values stated in the currently applicable standard for motor starters (EN 60947-4-1) are not valid in practice for IE3 motors
- Direct valve integration
- Eaton invests in training facility
- Long range sensors
- White paper helps machine builders save money
- Choosing the right hydraulic pump
- Data transparency - the key to optimised operation
- Control system upgrade
- Changes to North American National Electrical Code
- Optimum safety & reliability
- Now with SmartWire-DT
- JOINT WIND ENERGY GENERATORS VENTURE
- PUMPED UP PERFORMANCE
- SOFT STARTER OR VARIABLE SPEED DRIVE?
- Jeans With Less Energy
- Enhanced to Withstand Tough Environments
- Washdown Motors
- Savings From Improved Torque Ratio & Efficiency
- Engineering Talent Search
- Cooling System & Frame Optimised
- Sustainable Motors