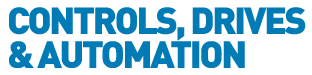
![]() |
Charlotte Stonestreet
Managing Editor |
Linking intelligent assets to optimise operations
06 January 2015
When someone mentions California, what is the first thing that springs to mind? Hollywood? Disneyland? Industrial automation? OK, maybe not industrial automation, but for a week in November it was definitely top of the agenda in the Golden State when Rockwell's Automation Fair took over the Anaheim Convention Center. Charlotte Stonestreet reports
Central to Rockwell's message throughout the event was the concept of 'The Connected Enterprise'. With ever increasing pressure on manufacturers, machine builders and industrial operators in terms of cost, energy and time to market, Rockwell asserts that the sector needs to work smarter and take advantage of the potential to increase connectivity across enterprises. Essential to this approach is the much touted Internet of Things, whereby almost every object can use embedded technology to gather and transmit information.
"We are here to share our vision, expertise and the most contemporary products, software services and solutions for industrial automation. And we're here to learn from our customers what is driving their business today and in the future," said CEO Keith Nosbusch in his opening Automation Perspectives presentation.
Value drivers
Nosbusch highlighted four main high level value drivers that Rockwell has identified as being important across all the sectors it serves: Faster time to market; Lower total cost of ownership; improved asset utilisation; and Enterprise risk management. According to Nosbusch, everything Rockwell does is focused on helping its customers realise tangible benefits in one or more of these areas, and this is achieved through The Connected Enterprise.
"The Connected Enterprise is focussed on rapid value creation through the tighter integration of the industrial assets and the rest of the enterprise value chain," said Nosbusch. "That tighter integration requires secure networks, ease of data collection and management, and contextualising the data to turn it into information that that can be shared; from the plant floor across the enterprise and from suppliers to customers."
With galloping developments in integrated control and information, along with the Internet of Things trend, Rockwell believes that it is at an inflection point for the Connected Enterprise and the realisation of it for customers, however, this is not without its challenges. Central to the success of this approach is the convergence of IT (Information Technology, ie. ERP, CRM, quality, accounts, supply chain) and OT (Operational Technology, ie. machines, controllers, sensors, actuators), and this raises all sorts of potential issues. Traditionally, these two areas of a business have been completely separate, with different technologies and priorities.
"Critical to the OT side is realtime data that drives control and safety. Realime data is typically collected and acted upon in milliseconds or microseconds, frankly, reliable and repeatable processes for control, safety and security are paramount. Many operations need to run 24/7 safely and securely; industrial processes cannot tolerate shutdowns for software updates," said Nosbusch.
"On the other side, IT, transactional data and business systems form the backbone, with their own priorities on what is mission critical. Transactions will take several seconds or even minutes, and the IT side is more tolerant of software patches and updates that may sometimes shutdown a computer or two."
Addressing the challenges of true convergence in these areas, Nosbusch acknowledged that in the past solutions had tended to be inflexible, expensive and unable to scale easily – issues that Rockwell has been working on, along with partners, to bridge the gap. The result is a robust, IP-based, network infrastructure for industrial automation, with a broad range of hardware and software products, solutions and services jointly developed with IT giant, Cisco, Rockwell's strategic partner in this area.
According to Nosbusch, this flatter and more open approach to industrial networking has resulted in a level of flexibility not possible with the previous generations of proprietary industrial technology, and it forms the foundation of IT/OT convergence. However, he also acknowledged that up to this point only a few of the most progressive manufacturers have managed to truly bridge to IT/OT divide.
Great potential
There's no doubt that the opportunities in this area are huge, with figures putting the potential economic value of the Internet of Everything at a staggering $19 trillion. However, a recent survey by Industry Week also shows that currently less than 14% of manufacturers have connected their machines to the enterprise network. Another significant figure, from Kapersky, is that 21% of manufacturers experienced a loss of IP last year due to a breach in security. Rockwell is working with Cisco and customers to provide a reference architecture and help implement layered end-to-end security solutions. Nosbusch also pointed out that big data collected from operations could be used to help make faster, more informed business decision, rapidly drive value and reduce downtime.
"Modern technologies are helping us connect smart assets to the rest of the enterprise. The foundation is ever-smarter industrial assets coupled through contemporary control and information capabilities via a secure IP-based network infrastructure," said Nosbusch. "The IP-based infrastructure is enhanced by the industrial environments by the power of the Common Industrial Protocol, or CIP, delivering realtime information in a reliable, safe and secure manner. The data from these smart assets will be processed aggregated and analysed with scalable computing that is delivered at the point of most value, whether that is directly within a controller, or the edge, or in the cloud."
Rockwell delivers The Connected Enterprise and drives innovation through three core platforms: Integrated architecture; intelligent motor control; and solutions and services. These three core platforms are complemented and extended by Rockwell's partner network.
While all integrated control and information applications start with smart assets, Nosbusch encouraged his audience to think of two types of application that are in broad terms are different in sophistication in computing and communications. The first involves smart assets distributed in the field, often in remote locations. In such cases, services such as predictive maintenance are now practical through the power of integrated control and information technologies.
"Remote expert models allow the provision of these services in a much more cost effective and timely manner, versus a model which one required an expert to get on a plane and travel half way around the world," said Nosbusch. "In many heavy industries that is particularly attractive as equipment is often based in inhospitable sites."
The same is true for natural resource industries, such as oil & gas and mining, where assets need to be placed close to the natural resource. While the past is has been expensive and problematic to connect to these assets, today's technologies such as cloud-based computing mean it is now much more cost effective and practical to remotely manage them. However, Nosbusch also points out that it is not desirable to cut out human intervention altogether.
"There is much talk these days about big data analytics automatically extracting insights from complex patterns in Terabyes of data. Yet our experience in the industrial world is that most remote assets applications involve some form of man in the loop; an expert who can blend timely information access with years of experience to create real-world insights and decisions for what actions to take," he said.
Plant-wide
The second type of application Nosbusch referred to was plant-wide; Smart assets in plants typically have greater computing and connectivity than distributed assets. "This enhances the ability to compare and optimise operational performance across multiple machines, lines, plant sites, and across entire supply chains."
Smart assets in a plant generate a significant amount of data; contextualisation and analytics provides actionable information such as prognostics, multi-plant comparisons and process optimisation. This, said Nosbusch, will significantly improve productivity and global competitiveness of the plant.
Perhaps one of the best endorsements of The Connected Enterprise is the fact that Rockwell uses it itself. "Rockwell Automation not only believes in the vision of the connected Enterprise for our customers, we believe in it for ourselves. Over the past several years we applied the integrated conrol and information portfolio to transform our own manufacturing and supply chain operations in support of our growth and performance strategy and to meet the requirements of customers around the globe," said Nosbusch. "The results are dramatically higher levels of productivity, quality and customer satisfaction."
- MANUFACTURING AUTOMATION EVENT
- Collaboration key to reduced cyber risk
- Wiring & Enclosure Size Cut
- PlantPAx 5.0 offers improved productivity and reduced risk
- Collaborative offering to drive digital transformation
- Taking on the challenge
- Stay ahead of the curve with Rockwell Automation's CUBIC modular enclosures
- Flexible relay solution simplifies safety implementation
- Simplify machine safety systems
- Rockwell acquires ESC Services
- No related articles listed