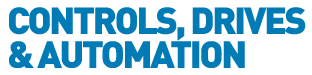
![]() |
Charlotte Stonestreet
Managing Editor |
Precision rack and pinion drives – redesigned
13 March 2015
The solution for maximum power density and powerful dynamics.
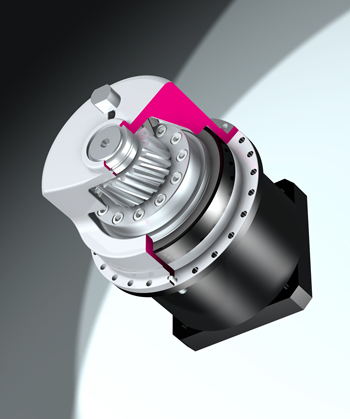
In the past rack and pinion drives were generally developed from a planetary gear unit with a gearwheel fitted to the output shaft and the matching gear rack. But the overhung load on the gear unit from the rack and pinion combination is then so high that it actually determines the dimensioning. Utilisation of the gear unit torque can normally only be in the 40 – 60 % range.
STOBER wanted to overcome this disproportionality of the resources used and developed a new concept for a super compact and highly efficient rack and pinion drive jointly with ATLANTA, the premier manufacturer of gear racks.
The most immediately striking feature of the new HighForce ZTRS-PH(A) rack and pinion drive is the integral output bearing housing, a highly stiff supporting assembly for the rack pinion which relieves the load on the flange-mounted planetary gear unit bearings. The reduced tilting moment of this construction makes it possible to base the drive design on the torque actually required and on the feed force.
As a rule this means that the gear unit can be a size smaller than normally used in the past. Due to the comparatively small pinions, a higher output speed is necessary to obtain the required feed rate. Which means that the gear ratio is lower and in many cases a single-stage planetary gear unit can be used instead of a two-stage.
This gives the outstanding power density that should encourage many designers to use redesigned rack and pinion drives. The flange-mounted planetary gear unit offers a choice between the helical PH and PHA versions.
Improved linear stiffness has not been forgotten in the new design, because the pinions do not now have to be flange-mounted directly on the gear flange shaft's bolt circle. The new mounting system makes it possible to use rack pinions with a very small number of pinion teeth, which increases linear stiffness by up to 100%.
Although the reduction in size was of central importance, other factors were also considered. Apart from the linear stiffness, the linear backlash was also improved through a 40% reduction. The pinion concentricity is adjusted to ≤ 0.01 mm.
The wide variety of gear ratios and pinion teeth numbers allows optimised adaptation of the inertia. Last but not least, there is the optional pinion lubrication with felt pinions which is integrated in the cast output bearing housing for manual operation or connection to a central lubrication system.
The HighForce ZTRS-PH(A) rack and pinion drive is available as of now in sizes 7, 8 and 9, modules 2 to 6 and gearing quality 5.
Caption
The integral supporting bearing reduces the tilting moment, making over-dimensioned drives unnecessary in the future.
- Permanent magnet servo motors provide energy efficient solution
- Motor removal on the vertical axis
- Widening the scope of rack-and-pinion
- Compact drives for depowdering system
- Drive Design Can Be Based On Torque Required
- Unwind, wind and rewind with precision
- Energy-saving modular drive
- Right-angle servo gearbox
- Digital shift control
- More processing power
- No related articles listed