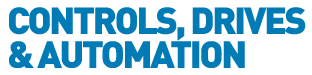
![]() |
Charlotte Stonestreet
Managing Editor |
Home> | Guides | >MAD Guide | >Vision marches on |
Home> | AUTOMATION | >Vision Systems | >Vision marches on |
Industry Associations
Vision marches on
20 November 2015
Machine vision is a fast-moving environment, where developments in processing power, camera sensors (especially CMOS sensors), illumination, optics, software capabilities and image data handling standards constantly push back the boundaries of what is achievable
Cameras with higher resolution, faster operation and smaller physical size are linked with ever more powerful processing systems to enable more complex inspections to be carried out or give better performance for existing applications. Perhaps almost as important is the availability of the skills to best make use of these developments. Fortunately many specialist vision systems integrators have emerged with the particular skills needed to deal with challenging applications, especially the integration of vision systems into existing production lines.
Such integrators often operate in specific industries and have a good understanding of any industry-specific requirements and standards that need to be met. They can be of great benefit where the installation set up is complex, or a complete turnkey solution including product reconciliation, rejection and handling is required. Nevertheless, whether a vision project is handled ‘in house’ or by a systems integrator, there are many benefits to end-users arising from the most recent developments in vision technology.
Camera developments
Probably the most significant development in 2015 was the announcement that Sony, the largest manufacturer of CCD image sensors, will discontinue production of these in 2017, with final deliveries in 2020. Whilst this is not the death knell for CCD-based cameras as there are other CCD sensor manufacturers out there, it has served to accelerate the move by most camera manufacturers towards using CMOS sensors.
Interestingly, whilst CMOS sensors have traditionally struggled to match the image quality of their CCD counterparts, some of those launched in 2015 have surpassed the equivalent CCDs in terms of noise and dynamic range. With their ability to support higher frame rates and traditionally lower costs, this is leading to higher speed cameras with higher resolution. The overall benefit for users is the ability to image smaller details at higher speed at generally lower price points.
Data transfer standards
Higher image resolution and higher frame rates generate higher quantities of image data, which needs to be transferred from the camera to the processing computer. There are a number of vision-specific data transfer standards. The three prime considerations are data transfer rate, the distance over which the data can be transmitted and cost. The GigE Vision standard, first announced in 2006, has for some time been the most popular, primarily due to its reasonably fast data transfer rates of 115 Mbyte/s over distances of up to 100 metres using standard Ethernet connectivity.
Other standards are available which offer higher data transfer rates but over shorter distances. The newest of these is USB3 Vision which utilises the USB 3.0 consumer interface with data transfer rates of around 350 MBytes/s over 10 metres (50 metres using fibre optic cable). This capability, combined with the inherent low cost of the cameras and the ever increasing availability of USB3 interfaces on PCs has seen the use of USB3 technology gain traction in 2015, with some users upgrading from USB 2.0 as well as the emergence of some completely new application areas, since USB3 offers a cost-effective ‘plug’n play solution, especially for single camera applications.
The adoption of a data transmission standard generally takes several years, especially for OEM system builders who only revisit a design maybe once every 5 years, however the increasing availability of USB3 cameras is a strong indication of growing demand, and is likely to increase in popularity in vision applications where high resolution and frame rates are required but the better control functionality provided by GigE Vision and other interfaces is not so important.
Big data and Industrie 4.0
Automation is key to improving efficiency in manufacturing industry and the automation of manufacturing processes is being revolutionised with the emergence of INDUSTRIE 4.0, Big Data and the Industrial Internet of Things (IIoT). According to IBM, ‘2.5 quintillion bytes of data are created every day, meaning that 90% of the data in the world today has been created in the last two years alone.’ While industrial vision systems currently make a only a small contribution to this, data creation is increasing. Indeed, a line scan camera with a 16K sensor operating at 120 kHz line rate produces data at 2 GBytes/s.
Increasing data generation will require increasing processing power, but not necessarily equivalent data storage as frequently images are processed and measured on the fly and only those highlighting defects, for example, need to saved for later review. INDUSTRIE 4.0 will result in smart machines, storage systems and production facilities capable of autonomously exchanging information, triggering actions and controlling each other independently. Fundamental to this process is connectivity between systems and the interchange of data. At the lower level, data will be produced by a host of smart sensors which will certainly include industrial cameras.
The move towards INDUSTRIE 4.0 is already underway, with the emergence of products which can monitor an entire production process in real time, to identify which machines or processes have the greatest impact on overall productivity. Work is in progress involving some UKIVA members to integrate vision systems into this type of system. Code reading and verification, a well-established application for vision, will be a key factor in this process in order to eliminate operator data input error.
3D imaging
3D machine vision imaging is increasingly having a major impact in a wide range of industries and applications from volumetric measurements, to inspection for packaging and robot bin-picking. Laser profiling using triangulation is one of the most popular 3D techniques. The object to be measured passes through a line of laser light and a camera mounted at a known angle to the laser records the resulting changing profile of the laser line.
These 3D profiles deliver high measurement resolution with good measurement range. Another common 3D method mimics nature by using a binocular stereo set-up where two cameras are used to record 2D images of an object. A 3D image can then be calculated using triangulation. A random static illumination pattern can be used to add arbitrary texture to plain surfaces and objects that do not have the natural edges (texture) information which the stereo reconstruction algorithms require.
High speed imaging
The ability of vision to provide 100% inspection capabilities on production lines is dependent on the exposure times (to avoid motion blur) and data acquisition rates offered by the cameras used, as well as factors such as illumination intensity needed, camera and light source triggering, data capture, transfer, processing and storage. Year on year higher frame or line rate cameras are introduced meaning even faster processes can be monitored. In manufacturing industry inspection applications on high-speed production lines include product, packaging and label defect identification, label reading and verification for codes and human readable data, and web-based product inspection.
Process and machinery diagnostics are another important application since even minimal discrepancies in high-speed process machinery mechanisms can cause an entire production line to come to a standstill.
The UKIVA is a special interest group of the PPMA Group of associations. Its members include core vision technology suppliers, vision system integrators as well as equipment suppliers who use vision technology. UKIVA members who are vision technology suppliers or vision systems integrators can provide expert advice on the topics discussed in this article and on any other application for industrial vision.
- UKIVA Technology Presentation Hub
- 2020 UKIVA Machine Vision Conference Rescheduled to 2021
- First Machine Vision Conference keynote announced
- UKIVA to launch Vision Integrator Standard at conference
- Vision as an enabling technology for control & automation
- Focus on the best in vision
- First keynote for UKIVA Machine Vision Conference announced
- Talk to the experts at UKIVA Machine Vision Conference & Exhibition
- New Chair for UK Industrial Vision Association
- UKIVA Machine Vision Conference registration open
- Turnkey hovercraft drivetrain guarding
- More Ways of Identifying Objects
- HD Machine Vision
- Bespoke Vision Sensor Packages
- B&R NEW WEBSITE
- View Images & Overlay Graphics
- Get A Lock On 3D Measurement
- Entry-level vision system
- Multipix will launch the NEW Datalogic MATRIX 450
- Process, print and packaging inspection systems on show