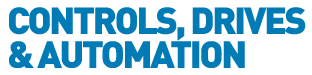
![]() |
Charlotte Stonestreet
Managing Editor |
Home> | AUTOMATION | >Machinery Safety | >Industrial robot safety |
Home> | AUTOMATION | >Robots | >Industrial robot safety |
Industrial robot safety
21 October 2016
Andrew Armstrong, Fanuc UK sales & marketing manager, explores how to keep robotics safe on the shop floor
If used without care, robots can be dangerous to humans. Back in 1961 when General Motors introduced the first industrial robot to its production line, humans were at high risk inside a robot’s work zone. Since that time, robot manufacturers such as FANUC have spent enormous effort and money to produce models with the best possible safety levels.
As robots have become more refined, and applied across more industry sectors, mainly for heavy work, devices are used to monitor a robot’s surroundings, such as vision and force sensors that allow robots to see and feel what is around them. Using smart synthetic skins, scientists are even looking to endow future robots with a human-like sense of touch.
Collaborative robots
In recent years, collaborative robots (Cobots) have emerged: in contrast to traditional robots, which cannot operate in an operator-occupied workspace without safety fencing, these cage-free robots can work side by side with humans on shared or separate tasks.
Although collaborative robots do not eliminate the need for workplace risk assessments, the increased adoption of peripheral safety devices is enabling robots and humans to work in close proximity of each other, eradicating the fear of interrupting production or worse, an accident.
Cobots are equipped with force sensing to limit their power and force: in any situation they can feel or detect an abnormal force and stop their motion immediately. Although they still cannot avoid a crash, Cobots can reduce its impact and avoid certain types of incidents, like crushing accidents. This makes them safer to work alongside humans.
Dual Check Safety (DCS) Position Speed Check
Dual Check Safety (DCS) Position/Speed Check features check the speed and positional data of motors with two independent CPUs within the robot controller. These functions can detect any position and speed errors immediately and shut down the motors power. Safety data and processes are cross-checked by two CPUs. Self-diagnosis of safety hardware and software is executed periodically to prevent potential failure accumulation.
Risk assessments
As collaborative robots are working alongside humans without any type of shield or guarding, it raises a new level of complexity.
In line with ISO 10218 and ISO/TS 15066 standards which relate to the collaborative operation and safety functions, end users or integrators will need to do a complete risk assessment to prove that their robotic application using a collaborative robot is safe.
When doing a risk assessment, while the robot itself may be safe, the entire robotic system has to be considered, including grippers and any other peripheral equipment.
From a safety point of view, grippers can cause pinching or crushing injuries and the risks of these should be taken into account in any risk assessment.
Practical measures
In order to ensure that humans are not exposed to unacceptable risks when working collaboratively, the current standards describe four separate measures that can be used to provide risk reduction.
It is required that at least one of these is fulfilled, in addition to having visual indication that the robot is in collaborative operation.
The four measures are:
- SAFETY-RATED MONITORED STOP: when it is detected that a human has entered the collaborative workspace, the robot should stop. The stop condition should then be maintained until the human leaves the workspace.
- HAND GUIDING: the human can guide the robot by hand. Additional requirements for safety include safe-limited speed monitoring and a local emergency stop.
- SPEED AND SEPARATION MONITORING: the robot must maintain a specified separation distance from the human and operate at a pre-determined speed. This measure requires careful risk assessment and needs to take account of safety distances.
- POWER AND FORCE LIMITING BY INHERENT DESIGN OR CONTROL: the power and force of the robot actuators need to be monitored by safety-related control systems to ensure that they are within limits established by a risk assessment.
Key Points
Increased adoption of peripheral safety devices is enabling robots and humans to work in close proximity of each other
In line with ISO 10218 and ISO/TS 15066 standards end users or integrators of cobots need to do a complete risk assessment
To ensure humans are not exposed to unacceptable risks when working collaboratively, current standards describe four separate measures
- Fuelling innovation
- Bleckmann quadruples its Kardex AutoStore
- New digital tool set to transform traditional product testing
- Manufacturing SMEs report strong sales growth
- Digital twin for sustainable & secure power grids
- GM Group to make MACH debut
- Funding secured for Silverstone based Digital Manufacturing Centre
- Research project for the use of hydrogen in aviation
- Robotics for the nuclear industry
- Tech skills gap hampering recovery
- OVERVOLTAGE PROTECTION
- Balls to Gravity
- ROBOTS GIVE FASTER CELL TOOL CHANGE TIMES
- ROBOT FOR DELICATE ASSEMBLY
- MAKING THE MOST OF SAFETY BENEFITS
- NUMBER OF ROBOTS IN UK ON THE RISE
- EXTEND MOBILE INTO MAINTENANCE
- Electronic Locking
- The future is bright - The future is automation!
- Machinery Safety Roadshow