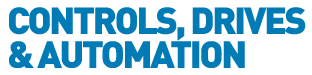
![]() |
Charlotte Stonestreet
Managing Editor |
Five key elements for effective IIoT implementation
15 May 2017
Industrial automation exists within a broader technological framework and has benefitted from advances in industrial networking and mobile computing, reports Andy Pye
The combination of these technologies is helping to make the vision of concepts like the “Connected Factory”, “Industry 4.0” and the Industrial Internet of Things (IIoT) a reality. Often however, the proliferation of competing concepts can lead to confusion and leave some questioning how to begin practical implementation.
A white paper has been published by Red Lion Controls defining these concepts, and examining key elements organisations should consider when devising an effective implementation strategy.
The Connected Factory is the vision of a manufacturing environment where every machine is able to communicate with all other machines and devices across the plant floor and other remote locations. The purpose of the Connected Factory is to connect, monitor and control virtually anything, anywhere to drive operational productivity and profitability.
Similar to the Connected Factory and Industry 4.0, IIoT will mean that organisations will be able to connect many different devices, including older equipment, and get them to “talk” with each other in a way that they could not before. By gathering data from both new and legacy devices, organisations can use that data to improve efficiency and gain a competitive advantage.
Many of today’s organisations are eager to implement Connected Factory, Industry 4.0 and/or IIoT concepts to realise benefits, such as reduced operational costs and better visibility and control. While it is, however, unrealistic and cost-prohibitive for most organisations to construct green-field facilities or “rip-and-replace” legacy equipment, many solutions utilise existing equipment and allow components to be strategically deployed to extend monitoring and control capabilities without impacting day-to-day operations. When updating a facility, it is important that expectations be set early. Despite the vision of an IP address for every piece of equipment in a network, the reality is end users will not be able to log into every panel meter, water pump and drive from mobile devices.
Bringing a facility into the 21st century involves several core fundamentals to help ensure a smooth transition and provide the ability to access, monitor and control information from anywhere.
Key elements discussed in the white paper cover:
- Legacy Equipment
- Protocols/Communication
- Location/Environment
- Security
- Staff
Industrial controller for extreme industrial environments
Red Lion Controls has launched the new Graphite Edge Controller, which was on show at Industry 4.0, the summit and exhibition held in Manchester in April. The compact rugged industrial controller offers highly scalable I/O and combines networking and data visualisation with industry standard IEC 61131 control capabilities in a small, easy-to-deploy footprint.
The Graphite Edge Controller provides a rugged industrial controller for the process and factory automation market, with wide operating temperatures to control and monitor machinery in harsh environments.
“The Graphite Edge Controller is an important product to round out Red Lion’s rugged Graphite platform,” said product management director Paul Bunnell. “Its all-metal construction and broadly expandable I/O capabilities allow customers to use Edge Controllers in the harshest of environments, at virtually any scale – from factory automation applications to remote process applications.”
The device is equipped with the Crimson 3.0 software, to interconnect devices using over 300 industrial protocols and use IEC 61131 programming languages – such as ladder logic, function block and structured text – to solve specific application needs, in addition to providing data logging and web serving functionality.
Industry 4.0 Summit
April 2017 saw two major manufacturing events hosted in the UK – the Industry 4.0 Summit and - running in parallel - the Factories of the Future EXPO. This showcased new technologies in automation, robotics, software, sensors, virtual reality, augmented reality and other related areas.
The Industry 4.0 Summit featured two days of presentations from 40 leading experts on 4.0, IIoT, smart manufacturing with plenty of case studies of industry 4.0 in action. There were 300 attendees to the Summit.
- Ethernet Switches
- Red Lion unveils next wave of compact NT24k Gigabit Ethernet industrial switches
- RTUs get ATEX approval
- Overseeing relationships & growth
- Red Lion adds compact industrial Gigabit and PoE+ DIN-rail switches to NT24k platform
- Web-based event engine
- Red Lion N-Tron Series managed switches certified by ODVA to meet CIP specification
- Ethernet industrial switches
- Ramp soak options
- Executive appointments
- No related articles listed