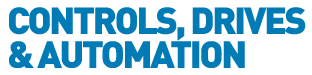
![]() |
Charlotte Stonestreet
Managing Editor |
Home> | AUTOMATION | >Machinery Safety | >Keeping pace with technological change |
Keeping pace with technological change
05 March 2018
The connected world of Industry 4.0’s smart factories adds a new dimension of complexity in terms of machinery safety challenges, as adaptive and dynamically configurable machines and machine modules allow unique combination of machines for higher efficiency and productivity on the shop floor. Paul Taylor, manager for Machinery Safety at TÜV SÜD Product Service, explains more
Industry 4.0 is a system of collaborative computational, mechanical and electrical elements which communicate in real time, enabling smart factories to digitise processes that improve both efficiency and quality, while reducing manufacturing costs. Often referred to as the ‘fourth industrial revolution’, Industry 4.0 includes cyber-physical systems, the Internet of Things (IoT) and cloud computing.
In order to realise the potential of today’s digital transformation while remaining safe, secure and competitive, businesses must adopt an effective approach to manage their processes, systems, physical and data assets.
The digital transformation of production equipment and production lines will impact the communication between machine modules (M2M) and between products and machines (P2M). However, in today’s static machinery environment, the configuration of machines and machine modules in the production line is completely known at the starting point of the system design. If substantial changes are made, a new conformity assessment may be required.
It is an employer’s responsibility to ensure that all machinery meets the requirements of the Machinery Directive and Provision and Use of Work Equipment Regulations (PUWER), of which risk assessments are an essential ingredient. Therefore, if a machine has a substantial change made, a full CE marking and assessment process must be completed before it can be returned to service. Any configuration change in the production line may require re-certification of the whole facility.
Instant updates
However, the dynamic approach of Industry 4.0’s cyber physical systems means that with a simple press of a button, easily configurable machinery and production lines can be instantly changed. As it is the original configuration that is risk assessed, such instant updates to machinery mean that the time-hungry, traditional approach of ‘risk assessment as you make changes’ will become obsolete.
The risk assessment process therefore needs to be modified to meet the demands of the more dynamic Industry 4.0 approach. This would mean that all possible configurations of machines and machine modules would be dynamically validated during the change of the production line. Each new configuration would be assessed in real time, based on digital models of the real behaviour of each configuration, which would be based upon the machinery manufacturer’s correct (and trusted) data about the Cyber Physical System. The result would be a rapidly issued digital compliance certificate.
Machinery safety in our current Industry 3.0 world therefore looks like this:
- Safety Assessment of machinery to the machinery directive MD 2006/42/EC
- Risk assessment (ISO 12100)
- Safety concept assessment (SRECS)
- Development of safety functions acc. to ISO 13849 or IEC 62061 for complex safety sub-systems
Whereas machinery safety in an Industry 4.0 world would look like this:
- Safety Assessment of machinery to the machinery directive MD 2006/42/EC
- Modified Risk assessment (ISO 12100) in case of human-machine interaction
- Safety concept assessment (SRECS)
- Development of safety functions acc. to ISO 13849 and IEC 62061 for complex safety sub-systems
Industry 4.0 takes safety assessments into four separate domains – the smart factory (cyber-physical production systems), vertical integration (automation), horizontal integration (with other systems outside the main production environment) and human-machine integration. The introduction of a modular certification approach will enable machinery safety practice to keep pace with technological change by reducing complexity based on customer-specific modular approaches. This will create a circle of continuous learning, where 95% of validation runs in real time, with modular certification software running as a kind of assistant system and new questions and problems being solved by human experts.
Key Points
- It is an employer’s responsibility to ensure that all machinery meets the requirements of the Machinery Directive and PUWER
- If a machine has a substantial change made, a full CE marking and assessment process must be completed before it can be returned to service
- The risk assessment process needs to be modified to meet the demands of the more dynamic Industry 4.0 approach
- TÜV SÜD BABT appointed as Machinery Notified Body
- UK’s first dedicated Industry 4.0 IoT cellular test service
- Machinery Safety UCPD Courses
- Machinery Safety Roadshow
- Shaker Puts Environmental Testing Laboratory Ahead
- TÜV SÜD UK Appoints Mary Grigsby as Head of Product Service
- Faster access to Russian, Belarus & Kazakhstan markets
- Wireless module warning
- Ensuring electrical safety in hazardous areas
- TÜV SÜD launches machinery SIL certification service
- OVERVOLTAGE PROTECTION
- MAKING THE MOST OF SAFETY BENEFITS
- EXTEND MOBILE INTO MAINTENANCE
- Electronic Locking
- Machinery Safety Roadshow
- Machinery Safety UCPD Courses
- GUIDE TO EX NA INSTRUMENTATION INSTALLATION
- Safety Relays Meet SIL3 Requirements
- IECEx Approval
- ARE YOUR SAFEGUARDS AS SAFE AS YOU THINK?