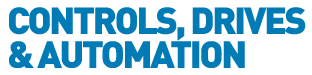
![]() |
Charlotte Stonestreet
Managing Editor |
Home> | MACHINE BUILDING & ENGINEERING | >Enclosures | >Rittal unveils new large enclosure system |
Editor's Pick
Rittal unveils new large enclosure system
23 April 2018
After five years in development, Rittal has launched its new VX25 large enclosure system at this year's Hannover Messe. Embracing Industry 4.0 philosophies in terms of both application and manufacture, it has been fully developed to meet requirements for increased productivity in control and switchgear manufacturing.
Reported to offer the highest possible quality and consistency of data, reduced complexity and savings in time, as well as safe assembly, the VX25 features more than 25 registered patent and trademark applications, demonstrating the high level of innovation involved.
Right from initial concept, Rittal's aim has been to make the best – in the form of its renowned predecessor, the TS 8 system – even better as conveyed by Dr Thomas Steffen, managing director Research and Development at Rittal, who comments: “The market needs an enclosure that cuts throughput times in engineering and assembly, reduces complexity and that finds a place for itself as a full-grown module in the megatrend of digitisation.
"The new Rittal large enclosure has now become 100 percent Industry 4.0-capable. With the combination of a real enclosure and its digital twin, the new development will meet every future digitization needs – from online configuration and engineering to assembly, as well as automation, logistics and maintenance.”
The development process for the new large enclosure system involved extensive dialogue with Rittal customers. A large-scale, scientifically based usability study collated words, images and moving film to document the everyday working life of control and switchgear manufacturers, covering ten companies in Germany, eight in the USA and six in China, including small, medium-sized and large companies.
“This user analysis was an eye-opener. In some cases, we spotted problems that the customers themselves hadn’t yet identified,” says Dr Steffen. As a result, 150 systematically recorded and specific requirements for a new enclosure emerged, providing developers and product managers with a robust guide for the actual development work. Rittal also used the findings of the customer advisory council, which was also involved, to complement this.
The heart of the VX25 system is the newly developed frame section. It determines the installation space, the efficiency in engineering and assembly, the expansion options, the stability and thus the reliability and flexibility in the customer’s workshop. The new large enclosure system maintains all the important and established product features of the existing TS 8 large enclosure system and to expands them significantly with a multitude of new functions and customer benefits.
Amongst the notable benefits of the VX25 are the significantly reduced number of components installed and the system's consistent 25mm pitch pattern, which has helped to make the number of individual parts at all levels and across enclosures fewer. The 25mm pitch pattern also means the enclosure can be expanded much more flexibly, even beyond its limits if required.
Installation components for the vertical frame parts components now also fit in the enclosure’s roof section and base area. When the enclosures are bayed, the 25mm pitch pattern also continues through into the adjacent enclosures. As a result, rails can be mounted over multiple enclosures, for example. These and other baying options can now be implemented with a 40 percent smaller range of punched sections with or without mounting flanges. This way, inventories and logistics outlay can also be substantially reduced. At the same time, the new frame section in 20mm installation depth provides more space in the enclosure, space which is now available for the installation of components. Depending on the application involved and the components used, smaller switchgear can be used, which translates into lower costs.
Reduced complexity
A clear reduction in complexity also impacts the assembly and disassembly of the doors. This work can now be performed in one-person assembly without any tools whatsoever. The door is simply hung in the hinge. The hinge is designed so that the door is automatically secured when closed, so that unintentional lifting is avoided.
All common variants are available in future for use in the locking system. Electronic locking systems, which are increasingly being used in response to increased safety demands, can also be easily retrofitted. Here too, no subsequent machining of the door is required because the bushings needed for the cables are already present.
A number of innovations have also been implemented when it comes down to joining up enclosures in bayed suites. The new baying system needs far fewer parts. Since all the screws are mounted in the direction of the bay, assembly is also simplified. A new baying seal, which is simply snapped on, ensures that the enclosure’s degree of protection is retained when baying.
“What is new is that no enclosure system has ever been previously developed so consistently and systematically to ensure maximum customer benefit. The VX25 matches the way the control and switchgear manufacturer thinks and works – both in functions and processes," says Dr Steffen.
- Electrical safety assured with Rittal's TS 8 baying system
- Temperature management in the food industry
- Design & size a busbar
- Design is everything
- Design Time Reduction
- Condensation Eliminated
- Hygienic climate control
- Energy-efficient enclosure cooling
- New Busbar System Ri4Power 185mm for safe & quick switchgear
- Maximising ROI from enclosures