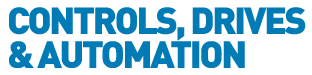
![]() |
Charlotte Stonestreet
Managing Editor |
The answer is blowing in the wind
02 March 2021
2020 saw almost a quarter of the UK’s electricity being generated by wind turbines, representing almost double the share of wind power in 2015, and up from a fifth of the UK’s electricity in 2019. Charlotte Stonestreet highlights some of the technologies behind the statistics
According to independent analysis conducted by academics from Imperial College London for Drax Electric Insights, via Imperial Consultants, power from renewables overtook fossil fuels in the UK for the first time in 2020 – and carbon emissions fell by 16% year-on-year.
However, as this was in a large part due to reduced demand caused by Covid lockdowns, when gas and coal power stations were turned down, the UK will need to deploy a range of new green technologies, which complement renewables like wind and solar, if it is to meet its climate targets
Wind and solar generated 30% of Britain’s electricity in 2020 – around half the share required by 2025 for the UK to reach its climate targets according to the Climate Change Committee (CCC). The Electric Insights report shows that achieving the CCC’s targets will also require a range of other technologies, such as bioenergy with carbon capture and storage (BECCS), hydrogen and nuclear.
Dr Iain Staffell of Imperial College London, and lead author of the quarterly Electric Insights report, said: “2020 saw Britain edge closer to the power system of the future with renewables generating more power than fossil fuels. Flexible technologies like pumped hydro storage kept the system stable as supply from renewables increased and demand for power fell.
“The next steps we must take towards a net zero power system will be more challenging – driving out the last sources of fossil carbon will require us to go beyond just having more wind and solar power. New business models, backed by policy and investment, will be needed to bring advanced-but-proven technologies into the mainstream."
Flexible power systems
To enable a decarbonised power system, with increasing volumes of intermittent renewables, from diverse sources such as wind, wave, marine, hydro, biomass and solar, there is a need for much greater flexibility in the decentralised energy system to maintain grid balance. Government analysis estimates that “a smarter, more flexible system could unlock savings of up to £12bn per year by 2050”.
Meeting these needs, digitisation of the energy sector using RTUs is happening at pace. Historically, maintenance engineers didn’t have visibility of asset conditions within the grid — adopting a reactive rather than proactive approach, simply because they didn’t have the technology to inform them of when and which asset required attention. However, according to Matthew Hawkridge chief technology officer at Ovarro, deployment of remote telemetry unit (RTU) systems is changing this, creating smart grids that help utility firms optimise service to customers. The RTUs, even though they only a small element of this network, are critical because they capture data from a wide range of assets and convert it into effective management information.
Recent advances make it possible for each RTU to act autonomously or communicate by radio with a telemetry data gateway that is connected to a cloud computing infrastructure equipped with appropriate software capable of presenting processed information to management. Reliable low-band telemetry can collect data from most assets in the energy sector, where they act as the ‘canary in the mine’ when it comes to predicting, diagnosing and communicating outage events.
One of the key benefits of RTUs is that they can perform autonomous control in real time and then report to SCADA that it has everything under control. Operators at the SCADA interface can ‘supervise’ the operations by setting new KPIs or updating instructions — open/close this, start/stop that, for example — for RTUs to then act upon and manage locally.
Undisrupted energy
With renewable energy sources providing more of the country’s electricity than ever, Aggreko is highlighting the importance of energy storage solutions. Specifically, battery technology can help ‘smooth’ fluctuations associated with wind power and other green energy sources, allowing for consistent energy provision during periods of high demand but lower generation.
According to Aggreko, the implementation of battery technology will be crucial to moving away from a peak-and-trough approach to renewable energy generation, and ensuring a stable supply, as Chris Rason, managing director, Aggreko Northern Europe explains: “Though the UK’s green energy revolution continues apace, issues around consistent grid supply, and the disruption it can cause, may hamper the adoption of environmentally friendly power sources.
"Battery technology can provide a means of alleviating fluctuating power risks associated with renewable energy sources, helping us transition to a greener, net zero future. While it is not a new concept, progress made in the rental space means it is now much more accessible for companies to access on an industrial scale, without the prohibitive purchase costs of even three years ago.”
Turbine blade production
One of the highest-profile UK renewables stories is Siemens Gamesa’s wind turbine blade factory at Green Port Hull, where Siemens Digital Industries (Siemens DI) has successfully deployed industrial communications network solutions.
The factory, a £310m investment by Siemens and Associated British Ports (ABP), manufactures 75m blades for 7MW and next generation 8MW turbines. When the IT and OT project was commissioned in 2017 its sheer scale and magnitude required meticulous planning, especially in the area of communications networks, considering the remote location, harsh quayside environment and size of the factory.
It was crucial that internet connectivity was not compromised, and the operations team needed to ensure that work would not be disrupted or halted. The manufacturing systems would equip the shop floor with 70 computers for engineers to work from. However, these computers could not remain fixed as the layout of the factory needed to adapt to meet production demands.
Siemens DI team deployed its Scalance range of integrated solutions to ensure efficient industrial networks and bus systems. A holistic approach to routing, security applications, remote access and industrial Wireless LAN played a key role in the smooth delivery of the project.
Similarly, Industrial Wireless LAN (IWLAN) solutions were used to guarantee maximum reliability and performance. The site needed flexibility without cables, secured real-time data transmission and more space in the control cabinet. The Scalance W range was used so additional features or ifeatures for the network could be activated via KEY-PLUG W700 iFeatures in selected devices in the SCALANCE W-700 range.
Pitch drive control
As the wind power sector expands, KEB Automation is seeing an increase in demand for its drive controllers, motors and brakes for onshore and offshore wind turbines. Pitch and yaw drives, pitch motors, as well as pitch and yaw brakes from KEB, are proving popular as a central safety component in wind turbines, including the latest high power (10MW and above) turbines.
The manufacturers of wind turbines have special requirements that must be met. "In the wind sector, robustness plays an important role, as do long maintenance intervals, because the turbines are exposed to a wide variety of environmental conditions," explains Roger Brohl, product manager for the wind sector at KEB Automation. "From very cold to very warm, with high vibrations in the nacelle, which means drives and brakes have to withstand everything."
Brohl continues: "The keyword here is safety. The pitch drives are a central safety component of the wind turbine. In the event of a power failure, a storm or a fault, they must ensure that the turbine blades reach a safe position – the so-called vane position."
Turbine towers
When it comes to producing wind turbine towers, due to their size, individual cone segments are welded together. Precision and repeatability are prerequisites in this process, which is why specialist manufacturer of critical assemblies for wind turbines, Talleres Ganomagoga, relies on linear roller guide technology from NSK.
The company uses large welding machines based on a column and boom concept. These ‘circular welding columns’ weld the internal and external joints of the long steel hoops that form the cones of wind turbine towers. In terms of capacity, the machines can accommodate cones measuring up to 7m in length and 5m in diameter.
To help expedite its welding process, Talleres Ganomagoga required a way of moving a machine along the length of a tower as it grew in size during manufacture. By collaborating with the expert team of engineers at NSK, this vision soon became reality.
Today, the company joins the cones together by manoeuvring a circular welding column along a specially devised system of linear sliders and rails from NSK’s precise and reliable RA series. The combination of NSK super high-load linear sliders and NSK rails (in lengths of 9.225m and 7.8m) helps Talleres Ganomagoga achieve precise movement of its special welding machines in line with production demands.
Inspection & repair
Once a wind turbine is in operation it is imperative that the blades are regularly inspected. Towards the end of last year, the world’s first blade walk by a robot on an offshore wind turbine was achieved thanks to BladeBUG and the Offshore Renewable Energy (ORE) Catapult. Over two days in mid-October, the six-legged inspect-and-repair robot repeatedly scaled blades at ORE Catapult’s 7MW Levenmouth Demonstration turbine off the coast of Fife.
BladeBUG represents a 30% reduction on current blade inspection techniques, which are conducted by rope-access technicians. For next generation turbines, ORE Catapult predicts the cost savings could reach as much as 50%. These costs have traditionally been one of the primary areas of concern for offshore operators, as sea conditions and faster tip speeds can lead to significant blade damage over time.
The robot is being developed under a £1 million collaboration project between BladeBUG and ORE Catapult, part funded by Innovate UK. By the project’s end BladeBUG will be capable of inspecting blade surfaces for emergent cracks and imperfections, transmitting data on their condition back to shore and resurfacing the blades.
The robot is also a key component of the £4.2 million MIMRee project which will demonstrate a fully autonomous inspection and repair mission to an offshore wind farm. During these trials, BladeBUG will work in collaboration with an autonomous vessel and teams of drones, using a robotic arm to clean and resurface damaged blades. The final MIMRee system technology trials are set to take place in mid-2021.
Key Points
- Wind and solar generated 30% of Britain’s electricity in 2020; around half that required by 2025 to meet climate targets
- Reliable low-band telemetry can collect data from energy sector assets, helping to predict and diagnose outage events
- Battery technology can help ‘smooth’ fluctuations associated with wind power and other green energy sources
- New four-phase method for motor control
- Funding for green electric revolution
- £53 million funding for UK manufacturers
- Hyundai & Kia debut VR design evaluation system
- Pump up the savings
- Peugeot uses 3D printing for car accessories
- DTC or FOC - which is better?
- First UR+ Application Kit for quality inspection
- Beyond the manufacturing plant
- UK manufacturers leading the way
- No related articles listed