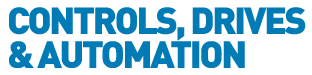
![]() |
Charlotte Stonestreet
Managing Editor |
Home> | DRIVES & MOTORS | >Variable Speed Drives | >Injection moulding energy costs cut |
Injection moulding energy costs cut
25 April 2014
Manufacturer of water fittings and valves, Atlantic Plastics, is saving 20 percent of the energy costs of a large injection moulding machine, following the fitting of an ABB variable speed drive.
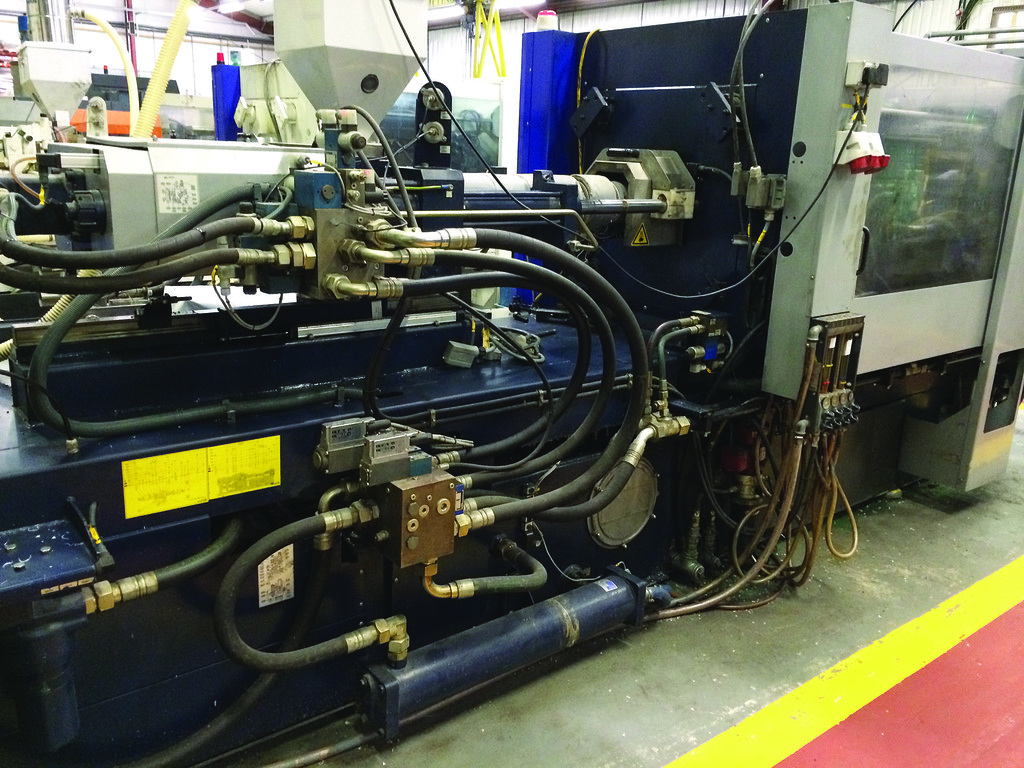
The company, which carries out all injection moulding on site using 36 machines, wanted to cut energy costs for its production as well as improve its environmental credentials.
An investigation showed that the existing direct-on-line installation used 25.3kW. ABB authorised value provider, APDS, installed a trial drive at the site to measure the actual demand required and match the flow to this demand. This drive drew 10.5kW, giving an average hourly saving of £1.28 in electricity costs. These readings were confirmed by Atlantic Plastic using their own power meter.
The IP21 drive is supplied in a floor mounted steel enclosure. Because it is on the shop floor, the enclosure provides extra protection for the drive from collision with vehicles and the moving parts of other machinery.
- ABB’s YuMi comes to Smartech Selfridges
- Touchscreen data recorder
- Total Plant Automation For Power And Water Sectors
- ABB wins Supplier of the Year at Pump Industry Awards
- High performance PLC
- Extra production days gained
- Definitive guide to the big six flowmeter technologies
- ABB launches virtual technical assistance support service
- Lessons learned from ICS cyber incidents
- Transformer intelligence
- PUMPED UP PERFORMANCE
- SOFT STARTER OR VARIABLE SPEED DRIVE?
- Jeans With Less Energy
- Enhanced to Withstand Tough Environments
- Savings From Improved Torque Ratio & Efficiency
- Modular VSD
- ENERGY SAVING: AN OLD MESSAGE WITH NEW PROMISE
- Updated installation guide for power drive systems
- UK drives manufacturer seals global automation deal
- WEG motors & drives power high-efficiency air blowers