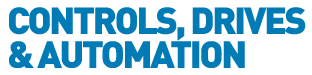
![]() |
Charlotte Stonestreet
Managing Editor |
Home> | AUTOMATION | >Controls | >Increased flexibility & simplified engineering |
Editor's Pick
Increased flexibility & simplified engineering
03 December 2020
ROCKWELL AUTOMATION recently marked the first decade if its PlantPAx modern distributed control system (DCS) with PlantPAx Release 5.0, which features improvements in scalability as well as providing easier plantwide information access for data-driven decision-making across facilities and enterprises. It has also added new controllers and workflows to streamline projects and reduce engineering effort.
"Rockwell Automation's overall goal is to enable The Connected Enterprise for its customers, so they can achieve digital transformations and take advantage of new technologies, and that's what PlantPAx really embodies," said Blair Wilson, global marketing manager for PlantPAx at Rockwell Automation. Wilson presented "Overview of the new PlantPAx 5.0 system: What's new and what's next" at the Process Solutions User Group conference, held as part of the company’s Automation Fair at Home event.
"PlantPAx and its modern DCS approach has four main pillars: plantwide, scalable and modular, secure and flexible. Plantwide means a common-core technology that can transition intuitively and effortlessly between different plant areas. Scalable means it can be applied in simple or complex applications, while its modularity allows customers to grow. Secure means that, even as we go through digital transformation to achieve The Connected Enterprise, it's still important to be able to push information throughout your facility and the organisation in a secure manner, and PlantPAx supports that. Flexibility in delivery and support is based on the dual path our customers have: our army of system integrators, who are fantastic to work with, and are experts in a variety of industries, and our extensive team of subject matter experts who can deliver and support our customers."
To help users design, build and improve a control system over its lifecycle, Wilson reported that PlantPAx's root goals are to make it easy to design, configure and integrate, save engineering costs and reduce commissioning hassles. In the design lifecycle phase, PlantPAx accomplishes this by providing:
- Characterised systems and validated architectures for optimal performance of the DCS servers, controllers and required memory
- Speed and ease of programming and system configuration, including preconfigured templates and process libraries
- Premier integration of its common-core technology with motor control and field instrumentation
- Ease of integrating primary processes with other OEMs, including no need for data remapping.
In the sustain lifecycle phase, PlantPAx improves operations, empowers operators, and reduces training costs by providing:
- Graphics that are focused on simplicity and situational awareness
- Real-time display of process variables, alarms and trends
- Multi-lingual support for multiple user modes
- Integrated reporting tools to convert data into usable information in real-time
- Trends with optimised display of event information with real-time and historical data about it
- Effective alarm management that directs an operator's attention to required tasks
- Improved maintenance with high availability of servers, controls and networks, out-of-the-box diagnostics for system issues, seamless visibility of devices for asset management, and "breadcrumbs" that highlight modules in abnormal state to quickly learn what's been changed and needs attention.
"The breadcrumb system in our faceplate library lets operators intuitively and quickly track down the root causes of an issue," explained Wilson. "However, scaling also means improving over the lifecycle of a facility, especially as users bring in added equipment and increased complexity."
5.0 to conquer batch, hybrid, heavy industries
Because its essential mission has always been putting together trusted hardware and software for consistent outcomes, PlantPAx 5.0 is surpassing itself to become purpose-built for plantwide control of batch, hybrid and heavy-industry applications. In all these new settings, Wilson reported its five core tenets are: reduced footprint, consistent delivery for customers, streamlined workflows, guided cybersecurity and enabled analytics.
"PlantPAx 5.0 can serve larger and more complex operations securely with reduced footprint due to simplified architectures, new purpose-built controllers, embedded process objects, automatic hardware diagnostics, IEC 62443-3-3 cybersecurity certification, improved HART integration, and improved support for validated industries."
The two new ControlLogix and CompactLogix controllers streamline their former control environment by now deploying several features natively, such as embedding instructions and task modelling to minimise project design time. Benefits include out-of-the-box settings and instructions that follow PlantPAx guidelines, ControlLogix controller performance profiles, and intuitive workflows that eliminate unneeded rework, and simplify design and deployment efforts.
"We also transitioned the process objects library to be the embedded process instructions in the controller," added Wilson. "These instructions have a reduced footprint because they're native to the controller, and are no longer added after the fact. They also use a graphical user interface (GUI) to configure and troubleshoot the instructions, which makes doing this easier and quicker than it has been before. This will also make these instructions more consistent, whether they're delivered by your system integrator down the road, from Rockwell Automation's solutions business, or from somewhere overseas. The GUI also streamlines workflows by embedding instructions within the HMI."
Easier alarms, libraries—and HART
In addition, PlantPAx 5.0 further streamlines tasks for users by providing Select and Go alarms as part of its instructions. This will:
- Allow simple alarm configuration and setup
- Use one environment to deploy alarms when creating control elements using Logix Designer software
- Provide one location for adding and configuring alarms
- Use one click to add an alarm from an object's definition
- Provide predefined alarms for every object; and let users enable alarms for each instance.
"This lets users go in, turn on the alarms they want, and that's it," said Wilson. "This lets them move on to more complex or more value-added tasks."
Similar to its easier and embedded instructions, Wilson reported that PlantPAx has added dual library support. "We're continuing to support PlantPAx 4.0 and 4.1 libraries," he explained. "These libraries have the same look as feel as the new library, so users can take a phased migration approach, which will help when they bring new functions into their facilities.
"PlantPAx will also show dashboards of process instructions per task to optimise visibility and task balancing. It can be used with an embedded webpage that shows CPU utilisation and avoids task overlaps. This will allow more consistent performance and task loading during project creation, and make it easier to identify how many control strategies are running. We're also offering automatic creation of consistent task models in Logix Designer software."
Likewise, PlantPAx 5.0 will provide highly integrated HART functions. These will let users:
- Add and replace HART devices online
- Show HART signals and connection status, indicated in a Logix Design I/O tree in Studio 5000 software
- Display integrated device diagnostics via profile
- Allow connection type selection in PlantPAx.
"The benefits of these HART capabilities will allow more intuitive integration and the inclusion of device diagnostics in PlantPAx's data type connection, and will give users an out-of-the-box faceplate for rendering HART content," added Wilson.
- Collaboration key to reduced cyber risk
- Dual VPN & firewall capabilities
- Just enough control
- Live art installation challenges public perception of robotics
- Optimising uptime
- Rockwell to acquire Avnet expanding cybersecurity expertise
- Next-generation electronic overload relay
- Addresses bandwidth requirements
- Leading EDGE seminars address key business issues
- ENHANCED PROCESSING