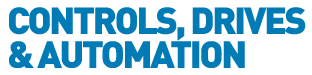
![]() |
Charlotte Stonestreet
Managing Editor |
Home> | AUTOMATION | >Handling & Logistics | >20kg payload cobot palletiser |
Home> | AUTOMATION | >Robots | >20kg payload cobot palletiser |
20kg payload cobot palletiser
26 June 2023
OMRON RECENTLY launched the new TM20 collaborative robot (cobot) with a payload of 20kg, whilst keeping its small footprint and providing a reach of 1.3m, making it suitable for tasks such as palletising.
Recognising the potential of the TM20 and the new opportunities it could bring, Reeco a specialist in the manufacturer and delivery of a wide range of palletising solutions and an official UK solutions partner of Omron, was quick to adopt the TM20 and expand their palletising offering. The new RB2000 palletiser is a 20kg payload, cost effective, market ready solution which makes end-of-line robotic automation attractive to producers of all sizes.
With the introduction of the RB2000, Reeco believes that it has now evened the playing field between traditional industrial robot palletising and cobot palletising. Manufacturers of all sizes now have an opportunity to palletise heavier products but maintain the smaller footprint offered by the Reeco RB range, thus not requiring further factory space but rather creating an automation process to help their existing lines.
But what are the options when it comes to automated palletising and the differences between traditional industrial robot palletising and cobot palletising?
As Reeco’s managing director Lel Rees explains, robot palletising has been a crucial part of the manufacturing industry for decades. These industrial robots are designed to perform repetitive tasks with precision and speed, making them ideal for palletising. However, with the advent of collaborative robots or cobots, the palletising industry has undergone a significant transformation. But what are the differences between traditional industrial robot palletising and cobot palletising?
Traditional industrial robot palletising involves the use of large and heavy robots that are programmed to perform specific tasks. These robots are designed to handle heavy loads and operate at high speeds, making them ideal for palletising large volumes of products. Traditional industrial robot palletising is ideal for applications where speed and precision are critical.
One of the primary advantages of traditional industrial robot palletising is that it is highly reliable. These robots are designed to operate 24/7 without fail, making them ideal for high-volume manufacturing environments. Additionally, traditional industrial robot palletising is highly customisable, allowing manufacturers to program the robots to perform specific tasks.
However, traditional industrial robot palletising also has some significant drawbacks. Firstly, these robots are expensive to purchase and maintain. Additionally, traditional industrial robot palletising requires a dedicated space to operate, which can be challenging for smaller manufacturers with limited space
Collaborative robots on the other hand are designed to work alongside human operators, performing repetitive tasks that are either dangerous or tedious. Cobots are smaller and lighter than traditional industrial robots, making them more flexible and easier to deploy.
- End-of-line automated
- OMRON listed in Dow Jones Sustainability World Index
- Connect with confidence
- OMRON awarded Gold Rating for LGBTQ+ initiatives for 6th consecutive year
- Omron awards suppliers with green certification
- Omron’s new N-Smart sensor family
- Trends in AI & robotics beyond 2020
- Food-grade models added to SCARA range
- OMRON adds EtherCAT models to i4L SCARA robot series
- OMRON UK and Brillopak forge strategic partnership
- Balls to Gravity
- ROBOTS GIVE FASTER CELL TOOL CHANGE TIMES
- ROBOT FOR DELICATE ASSEMBLY
- FIRST FASTBOX
- NUMBER OF ROBOTS IN UK ON THE RISE
- Tailor Made For Automated Warehouses
- Number of Operators Reduced
- Prevents Potential Material Release
- Integrated or Standalone
- The future is bright - The future is automation!