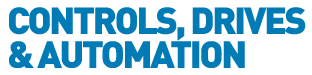
![]() |
Charlotte Stonestreet
Managing Editor |
Home> | IIot & Smart Technology | >IIoT | >Trends in AI & robotics beyond 2020 |
Editor's Pick
Trends in AI & robotics beyond 2020
25 February 2020
At the beginning of new year and a new decade, many companies are wondering which technologies they should be monitoring in 2020 and beyond. Automation and robotics expert, Omron, has identified the most important trends and developments over the coming year.
Artificial intelligence (AI) has been the subject of considerable hype for several years and is starting to break through in the industrial sector. McKinsey recently forecasted that the global market for AI-based services, software and hardware will grow by up to 25% annually and will be worth around US$130 billion by 2025. But AI also represents a major challenge for industries in Europe, which are lagging behind the US and China. So, how can we start putting AI into action? Predictive maintenance is one area that demonstrates its advantages and potential.
Omron believes that the industry is now ready to move to the next stage, and that the emerging practical industrial automation solutions should focus on ways in which AI can enhance human intelligence, or augmented intelligence, and how it can be implemented on the factory floor, whilst ensuring sustainability. These solutions will support people working in industrial automation in decision making and improve operational efficiency.
We’ve identified the following AI trends in robotics and industrial automation:
1. Valuable machine data generated at the edge. A new generation of workers in industrial automation will change jobs more frequently than ever before. The latest developments in factories depend on the generation and collection of deep knowledge and data insights at machine level – i.e. at the edge. The machine can learn from its human operators and subsequently improve the output. Technology controlled by AI can empower machine learning by predicting both product and equipment failure, using data generated by Industrial Internet of Things (IIoT) devices. The analysis and use of combined data enable users to rapidly predict potential machine errors, preventing disruptions and the deterioration of product quality.
2. Increased efficiency through self-learning algorithms. With the change from mass customisation to a high-mix, low-volume approach (Lot size 1), efficiency must be improved by reducing human errors and machine downtime. AI with learning algorithms can help machine operators to achieve the best result in every change-over. Innovative control technology can also help employees to work alongside robots and machines to achieve manufacturing excellence. This is accomplished by using a broad range of factory automation equipment that enables IIoT-capable production or implements optimal AI algorithms in the equipment. The AI-equipped controller is designed to immediately detect signs of any equipment irregularity. The machine automation controller's AI algorithms allow it to learn the repeated movements of equipment from precise data from sensors. This in turn provides feedback for status monitoring and the real-time control of machines.
Let’s take a bottling application as an example: the bottles are carried via a conveyor belt and filled. The AI controller learns what a normal situation looks like when no failures occur. In case of a disturbance, such as blockage causing selective friction, anomalies will be detected by the AI controller. The filling process will shortly pause and resume when the process is stabilised. This prevents any failure from taking place, for example spilling liquid on the packaging line, which in turn helps reduce machine downtime and waste.
Transforming production and implementing AI can help manufacturers to prolong equipment longevity and detect unforeseen events to prevent failures. This reduces the risk of equipment damage and downtime. Using AI helps optimise what needs to be done to improve; driven by practical requirements to noticeably improve overall equipment efficiency (OEE). What’s more, an improvement of just a few percentage points can result in significant efficiency gains and cost reductions.
3. Efficient decision-making with visualised data: Industry 4.0 and IIoT enable the accurate collection of historical data. However, many AI projects struggle with the visualisation of new data. Predictive maintenance and control solutions, can align the control functions of manufacturing lines and equipment with AI processing in real time. The AI Controller can support companies by generating new, rather than historic, data that is time-stamped and easy to visualise. The process of collecting raw data from machines is completely automated, using an AI controller which operates on the ‘edge’ within the machine. This leads to higher data accuracy and consistency. The controller also creates data models from correlation analysis and monitors the machine status based on these models. Without this automation, machine designers and operators would need to invest in developing their own analytical and optimisation capabilities.
4. Sustainable technology: As the world’s population continues to grow, this places an increasing burden on the environment. AI-assisted collaborative robots (cobots) will play an increasingly important role beyond 2020. The aim is to create healthy and safe living and working conditions that cause less harm to the environment. Omron can help companies to achieve more sustainable working conditions in factories with its portfolio of robots and AI. Assembly and disassembly robots have an important role to play here. The new generation of robots can learn from machine operators (sensing). They can collaborate with the cobot (control) on a circular production line. They collect smart and intuitive data from its actions, assess the data using algorithms, advise the operator about the next steps, and implement efficient processes for each changeover (think).
“Solutions that contribute to an integrated, intelligent and interactive manufacturing site are key to Omron’s "innovative-Automation" concept. Together with our customers, we strive to make the efficient and sustainable factory of the future, in which robots, AI and employees work in harmony, a reality,” said Tim Foreman, European R&D Manager Omron Europe. “We continue to pursue remarkable enhancements in efficiency with leading-edge sensing, control and robotics solutions, while putting artificial intelligence into practical use on the factory floor.”
Key Points
Technology controlled by AI can empower machine learning by predicting both product and equipment failure, using data generated by IIoT devices
Innovative control technology can help employees to work alongside robots and machines to achieve manufacturing excellence
Transforming production and implementing AI can help manufacturers to prolong equipment longevity and detect unforeseen events
- Medium payload AMRs
- Big data solutions
- Getting started with smart devices
- Omron’s Flexible Manufacturing Roadshow comes to UK
- Omron’s new N-Smart sensor family
- OMRON appoints Reeco Automation cobot solution partner
- Get more from your production data
- Choosing the best robot for a smart factory
- Flexible application essential for full potential
- The key to sustainable manufacturing
- Industry 4.0 ready
- What operators need to know about IIoT adoption
- Predictive maintenance leader
- The digital future has begun
- The smart future of manufacturing
- Partnership integrates freight & warehouse management
- Secure data handling
- Makes IoT available in practice
- When & where will Industry 4.0 actually happen?
- Simplifying IIoT & product suite understanding