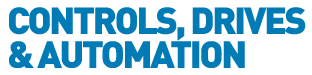
![]() |
Charlotte Stonestreet
Managing Editor |
Home> | AUTOMATION | >Vision Systems | >3D time-of-flight imaging |
3D time-of-flight imaging
08 October 2018
3D machine vision allows precise three-dimensional inspection and measurement of complex free-formed surfaces. Two of the best known techniques are laser line triangulation and stereo vision, but time-of-flight (ToF) imaging opens up a diverse range of depth perception application opportunities.
Time-of-flight cameras feature an IR illumination source, sensor and optics. The illumination source is triggered to emit an intense pulse of NIR laser light. The pulse of light floods the scene, and is reflected back to the sensor from objects within the scene. The camera measures the time taken by the light to reach each point on the object and return to the sensor. As this time is directly proportional to the distance, the camera provides distance information for each image point. Cameras typically have a distance range of several metres. A complete 2D image of the scene can also be captured from the pulses of light using the same sensor, giving both range (3D) and intensity information in a snapshot of the whole scene without scanning. By using short, intense pulses of IR light the cameras can be used in low light and even no light situations, as well as in the prescence of ambient light. However, in very bright situations IR band-pass filters can be used to prevent unwanted light from reaching the sensor.
ToF cameras used in machine vision applications should offer connectivity using accepted standards to ease the development of machine vision solutions. For example, the Starform Swift ToF camera from Odos Imaging, available from Stemmer Imaging, features an industry standard GenICam compatible interface and GigE Vision connectivity. This provides easy hardware integration and the ability to use popular machine vision software packages such as Stemmer Imaging’s Common Vision Blox. This camera has 640 x 480 pixel resolution and can acquire 3D point clouds for imaging at 44 fps from a range up to 6 metres, with a typical depth precision of 1 cm. These fast frame rates can be used to track dynamic scenes in 3D or accumulate data from static scenes for improved precision. A 3D point cloud, raw depth data, a 2D intensity image or any combination can be output giving the user freedom to work with the best data for a given application. The GPIO interface enables individual triggering and synchronisation of multiple cameras.
Smart camera approach
In addition to exporting data to software packages for analysis, there are a number of camera-integrated software packages available. This on-board processing makes it a smart camera which can be used as a self-contained unit for completeness, height detection and box measurement.
ToF machine vision cameras are ideal for a wide range of factory processing, packaging and logistics applications. Carton/object dimensioning and profiling using ToF offer major benefits over traditional laser curtain approaches, as multiple objects may be dimensioned at the same time, allowing increased throughput and utilisation. This approach provides detailed XYZ, orientation and minimum bounding box information about each object. The 2D intensity image can also be used to check the condition of the carton or object for manifest and tracking purposes. By combining 3D and 2D images, ToF cameras can also be used to create robust completeness or presence checking systems for packing containers. Each container can be checked to ensure that it is fully loaded with the correct number of cartons or items before sealing, thereby avoiding costly customer returns.
In logistics applications, high-resolution depth images allow packages and pallets to be rapidly and accurately sorted, dimensioned and profiled. An intensity image from the same sensor can be used for tracking, manifest, security, and recording purposes. Sensor systems mounted on a fork lift can allow for weight and dimensions of target objects to be captured in real-time, increasing the efficiency of the process flow. Distance information from ToF systems can increase the flexibility and efficiency of robot palletising and de-palletising stations, and is particularly suited to mixed load operations. Absolute dimensions and positions can be acquired and used as the input to optimise the utilisation of space in freight transport, as well as allowing efficient unpacking operations, even for pallets that have shifted in transit.
Key Points
- ToF machine vision cameras are ideal for a wide range of factory processing, packaging and logistics applications
- Using short, intense pulses of IR light ToF cameras can be used in low light and even no light situations, as well as in ambient light
- In addition to exporting data to software packages for analysis, there are a number of camera-integrated software packages available
- Stemmer Imaging becomes MTC member
- Scalable machine vision systems
- High speed reading of stamped, etched or printed 1D/2D codes
- Vision Technology Forum registration open
- Special offers on essential equipment for machine vision users
- Vision technology forum
- Highest res industrial TOF camera
- Machine vision software library
- Imaging & vision handbook
- All-in-one 3D smart snapshot scanner for stationary objects
- Turnkey hovercraft drivetrain guarding
- More Ways of Identifying Objects
- HD Machine Vision
- Bespoke Vision Sensor Packages
- B&R NEW WEBSITE
- View Images & Overlay Graphics
- Get A Lock On 3D Measurement
- Entry-level vision system
- Multipix will launch the NEW Datalogic MATRIX 450
- Process, print and packaging inspection systems on show