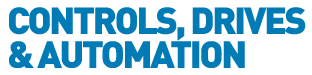
![]() |
Charlotte Stonestreet
Managing Editor |
Home> | AUTOMATION | >Data Capture | >DEEPER INTEGRATION IN THE FOOD INDUSTRY |
Home> | INDUSTRY FOCUSES | >Food & Beverage | >DEEPER INTEGRATION IN THE FOOD INDUSTRY |
DEEPER INTEGRATION IN THE FOOD INDUSTRY
31 October 2012
Mark Staples, food and beverage segment manager of the Industry Business division at Schneider Electric, looks at OEE+E, combining real-time control applications and energy management with production management capabilities
With the food industry facing the issue of ‘green image’, many manufacturers are investigating ways of operating efficiently, flexibly and sustainably, in a bid to reduce carbon emissions and utility consumption. This is coupled with increasing demands on the industry to quickly provide innovative new products to market. Therefore many are looking at achieving what could be termed ‘Overall Equipment Effectiveness plus Energy Management’ or OEE+E, combining real-time control applications and energy management with production management capabilities, creating a manufacturing environment that is cost effective and energy efficient.
A recent report by the EEF revealed that British manufacturing output is set to shrink by 1.5% this year. This, coupled with the increased demand placed on manufacturers to lower carbon emissions in line with Government targets by 2020, means it is imperative that food and beverage manufacturers seek innovative solutions that will help them to overcome both of these challenges.
Within the industry, the term ‘Overall Equipment Effectiveness’, or OEE, is a recognised key measurement of efficiency and is based on three main factors: performance, availability and quality. With the increasing focus on reducing energy consumption, energy management specialists such as Schneider Electric, believe that there is an argument to now include energy within the equation – resulting in what could be termed Overall Equipment Effectiveness plus Energy Management(OEE+E).
In today’s tough economic climate, end-users now expect control systems to go beyond functional and regulatory performance. It has now become a tool to manage the plant while reducing energy and overhead costs, cut carbon emissions and provide quick and precise information that mould both production and business strategies.
Additionally, increasingly complex software, such as Schneider Electric’s Ampla Express, can now be introduced to a plant, enabling end-users to collate all of their energy related data onto a single platform, offering an easier way to analyse energy consumption.
As a way of improving efficiencies, manufacturers should consider automating processes that currently operate manually. By doing so, it is possible to reduce human error and make significant cost savings for the company.
Further to this, automation allows for better repeatability, so particularly for the food industry, both the recipe and the actual production process can be automated and controlled, ensuring that all products look and taste the same every time.
ETHERNET-BASED
Over the past decade, the adoption of Ethernet-based control networks and commercial off-the-shelf hardware, components and operating systems have improved the way the systems in place communicate. This provides endusers with the flexibility, choice and predictability necessary to achieve a truly energy efficient plant. By upgrading to a fully integrated solution, incorporating both the energy management and automation system with the operation management applications, it is possible to make vast improvements to a site’s OEE+E.
Finally, for a food manufacturer to lower running costs while reducing energy consumption, they must employ a flexible automation system that is capable of reacting to increasingly variable energy costs.
The price of energy can vary significantly at different times of the day, as well as geographically. While manufacturers may be using a process automation system to manage energy consumption, if they are using too much energy at the wrong times of the day, both costs and emissions will remain high.
In response to market demand for a collaborative system, Schneider Electric introduced PlantStruxure - a process automation system which includes a range of production management software solutions. Once implemented, a solution such as PlantStruxure can help to keep unexpected downtime to a minimum, lower production costs, and help to ensure that energy reduction targets are met.
This effectively reduces waste and helps companies comply with the heavy environmental regulations which govern today’s food and beverage industry. Businesses that operate an open and collaborative production environment that embraces standards can enjoy significant energy efficiency benefits. It is time for manufacturers to look to a top-down approach to achieving what we can term a high OEE+E rating, to ensure that their systems are flexible, sustainable and energy efficient to withstand the test of time.
Key Points
- Manufacturers are investigating ways of operating efficiently, flexibly and sustainably
- End-users now expect control systems to go beyond functional and regulatory performance
- Savings can be made with a flexible automation system that is capable of reacting to increasingly variable energy costs
- Digital services provide solutions for dynamic workplace challenges
- Software-centric
- Schneider & AVEVA give Flint factory digital upgrade
- Scoring sustainability goals
- Schneider Electric acquires Itris Automation Square SAS
- Smart from the start?
- Schneider appoints new VP for Secure Power division UK&I
- Adding AI to process safety
- Smart factory role for cobots
- Schneider donates €1m to Factory of the Future