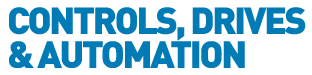
![]() |
Charlotte Stonestreet
Managing Editor |
Distribution centre automated
07 October 2021
TOYOTA MATERIAL Handling and Interroll, have installed a powerful and efficient conveyor system for Imnasa in Campllong near Girona, Spain. Core components of the new material-handling solution are the Modular Conveyor Platform (MCP), the RollerDrive EC 5000 and the MultiControl from Interroll.
The state-of-the-art system, which spans around 360m, automates the flow of goods between two buildings, increases productivity, and improves customer service as well as the working environment of the personnel deployed.
The automated conveyor system for Imnasa was fully designed and installed by Toyota Material Handling. Imnasa manufactures and distributes nautical equipment from numerous brand manufacturers to businesses and private customers. With a range of over 30,000 different products, it is one of the leading players in its sector in Europe.
The starting point for the new solution was the construction of a new building complex of 9,000 square meters expanding the capacity of Imnasa’s distribution center. To seamlessly integrate the different work processes within the already existing and new buildings, the two sites were connected by a 360-meter-long conveyor system in a tunnel. Using a zero-pressure-accumulation material-handling solution, the diverse goods are thereby automatically routed between the picking area in the existing building via the respective packing stations to the shipment area in the new building.
"The new solution has not only enabled us to significantly increase the capacity and productivity of our distibution center. We have also succeeded in further increasing customer satisfaction through faster and more reliable deliveries. In addition, the new solution now offers our employees significantly improved work ergonomics," explains Pol Revuelta, project manager at Imnasa.
A total of around 250 EC 5000 RollerDrive and 120 MultiControl from Interroll are used for the energy-saving transport of boxes and totes via driven roller and belt conveyors.
"Thanks to the excellent and smooth cooperation of all parties involved, the entire project—from planning to commissioning—was realized in a short time. The quality and modular flexibility of the Interroll products as well as the commitment of the Interroll experts involved played a key role in this success," reports Ana Lorente, project manager at Toyota Material Handling.
- Modular conveyor platform
- New MD at Interroll UK
- Interroll establishes new service organisation
- Interroll appoints pallet handling expert
- Hygienic drive solutions for the food industry
- Easy-to-integrate drive solutions
- Controls descending product speeds
- Powerful synchronous drum motor
- Innovative drive solution
- Synchronous drum motor
- No related articles listed