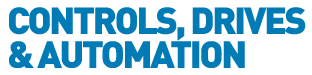
![]() |
Charlotte Stonestreet
Managing Editor |
Editor's Pick
Drive to greater motor efficiency
05 December 2018
With increasing evidence indicating global warming, perhaps industry should be accelerating its adoption of the best of currently available energy efficient technologies, asks Brian Bannister, motor specialist at LaFert.
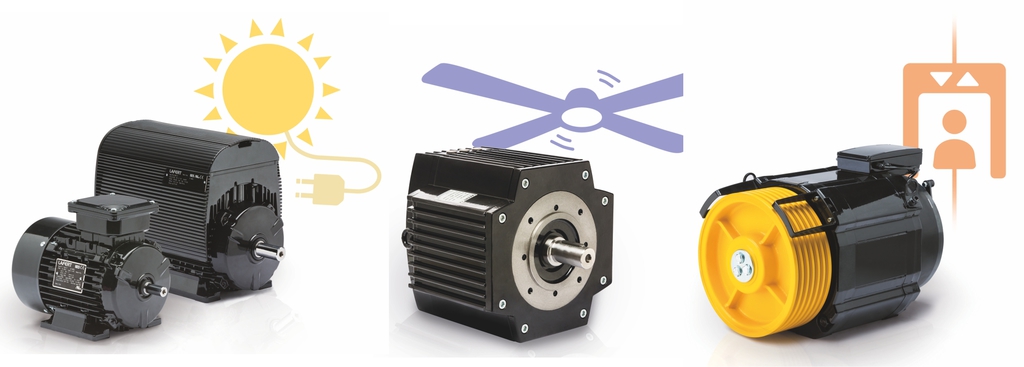
With regards to electric motors, a Draft ISC Revision published in July 2018 required the use of IE3 standard motors (0.75 to 1000kW) from January 2020. Yet motors achieving IE4 and IE5 efficiencies have been available for years and have been proven in the field. These motors have demonstrated particular suitability for continuously running items such as compressors, fans, pumps, lifts, escalators and conveyors.
Increasingly, industry is adopting these IE4 and IE5 motors with many industrial machinery manufacturers now incorporating them as part of original equipment. The attraction is clear when some in the market claim energy savings of up to 20%.
With increased efficiency of this level, the minimal additional cost incurred from specifying IE4 or IE5 motors could be recovered rapidly, followed by on-going savings potentially amounting to thousands of pounds a year, depending on motor usage. It could be considered as a ‘win-win’ situation with the end user reducing costs, lowering emissions and benefitting from a significantly more efficient system.
Very few buildings today do not have HVAC systems installed and these could benefit considerably from the use of IE4 and IE5 motors with many operations requiring continuously running motors. Incorporating elements that are ideal for these motors – compressors, pumps and fans – energy savings (and reduced costs) would soon mount up.
Lafert’s IE4 and IE5 motors are based upon permanent magnet motor technology. When this technology is used there are the additional benefits of both weight and size reduction. Weight reduction can be up to 50%, whilst a motor can be two frame sizes smaller than the standard asynchronous alternative! These features in turn potentially result in the need for less robust mountings and fixings being required for the motors, thus further reducing the weight and size of the installation.
Amongst Lafert’s permanent magnet high efficiency range are even versions developed specifically for large diameter fans and lifts – commercial and domestic.
Lafert’s motors for large ceiling fans (up to 7m) are typically employed in large areas within buildings, such as auditoriums, shopping malls, airports and sports arenas. They eliminate the need for gearboxes, can reduce energy consumption by up to 50% and minimise operating noise.
As well as offering energy efficiency, the company’s permanent magnet motors for lifts are designed to eliminate the space and high maintenance challenges of conventional electric motor/gearbox and hydraulic systems. Depending upon elevator load, these gearless motors are said to provide energy savings of between 45 to 70%.
Further, due to their compact design, smaller sheaves and light weight, they can be installed in the lift shaft without impeding lift car travel, thereby eliminating the need for a machine room. This in turn enables buildings to take lifts to an additional floor.
Permanent magnet motors provide one of the simplest ways of reducing emissions whilst at the same time offering technical benefits and potentially significant financial savings to the end user. All powerful reasons to seize the future now!
- Stainless motors
- New premises enhance service
- The route to energy saving efficiencies
- Energy, weight & space saving
- Stainless motors enhance hygiene & cut running costs
- Energy & weight saving
- Innovative drive technology for AGVs
- Compliant motor solutions
- Brake Motor For Power Failure
- Stainless steel motors