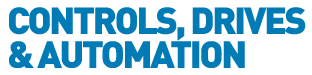
![]() |
Charlotte Stonestreet
Managing Editor |
Home> | AUTOMATION | >Handling & Logistics | >Food for thought |
Editor's Pick
Food for thought
14 February 2024
BARA chair George Thomson chews over some food and drink sector challenges

AS MOST of us are aware, food and drink is our largest industrial sector by a considerable margin and has both similar and different manufacturing challenges to other market sectors. One of the biggest challenges that I hear on a regular basis is the lack of suitable operatives available in the employment pool. I think those of us in the Automation industry can give a different perspective on how to solve those resourcing issues, as well as improving efficiencies and traceability at the same time.
I’m sure by now, every manufacturing company is aware of the relatively quick wins around the end-of-line solutions, however there are numerous options available throughout the manufacturing process. For example, I have lost count of the production facilities where totes were being manually filled and then pushed around to the next process, then manually emptied into the next vessel. Another way to approach this would be to use simple flow control automation to dose the product into a tote, which is then collected by an AGV/AMR and taken to the next process where again we use simple automation to automatically decant into the same vessel.
Another example would be lifting bags, buckets, or boxes of ingredients to decant into mixing vessels. These ingredients could be brought to the lineside by conveyors or AMR/AGV and then using food compatible robotics to effectively depalletise and decant. This is a process that is already used in the plastic industry for feeding Injection Moulding Machines, so it would be repurposing an existing solution from one industry sector to another. Yes, there will be some changes made to robot type and perhaps the gripping technology may need to be modified to suit the high care environment, but the bones of the solution would be VERY similar.
Make the connection
If we now couple these examples with one of my favourite topics, which is connected manufacturing – also described as Industry 4.0 – which is FAR more than just data. If the facility is connected as a cohesive manufacturing system, each production area can work together for smooth production flow. What this means in practice is that if there is an unplanned stoppage in one area, the upstream and downstream processes can slow down to allow for the unplanned stoppage to be rectified. Yes, the data is collected by the control system to allow for a root cause analysis to be carried out, but more importantly the production itself can balance itself to match the flow.
Why is this important you may ask? Simply speaking, it helps to reduce the ‘feast and famine’ that is created by suddenly having to stop production due to the back-up caused by the stoppage downstream, or the starvation caused downstream by the same stoppage. If I’m honest, this is exactly what I see when I visit a factory that wants me to look at a specific process that has been identified as the problem area. It is likely to actually be upstream or downstream of this process where the actual issue lies.
Examples like these are evident throughout our industry and are some of the many reasons that I am an advocate of going to a wide range of trade shows, even those not in your market sector, to see how other areas are approaching similar manufacturing challenges.
If you would like to start your automation journey, but don’t know where to start, I would highly recommend visiting the BARA website where we have outlined several topics under the Expert Advice section to give some initial information. Whilst you are there, why not register for our next Roundtable discussion or catch up on a previous session?
- High Demand For Grant
- Automation UK 2024 doubling in size to meet exhibitor demand
- Making the connection
- A fond farewell
- RMGroup becomes the UK’s first certified robot integrator
- 3D elimination
- Not all integrators are created equal
- Cross pollination to drive down cost
- Bringing industrial automation to life
- Automation influences