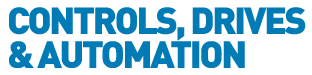
![]() |
Charlotte Stonestreet
Managing Editor |
Maintenance in the era of 4.0 - it's still all about the people
03 May 2019
Sponsored by Festo, as part of Maintec 2018 Controls, Drives & Automation hosted a round table discussion on the development of Maintenance 4.0 systems for predictive maintenance. The event attracted a range of lively and knowledgeable attendees; chair Andy Pye reports on the insightful session
Few things can damage the financial stability of a manufacturing facility more than unexpected downtime. On average, manufacturers suffer with 30% or more downtime during their scheduled production time. In some industries, such as automotive assembly, downtime can cost up to £17,000 per minute (a mind-blowing £1 million an hour).
The penetration of advanced maintenance engineering practices within UK manufacturing is patchy. Many companies still operate a breakdown maintenance system and the available technologies are not being used effectively.
On the evening of the first day at Maintec 2018, and shortly after the close of the exhibition, we held a behind-closed-doors Round Table Discussion involving invited key senior maintenance specialists from users and suppliers in the engineering sector.
Around the Table
In-house:
Andy Pye, Consulting Editor, Controls, Drives & Automation
Charlotte Stonestreet, Editor, Controls, Drives & Automation
Lee Hibbert, Consultant, Publitek
Guests
Richard Kelly, Managing Director, EMS Cognito (Presenter)
Steve Worth, Sales Manager, Klüber Lubrication GB (Presenter)
Jon Moody, CEO, SSG Insight
Prof Jyoti Sinha Programme Director, Reliability Engineering and Asset Management (REAM), University of Manchester
Andy Kidd, Chief Engineer, British Engineering Services
Phil Owen, Managing Director, SPM Instrument UK
Geoff Walker, Director, Faraday Predictive
Stephen Lewis, Consultant, Rail Technologies, British Steel
Nanoo Patel, Consultant Engineer, Tiara Machines and Systems
Karl Redmond, Associate, Rider Levett Bucknall
John Benjamin, Novotek UK & Ireland, Glasgow
Jon Hill, Business Development Director, INVMA
Lee Roberts, UK Sales Manager - Industry/Utility, DESMI
Marcus Halliday, Distribution Director, EMEA, Europe and Middle East, Cordex Instruments
The key theme we explored during the session was Overall Equipment Effectiveness (OEE). The discussion considered the effect on OEE of predictive maintenance, including the advent of Industry 4.0 devices, and how these concepts are being taken up by the SME community in the UK.
But first, some background….
Reactive maintenance
Reactive maintenance - also called emergency or breakdown maintenance - is the process of using equipment as much as possible without spending any further money that its cost price. Maintenance is avoided, servicing and checks are not ordered and temporary repair or quick fixes are made in order to reduce ongoing maintenance costs and spend only when absolutely necessary. Reactive maintenance ignores any preventative measures and simply deals with a problem or issue when it is reported. Under these circumstances, it is not possible to match stoppages to out of hours periods.
Preventive maintenance
Traditionally, maintenance has been done on a fixed schedule, replacing items at constant intervals. The price of downtime due to malfunction can be much higher than a good maintenance regime. In many cases, preventative maintenance is the smart economic choice. Even small improvements should result in significant benefits. This approach is less time-intensive than a regular inspection regime and can significantly improve the use of maintenance resources.
By planning, servicing, making regular checks and replacing parts when recommended, a preventive maintenance approach limits unexpected problems and aims to reduce long term expenses through avoiding unanticipated issues.
But although the intervals are usually based on established knowledge, and in many cases accelerated testing at the parts manufacturer, parts wear out at different rates for all kinds of reasons. Constant intervals do not take into consideration the unique and varying circumstances of a machine being maintained. So although general purpose schedules are easy to manage by arranging for spares to be delivered in a predictable manner, they risk wasting money by replacing parts that are still operational.
Preventive maintenance schedules rely on schedules provided by a machine’s manufacturer, to regularly replace machine components based on a suggested timeline. However, these timelines are only estimates of when the machine will require service, and the actual use of the machine can greatly affect the reliability of these estimates.
Predictive maintenance & machine learning
Predictive maintenance is about getting the most life out of equipment while minimising the risk of failure. It ensures that parts are used to the end of their natural life, but risks downtime due to delays in delivery of replacements or additional costs due to higher stock levels. The ideal combination is predictive maintenance with just-in-time supply chains.
As plants become more automated, monitoring technologies will be ever more integrated into the manufacturing process. Predictive maintenance is the process of tracking the performance of crucial machine components, such as motors, to minimise downtime needed for repairs. It enables users to more accurately anticipate when machine maintenance will be needed based on real-time data from the machines themselves.
Airbus has indicated that data diagnostics could put an end to aircraft unscheduled grounding for fault repairs around 2025, supported by big data and operational experience. In principle, the approach can tell that some parts do not need a scheduled check, but a full transition to this model will need much greater experience, because some unplanned downtime may be beyond the control of a manufacturer – caused by infrastructure failures, human error or even natural catastrophes.
Predictive maintenance is becoming synonymous with the smart factory. The ability to accurately track machine performance and anticipate failures before they occur is helping manufacturers improve overall equipment effectiveness and reduce wasted time and costs. A leading solution for predictive maintenance is condition monitoring; however, collecting machine performance metrics is only the beginning. To accurately interpret and communicate this data is essential for system reliability, and that’s where machine learning comes into play. A condition monitoring solution with machine learning removes human error from the equation and makes predictive maintenance solutions smarter and more effective.
What is OEE?
At the Round Table Discussion, Richard Kelly, Managing Director of EMS Cognito, set the scene, with a brief presentation on OEE.
OEE stands for Overall Equipment Effectiveness. It takes into account three aspects of the manufacturing process – Availability, Performance and Quality. The result is expressed as a percentage. An OEE score of 100% is perfect production: manufacturing only good parts, as fast as possible, with no stop time. An OEE score of 85% is considered world class for discrete manufacturers. Table 2 lists the six major losses which contribute to reduced OEE.
Automated machinery can dramatically increase effectiveness by speeding up production time and reducing the potential for human error, therefore increasing OEE. The fourth Industrial Revolution (Industry 4.0) is ushering in a new approach to maintenance activities, offering as it does, the ability to measure parameters at the coalface, and pass that data, remotely if needs be, for analysis. How will digital technologies underpin continuous maintenance? The more data that is obtained over time, the more confidence can there be in the predictions made, and this helps with planning maintenance schedules and the logistics of having spare parts available at the right time.
Kelly illustrated the progress one industry had made in improving the OEE of its machines by comparing tyre changes in Formula 1 racing, which has improved from 67s in the 1950s to 2.5s in the modern day. Interestingly, Andy Pye noted, how the number of people involved has increased dramatically!
Very often, said Kelly, poor OEE reflects not the machine failing, but a failure to understand the underlying system. In his experience, people involved in condition monitoring often don’t understand the process they are meant to be maintaining and keeping reliable. An excuse which is often used is that a plant is not reliable because the plant is old; however, this is only relevant in 11% of cases. In the other 89% of cases the real reason is that the organisation is doing something wrong and correct procedures, which reflect understanding the process have not been put in place. The importance of procedures is also highlighted by 68% of failures being due to human error.
Therefore, achieving high OEE depends on getting management teams to understand there is waste in any process and getting the buy-in of the operators. Data reveals lots of things about problems and looking at rejects is a fantastic opportunity for data analysis – let the process conditions inform when to intervene in the machine and not the calendar!
It is important to learn from industries at the forefront of best practice. The term "reliability-centred maintenance" (RCM) was first used in public papers authored by Tom Matteson, Stanley Nowlan, Howard Heap, and other senior executives and engineers at United Airlines (UAL) in 10978 to describe a process used to determine the optimum maintenance requirements for aircraft.
RCM is used to establish safe minimum levels of maintenance, changes to operating procedures and strategies and capital maintenance regimes and plans. Successful implementation of RCM will lead to increase in cost effectiveness, machine uptime, and a greater understanding of the level of risk that the organisation is managing.
Choose the right lubrication
Steve Worth, UK Sales Manager of Kluber Lubrication, offered the second short presentation, this one on the practical and down-to-earth issue of lubrication.
As part of an overall maintenance strategy, Worth highlighted how lubrication programmes play a significant part in improving OEE, regardless of whether the customer operates TPM methodology or more traditional strategies. It is vital that components such as bearings are lubricated sufficiently and to a suitable fill level dependant on torque, speed and load requirements. Equally the type of lubrication should be carefully considered for the application, based on temperature, speed and environmental conditions.
If parts are inadequately lubricated, or filled with an incorrect grease, maintenance problems will surely follow. The correct choice and application of well formulated lubricants assists the effectiveness and efficiency of capital and human resources, whilst extending maintenance intervals and maximising asset life. It has less of an effect on slow running and stops, which are usually due to other factors.
Indicators of problems can be identified by studying planned maintenance intervals, unplanned maintenance incidents and component rejects. Often, these can be traced to a lubrication problem. It is possible to monitor lubrication cleanliness and acidity online and remotely, while another indicator of problems, metal particles in the oil, is usually measured by sampling, because a ferrograph does not tell the whole story.
Correct lubrication practice not only means using the right lubricant for the application, based on understanding the speed, temperature and environmental conditions, but also making sure it is correctly applied. For example, attempting to lubricate a chain while it is under tension makes it impossible to lubricate the links and pins. Bearings and chains can also be killed with kindness by over-lubricating them, which can introduce new hazards, including contamination and floor spillages.
Kluber and other lubricant suppliers will do a lubrication audit, where the company will come in and look at the whole plant, inspecting every machine, and recommending a lubrication regime. Most offer a dedicated lubrication management tool, such as Kluber’s Efficiency Manager, often taking data out of the system to be stored in the cloud. This is especially useful when working remotely, such as with a fleet of ships which could be anywhere in the world.
Returning to OEE, Worth cited an example of an aerosol manufacturer who had to stop production for six hours every three days. This equates to 600 hours of lost production per year, which at £1750 per hour equates to over £1 million.
The solution was to put in a more appropriate product than the poorly formulated grease which was being used. This enables a move to monthly inspection, saving 90% of the downtime, saving just under 550 hours of production per year.
In this example, the change was driven by the engineering manager – he gained a £1 million of production for an outlay of 2kg of grease per year – although this did not stop the purchasing department asking for an improved price on the new lubricant!!
In terms of OEE, this simple change alone represents a 7% improvement in OEE, from 91.7% to 99.3%.
Lubrication improves OEE
Manufacturer of Aerosol Cans
Current re-lubrication interval every 3 days maximum Removal, strip down, re-lubrication and refitting the heads is 2.5 hours per machine Alignment of heads following re-lubrication is 30 minutes per machine Production is 50 weeks per year 6 days per week – 2 weeks shutdown Value of lost production is averaged at £1,750 per hour
Current time spent on lubricating Seaming Heads is 6 hours every 3 days which equates to approximately 600 hours per year Current value of lost production relating to the lubrication of Seaming Heads equates to 600 hours x £1,750 = £1,050,000
Result of lubricant change
Re-Lubrication interval increased from 3 days to 35 days Time spent on lubricating Seaming Heads reduced from 600 hours to 51 hours per year Lost production cost relating to lubrication of Seaming Heads has reduced to 51 hours x £1,750 = £89,250
Additional 549 hours per year machine availability per year A saving of £960,750 in lost can production Lubricant quantity reduced by over 90% Engineers have 549 additional man hours to carry out pro-active maintenance
Current Situation
Assuming: No additional downtime, No slow start losses, No quality losses Planned Production = 7,200 Hours Actual Production = 6,600 Hours OEE = 91.7%
New Situation
Assuming: No additional downtime, No slow start losses, No quality losses Planned Production = 7,200 Hours Actual Production = 7,149 Hours OEE = 99.3%
Increase in OEE = 7.6%
Involving the Full Team
Andy Pye challenged the participants to discuss what are the barriers to making maintenance improvements happen? How easy is it to involve an operator/ What skills and training are needed?
Jyoti Sinha (University of Manchester) argued that the key is understanding how the machine works, and therefore involving the operator is vital. Despite automation and smart factories, people remain the cornerstone of the plant of the future. Concepts such as OEE can be seen as too abstract to operators working on the shop floor.
A good maintenance strategy is very dependent then on involvement of the whole team. At the beginning of the project the designers have a massive influence on overall life cycle costs, so most of the decisions that influence the reliability of an asset are locked in early in its life cycle, and at the operational phases there is less and less opportunity to influence the life cycle cost through maintenance related decisions. Sometimes 80 to 90% of the life cycle decisions about the asset may be committed, “locked in” before the equipment reaches commissioning.
At the operational end of things, decisions have already been made that influence reliability, maintainability, replacement life and essentially output or service levels.
Technicians should get involved in purchase decisions, suppliers in operational decisions, and service engineers in spare parts logistics and reliability improvement. Operators should be part of the maintenance planning and execution at the basic level.
Management’s job is to be close to employees to help them develop their skills. Good record keeping is essential, so regular record audits are needed to check on quality. Maintenance workers tend to be hands-on people, so they are not always enthusiastic about completing piles of paperwork.
The goal of digitisation is to improve agility and responsiveness at strategic points in the process: tracking components for maintenance, managing consumption (raw materials, energy, etc.) and ensuring traceability of parts right to end users. It covers all areas of the plant.
The digital revolution supports and connects management at all levels. From employees to plants managers, everyone benefits from new technology. Digital technology aims to provide tools based on how things are really done on the job. The tools make work easier. They are more connected and collaborative, easier to use and more mobile – in short, more efficient.
Skills
These changing roles for the maintenance function mean that the skillset required for the maintenance engineer has changed, with new skills required, and some older ones - arguably - less important. As in all engineering disciplines, and in the light of proposed changes in the political landscape, the UK faces acute skills shortages.
An additional difficulty faced by some sectors is that these skills – typically science, engineering, and technology related ones - are in high demand in other sectors, and therefore it needs to identify how it can develop its own talent pipelines if it is to match performance levels in competitor countries.
John Benjamin (Novotek) observed that the input of operator observation remains extremely important alongside the sensors and systems of Industry 4.0. Human data forms a big part of the data set. But human failings are also important, so can be enhanced by the use of phone apps. QR scanners can be used to transmit a grease code, for example. This is not advanced machine analytics, but basic stuff, even though the data can be transmitted via the cloud using Industry 4.0 methods.
Worth commented that such aids free up the engineer to do other maintenance tasks. We need to upskill operators, despite techniques like colour coding and mistake-proofing generally. Today, auto-lubrication is often employed to minimise intervention, and records kept of the “what, where and when”. Comments about noises, smell and vibration are really important and all operators come equipped with two eyes, two ears, a nose and a mouth – perhaps the best condition monitoring sensors of all!
Benjamin said that people should not expect a magic show from condition monitoring. It will give you some benefits, but people are absolutely vital. An analogy is the car driver, who will check oil, water, lights and tyres, alongside the need for regular MoTs and services. Most failures come with some sort of warning. Operators know when something is going wrong.
However, he added, while people often think that what they are doing now is the best they can do. This mentality would have us flying Sopwith Camels!, But machines have no agenda, and unlike people, their data can be used for engineering, financial or reliability purposes. Equipment such as spinning devices often show signs of failure long before you can detect them with eyes and ears. Industry 4.0 is the means of getting machines to yield their information. Then the financial director can see the beneficial impact of condition monitoring on the machine.
It is vital to get people to think "can we be better" - how do we know how good we are compared to our competition? In the post-Brexit world in full glare of global manufacturing with China, India and elsewhere, people who have lower costs bases or are simply smarter and have better products will have a major advantage.
In practice, the takeup of risk-based inspection is not where it needs to be, even though pressure systems regulations allow for it. Lifting equipment rarely uses it, preferring instead 6 or 12 month maintenance intervals.
Karl Redmond (Rider Levett Bucknall) commented that the barriers to training and CPD need senior management engagement. It is important to get buy-in using return-on-investment (ROI) justifications to backup the vision, which needs to be articulated up and down the management chain. He added that maintenance often turns into a series of Ponzi schemes which refuse to share any data – transparency and an appreciation of common attributes are essential to address this.
Sinha agreed that Industry 4.0 gives the platform, but education and understanding of the machine is still important – the ability to look into a machine to find the reason for a failure. That local level of machine knowledge is still important. Machines themselves are becoming smarter and can teach industry professionals themselves, but operators still struggle with some elements, including software changes, where training is still needed.
Nanoo Patel (Tiara Machines and Systems) took that point further by referring to the “us and them” barrier to knowledge sharing. In his experience, operators are often pushed aside, and can equally hang onto information they know, despite knowing the machine best. It is important to give the “ownership” of the machine to the operator – make it up to that person to call for maintenance. This approach works brilliantly, and is much more effective than the responsibility falling to somebody sitting remotely and trying to play with data.
Sinha agreed. “This is 100% right - to do the maintenance you need to know *what* and *where* to put the maintenance, not rely on trial and error.”
Benjamin also agreed. “Industry 4.0 is knowledge-heavy at all levels,” he stated. “You have to know what you are doing, even to torque a bolt or apply a grease. You can have a smart tool which shows what it was taught to do. Even operators on equipment like GE’s aviation gas turbines, which are instrumentation heavy, need to know the fundamentals of fluid dynamics, thermal engineering, and the materials of construction. Machine learning is not replacing people, but about giving them better tools and better information to find out what happened immediately before or is about to happen.”
He drew the analogy of a smart phone – Siri and Alexa and the others cannot think originally outside the box like human beings can. They cannot manipulate and use knowledge like human beings. So Industry 4.0 is a human revolution, not a machine revolution.
Lee Hibbert interjected and asked how we should take people forward. By taking all this data off a machine. will operators end up drowning in data. How difficult is it to democratise that data?
Redmond said that the key issues are what information, what questions, how is it captured, what will be the cost, how long will it take. Not all people in senior management positions have the cultural nous to pass responsibility down the chain. People both at the top and bottom have to understand what this is for, and if they do, 99% will buy into it.
Hibbert asked if the age profile within engineering is a barrier in being able to break down that cultural issue. Redmond agreed: “Culture comes with so many problems at the top of the tree – we need to start joining up the dots and benefits.”
Charlotte Stonestreet asked if this cultural problem is a British issue. If we compare investment on automation and Industry 4.0 in the UK compared to other countries, including the EU, we seem reticent to make the leap.
Jon Moody (SSG Insight) quoted research he had done with Sheffield Hallam University. “Post-Brexit we will be operating in a global world and we will be exposed to a much wider cultural change – Industry 4.0 data is an enabler in the way we do business – something we will need to compete as an engineering country with China and India. These countries do not have the cultural heritage (or is it baggage?) of our organisation cultures and they can start with an open mind. Karl Redmond is absolutely spot on – we can meddling around in operational issues, but success is fundamentally down to how we make the organisation work better.”
Patel said that if we are not very careful, Industry 4.0 can blow up in our face - how do you sell it to the ground level? It is in danger of being regarded as another Big Brother – a disease in British industry of pitching productive against non-productive. We must not be afraid to give the individual some responsibility and pay for it at the ground level. Slapping monitors on the shop floor and having them operated by the guy sitting in the office is not the way forward.”.
He added that we must help companies to be competitive. My best customers are those where the operators on the shop floor love the machines. Management must be open and honest or a level of mistrust will emerge.
SME involvement
Most larger companies do take advantage of modern maintenance practices and technologies to improve their production responsiveness and flexibility. However, SMEs have been largely slow to implement such strategies. Traditionally, many SMEs are unaware of advances in engineering and maintenance methods and are reluctant to embrace them to improve their production process and competitiveness.
At a similar event in 2016, the slow uptake of the SME community of Industry 4.0 technologies was highlighted: at the time, Chris Greenough, Commercial Director of Salop Engineering, a manufacturer of pressings and assemblies based in Shrewsbury, and President of Shropshire Chamber of Commerce, said: “Digitisation has been pushed through the large OEMs and First Tier companies and that hasn’t filtered down to the SMEs. Yet, this is where the biggest potential improvement is.”
How have things changed since? Unfortunately, while 80% of UK manufacturers say industry 4.0 will be a reality by 2025, only 11% expect to be ready to capitalise on it, according to information recently released by the recently launched Green Technology Task Force i(London, 12 September 2018).
- 2022: a watershed year for AI adoption
- Mapping out automotive developments
- Call for accelerated robotics adoption
- SPS - bringing automation to life
- Nearly 100,000 exposed industrial control systems indentified
- Construction begins on National Robotarium
- UK manufacturing output & new orders fall at fastest rates since 2012
- Change is on the menu
- Hitachi, Fanuc and AI startup to form automation joint venture
- Leading manufacturers join Venturefest North West line-up
- No related articles listed