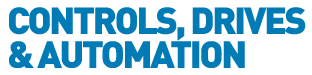
![]() |
Charlotte Stonestreet
Managing Editor |
Home> | AUTOMATION | >Sensors | >Minimising complexity in industrial automation |
Editor's Pick
Minimising complexity in industrial automation
26 February 2021
Recent developments in Industry 4.0 and the impact of Covid-19 have quickened the pace of adoption in industrial automation, with greater networking and higher sensor numbers facilitating ever-closer process monitoring. However, these trends do not necessarily need to lead to greater system complexity in signal acquisition, connection technology and cabling report Stefan Schumacher and Dominik Grzesiak
(Source: Shutterstock)
The development of Industry 4.0 technologies continues to accelerate at a rapid pace. Technologies such as Artificial Intelligence (AI), 5G, advanced sensing, advanced materials are bringing enormous and irreversible change today – which will, in turn, significantly accelerate transformation processes in industrial automation.
Meanwhile, the growth in autonomous manufacturing, especially the transition to the fully automated 'lights out' factory, requires automation and networking of all areas of manufacturing processes, furthering the adoption of these technologies.
To support these developments, manufacturing plants worldwide are set to replace conventional Fieldbus networks with Ethernet-based versions to leverage at field level the benefits of Ethernet – namely reliability and accessibility at an attractive price point.
The next phase will see companies move away from centralised, top-down control in favour of distributed control architectures with embedded safety and security – moving safety, processing and intelligence closer to the point of need and allows dynamic real-time processing.
Greater intelligence within each device eliminates the need for costly central controllers. Distributed control, with real-time machine-to-machine (M2M) communications and connectivity to enterprise applications, is set to drive a paradigm shift in the industrial automation world.
Robotic process automation
Many developments in digital transformation have been intensified in pace by the COVID-19 pandemic, especially in Robotic Process Automation (RPA). A recent study by Forrester Consulting, entitled The Future of Work: a Pandemic Spotlight, notes that organisations are unlikely to just go back to the way things were before when the pandemic: “Once the pandemic passes, which it eventually will, organizations will see structural changes to work. In fact, with so many people already working from home, employees and enterprises must reshape how they conduct themselves. Automation technologies have emerged as an invaluable asset for organizations to tackle this new world.”
To support this, extensive innovations in monitoring systems are under way, allowing organisations to gather more data to inform operational decision-making, generate new ideas and support new product development.
To support diverse goals such as more flexible manufacturing processes, automated control of material replenishment, and enhanced machine fault prediction, complete solution packages with sensors, connectors, cables, distribution boxes and software modules can help reduce industrial automation complexity.
As a specialist distributor in this area, Heilind offers products from more than 170 manufacturers. Here, the company highlights two examples illustrating how such solution packages can deliver important advantages.
One example is a level sensor used for monitoring the content of a tank. At the customer facility, if the content level dropped below a set threshold, an alarm lamp would illuminate and an employee would replenish the tank from the warehouse and, if necessary, order additional material during procurement.
Today, the process is very different, with the level sensor connected to a digital process chain. Now, if the contents of the container fall below a pre-set threshold, the signal is transmitted to the controller, with an automated order triggered via the ERP system. Not only are the signals from the level sensor transmitted to the controller, but so are the temperature, pressure and flow sensor values. In total, 30 sensors have been installed on pumps and along the supply pipes, monitoring the entire process.
The sensors are wired with an M5, M8 or M12 connector suitable for the harsh environmental conditions of an outdoor tank, while motors are connected with rugged M23 connectors.
Instead of many individual cable connections to the controller’s PROFINET bus, adjacent sensors and motors are connected to a distribution box at the nodes. Here, the signals are bundled via a cable and routed to the master box, from which only a single cable leads to the controller. Cabling and assembly costs were therefore cut significantly.
Instead of individual cable connections to the PROFINET bus of the controller, adjacent sensors and motors are connected to a distribution box at the nodes. Here, the signals are bundled via a cable and routed to the master box. Only one cable is required from the master box to the controller. (Source: Molex)
Typical components for monitoring
For the connection of sensors and motors for this type of application, manufacturers like Molex and Amphenol supply complete packages featuring connectors, cables, distribution boxes and master boxes, with variations for differing environmental conditions. Some manufacturers also offer software modules and development services for actuator control.
The LS02 level sensor from Standex Meeder, for instance, can be offered with normally open, normally closed or changeover contact types, delivering maximum rated power of 100W (400VDC/1A). This sensor can also be connected to a digital processing chain to trigger an automated order.
The LS03 level sensor from Standex Meeder can be connected to a digital processing chain to trigger an automated order. (Source: Standex Meeder)
Further innovation examples include the M12 connector range from Molex and M5 connectors from Norcomp, both designed for harsh environments with their waterproofing and extreme temperature attributes.
Robust M5 connectors from Norcamp are ideal for harsh outdoor environments (Source: Norcomp)
Heilind can also provide solutions such as the Molex Brad HarshIO digital module distribution box for PROFINET, as well as PC interface cards and PROFIBUS cards like the Molex SST PB3 in-chassis module for Rockwell Automation CompactLogix control systems. Among further offerings are TE Connectivity 98RK-1 scanner interface racks, providing power and communication for up to three external NetScanner system components. In addition, TE 9816 intelligent pressure scanners for rack mounting use a high-performance switch enabling them to communicate with a host computer via an automatic 10/100/1G Base-T Ethernet interface.
The HarshIO IP67 I/O distribution box from Molex combines up to eight sensor signals to simplify cabling and installation. (Source: Molex)
Robotics & manufacturing processes
A second example is using sensors in manufacturing processes, where there is usually little space for additional components, making physical wiring highly challenging. If, for example, a robotic system is to be monitored, the smallest possible sensors are typically used, with the signals transmitted by RF.
Sensors monitor the manufacturing process and register the status of the machines and systems. If, for instance, the pressure in a hydraulic line drops, this can indicate leakage. The changed sensor values trigger an alarm and a technician is automatically informed.
Components for system monitoring
Among Heilind offerings for such applications is the CD9515 torque sensor with speed measurement from TE Connectivity, with a 5 to 1000 Nm measuring range.
The same manufacturer offers a position sensor for tilt detection: the DOG2 MEMS series with CAN J1939 output. This two-axis inclinometer has a measuring range of ±90°. Meanwhile, the TE Connectivity U5600 pressure sensor for hydraulic pipes is ideal for measuring liquid or gas pressure, even with difficult substances such as contaminated water, steam or slightly corrosive liquids.
Heilind can refer customers to many new connector developments, including those based on multi-function interfaces and high signal densities on small layouts. Further innovations of note include those for high reliability and continuous loads, alongside others with hermetically sealed and IP68 protected interfaces, or solutions offering more than 10,000 mating cycles.
Stefan Schumacher is product manager, and Dominik Grzesiak, team leader product management, Heilind Electronics Europe
Key Points
- Can mobile robots help mitigate the skills shortage?
- Human resolution tactile sensor
- 3D printing - no threat to automation?
- Solution for integrating self-driving cars into real traffic
- Autonomous robots on offshore platforms
- EU targets high frequency drives
- SPS – bringing automation to life
- Perfect packaging – a recipe for success
- Are you ready for the changes to EU Authorised Representatives?
- HIMA Group acquires Sella Controls