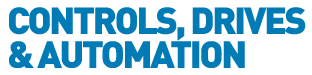
![]() |
Charlotte Stonestreet
Managing Editor |
Home> | INDUSTRY FOCUSES | >Printing & Packaging | >Perfect packaging – a recipe for success |
Perfect packaging – a recipe for success
27 June 2014
Better packaging means that millions of people are gaining better access to medications and food. Today, a third of the world's food still goes to waste, often as a result of inadequate packaging and storage. CDA takes a look at the issues and how they are being addressed
Primary packaging is the most challenging task in the packaging industry. In these machines, the packaging material meets the product at the highest possible speed; as a result, the level of precision has a direct influence on both product quality and the usage of raw materials.
At Interpack 2014, Bosch Packaging Technology introduced its biscuit packaging line, its new features demonstrating the direction which the packaging industry is taking. It is capable of slug to pile changeovers, and vice versa, in less than three minutes, with the same feeding components. Designed for maximum flexibility, the line also features the fastest product count changes currently available on the market. Enabling biscuit manufacturers to meet different global market requirements, the system is capable of producing multiple packaging variations, from smaller on-the-go packages to larger family packs. The line features horizontal flow wrapping and secondary packaging equipment.

Robotics
Bosch Packaging Technology also launched advancements of its robotic packaging machines at Interpack 2014. Delfi for feed placing into primary packaging and Paloma for placing into primary or secondary packaging are both vision-guided, and now feature the new GD33 Delta robot in a new open frame design for expedited cleaning and simplified operations.

This robot delivers higher speed and payload, broader application range and reduced maintenance time. Both developments are designed to help food producers lower the total cost of ownership (TCO) of primary and secondary packaging equipment and promote food safety.

The GD33 now has 60% fewer components than its predecessors. Integrated with Bosch’s Gemini 4, the fourth generation control and software platform, the higher speed, larger capacity and an improved payload capability up to 3kg increase the pick rate and extend the application range.
Festo handling systems are genuine alternatives to complex and heavy robot systems. Unlike six-axis robots, they can be easily integrated into existing control systems. This reduces programming and servicing costs.

Packaging on the fast track
A technique being called Reaction Technology enables programs created in the function block editor to be executed directly on I/O modules from the company's X20 and X67 series, eliminating internal data transmission.
To achieve this, B&R takes advantage of its Automation Studio 4 development environment to allocate software modules to distributed hardware and utilize the surplus capacity of logic components in the modules. This allows function block libraries to be stored there through the use of dynamic updates. These libraries can then be executed locally on the I/O module like the command set for a microcontroller.

Other high-speed packaging machine functions like code stamping and bad product rejection can synchronise motion control and distributed I/O to achieve absolute precision. Digital output patterns can be controlled with a resolution of 125 ns, and fast input edges such as registration marks or product detection can be recorded with a timestamp of 1 micosecond.
Machine design
France. Every minute, 15,000 patients around the world take a dose of medication produced at GSK Evreux. This high production volume entails a highly complex traceability system.
One of the inhaled forms produced by GSK is the Diskus, a multi-dose powder inhaler that delivers a metered dose of medication. The marking of each Diskus is checked using a three-camera Keyence XG vision system, with its intuitive VisionEditor software toolset.
The first camera uses OCR to check an in-house code that is engraved with a YAG laser. The second checks the placement and diameter of the label; this inspects it for tears and makes sure that the legal notices printed on it are legible. The label is printed on a white background at a rate of 110 to 150 strokes per minute. The last camera is used to check a special label with a black background used for the Japanese market.
"We were looking for a vision system that did not require any direct operator intervention and thus would eliminate the risk of incorrect adjustments," explains Christophe Fourcin of GlaxoSmithKline. "Operators simply enter the code of the product to be inspected into the PLC controlling the vision system. That way they don't have to deal with the complex matter of programming the thirty or so sizes used. The very nature of the detection performed means that we have to routinely make changes to the vision system. We wanted to have a tool that was ours and that we could modify as needed."
DC to AC
By changing from DC to three-phase AC technology, a large global provider of corrugated board plant has considerably improved the energy efficiency of its machines.
To construct its new medium-capacity SteadyLine corrugator, the Bavarian company BHS changed its drive technology completely. AC servo drive technology from Lenze has replaced the previous DC system. Among other things, this opens up welcome opportunities to improve energy efficiency and reduce the incoming power supply.

Corrugated board usually consists of five layers of paper, and a production line thus needs five splicers which can switch from an empty reel of paper to a full one without stopping the production process. BHS uses the Lenze servo drives series 9400 with integrated PLC for the main drive of the unwind and for the braking roller. This ensures reliable and high splicing speeds, even for low-weight paper, as a web tension regulating system has been integrated into the servo controller.
Smaller footprint
Festo's CPX/MPA valve terminal concept is being used by Italian Cama Group for a completely new machine generation.
One characteristic of conventional packaging machines is the large control cabinet outside the main structure of the machine. The controllers within this cabinet are connected to the drives, sensors and valves by a multiplicity of cables and lengths of tubing several metres long.

With the Cama's Breakthrough Generation, the machine footprint is reduced by integrating the control cabinets with the electrical and pneumatic components into the machine pedestal angles. Such a compact machine footprint helps to minimise cabling and makes it easier to access the utility devices.
DC speed control with dynamic braking
Bodine Electric has expanded its family of DC motor speed controls to include a new enclosed model with Forward-Brake-Reverse switch and dynamic braking. The new control is designed for bi-directional applications such as conveyors, packaging machines, screen-printing equipment, food processing applications, medical devices, lab instrumentation and labelling equipment.

This model features a Forward-Brake-Reverse switch, allowing dynamic braking for applications where the motor needs to be manually and infrequently reversed, or when required as a setup function in an application. Five trim pot adjustments (TORQ limit, MIN and MAX speed, acceleration/deceleration, and IR compensation) eliminate the computer-like programming often required in other drives. DIP switches allow the control to be easily calibrated for different motor sizes. Two diagnostic LEDs on the PC board indicate when power is on and when current output is at limit set by the TORQ pot.
Fault detection
Machine malfunctions, slowdowns, and other inefficiencies are problems that plague all production lines. The speed of these machines makes it difficult to isolate problems and the origins of machine jams and other unexpected stoppages are often misinterpreted by line operators and can go unrecorded and uncharacterized.
One problem or malfunction leads to another in a multi-stage system, creating a domino effect and making the original issue difficult to identify. Additionally, problems may be irregular or develop over a long period of time, making it hard to determine what went wrong.
To solve this problem, researchers at Kraft have developed the Remote Observer of Manufacturing Equipment (ROME), that actually reconstructs the events that lead to system failure. Similar to black box flight recorders used on aircraft, ROME is a diagnostic tool designed to support food and beverage machinery. It combines signal-data and video using multiple cameras and provides an integrated time-stamped data bundle.
The LabVIEW graphical system design environment is a key component to this application because it allowed for rapid development of the real-time detection and analysis platform.
ROME includes at least two high-resolution colour video cameras that are scene-specific and acquire data at 30 to 60 frames per second. ROME can accept up to 265 digital inputs (optically insulated input voltage from five to 250 VDC/VAC). ROME also accepts 16 analog signals of 4-20mA (12-bit resolution). The system has a real-time clock and is designed with no outputs to eliminate the possibility of influencing the operation of a machine’s control system.
High-speed frame grabbers give ROME the power to capture up to 10 seconds of video once digital trigger, or fault, is detected for post-analysis. ROME can continuously capture data for up to 80 independent 10-second "events” with a 10 second buffer, meaning at any given time the previous 10 seconds of data is preserved. Also, ROME can monitor machinery equipped with any type/brand of programmable logic controller (PLC).
Key Points
- New Bosch biscuit packaging line capable of of slug to pile changeovers, and vice versa, in less than three minutes
- B&R's Reaction Technology enables programs created in the function block editor to be executed directly on I/O modules
- AC servo drive technology from Lenze has replaces previous DC system at corrugated board plant
- Festo's CPX/MPA valve terminal concept used by Italian Cama Group for a completely new machine generation
- Partnership to accelerate development of AI solutions for future mobility
- UK manufacturers face historic need for automation
- Storing up the benefits
- How IIoT will deliver smarter factories
- Chancellor backs 4IR at parliamentary group launch
- Evolution In the Warehouse
- Connectivity & 5G in UK manufacturing
- Intelligent automation & personalised healthcare
- Elisa Smart Factory & TCS partner to deliver advanced analytics solutions to manufacturing sector
- Research discovers 106% increase in new malware
- Looks Good On Paper
- No Need For Circuit Breakers
- ACCURATE 2D & BARCODING
- No Sensor Readjustment Necessary
- Enhanced Performance From Asynchronous Spindle Motors
- High Accuracy
- KEEPING TENSION UNDER CONTROL
- SWEET SUCCESS OF SINGLE CONTROLLER
- OPENSAFETY STANDARD UNDERPINS NESTLÉ PACKAGING AUTOMATION
- THE ROBOTICS PACKAGE