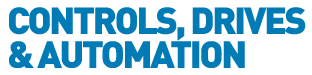
![]() |
Charlotte Stonestreet
Managing Editor |
Home> | MACHINE BUILDING & ENGINEERING | >3D Printing & Prototyping | >3D printing - no threat to automation? |
3D printing - no threat to automation?
05 March 2015
Andy Pye looks at the various methods concerned with 3D printing and looks at the potential impact of the technology on the automation market
Additive layer manufacturing (ALM) – originally known as rapid prototyping and also now known as 3D printing – differs from traditional manufacturing in that it forms items by adding material, usually by printing successive layers of a liquid or gel to form a solid. In contrast, most traditional manufacturing consists of material removal, material forming or assembly.
But despite lots of hype around the idea, there are some fundamental limitations. Initial use of 3D printing has been with a limited range of plastics. It is not quick and cannot be scaled: while automated production processes create large quantities of identical parts at high speed, 3D printers produce single parts. It can take many hours to make a part of only modest size and complexity.
But 3D printing can still revolutionise the production of low-volume parts, particularly those with complex geometry. And not just in plastic: Renishaw's AM250 features a vacuum chamber evacuation followed by high purity argon gas in order to create a high quality atmosphere, crucial when building in reactive materials such as titanium, where oxygen content must be minimised. It is also possible to run the system with non-reactive materials under nitrogen gas.
Rolls-Royce recognises the potential of ALM for producing aero-engine parts, using metal powder melted by electron beam and built ultra-thin layer by layer into complex shapes. The machines are sourced from Swedish company Arcam. Additive layer manufacturing has been used to construct a 1.5m diameter titanium front bearing housing (FBH) which is held inside a Rolls-Royce Trent XWB-97 engine.
The bearing marks the first time ALM has been used to produce such a load-bearing component, rather than by casting or forging. Later this year when an Airbus A380 takes off containing the XWB-97 engine, it will be the first time one has been airborne. The fundamental research behind the process has been carried out at the University of Sheffield.
Iain Todd, Professor of Metallurgy and Materials Processing said: "The barrier has not been the maturity of the technology itself, but the huge programme of testing, research and quality assurance that is needed for a new manufacturing process to gain approval."
Automotive industry
So what about the auto industry? Surely volumes preclude the use of ALM? Not a bit of it - the world's first car with the load-bearing structure and body being integrally 3D printed is the Strati. It has been developed by US start-up Local Motors. In 2014, the company undertook a challenge to build a 3D car live on the internet; in late 2015, the first legal models are expected to be delivered to customers.
The Strati is made from 212 layers of ABS plastic reinforced with carbon fibre. The printing process currently takes 44 hours, but the company hopes to get it down to 24 hours. Some of the electrical and electronic parts will be printed into the car as it is built up by the 3D printing process. Components such as the battery, motor and wiring that cannot yet be printed currently come from a Renault Twizy electric microEV.
According to Peter Harrop, Chairman of technology market research company IDTechEx, future models could benefit from the structural supercapacitor bodywork for cars being developed by Imperial College London, Volvo Geely of China, Vanderbilt University in the USA and Queensland University of Technology in Australia. Load-bearing supercapacitor printed circuit boards from Cambridge University in the UK and in-mould control and lighting electronics from T-Ink in the USA and others are also available.
Instead of vehicles manufactured in a huge central factory, Local Motors plans 100 microfactories in the next 10 years. Your garage perhaps?
Key Points
- Initial use of 3D printing has been with a limited range of plastics; it is not quick and cannot be scaled
- 3D printing can revolutionise the production of low-volume parts, particularly those with complex geometry
- Rolls-Royce uses metal powder melted by electron beam and built ultra-thin layer by layer into complex shapes
- Excellent prognosis for innovation
- Digital adoption critical for an enterprise-led recovery
- Automation firm secures funding for major JLR contract
- PPMA GROUP INDUSTRY AWARDS
- Serving up technology
- UK manufacturers turn to automation to boost domestic capacity amid trade uncertainty
- BICS powers first intelligent exoskeleton with global connectivity
- UK Space Agency to invest £374m per year in European Space Agency
- UK initiative to shape global standards for AI
- Robust barometric pressure sensor